-
- News
- Books
Featured Books
- pcb007 Magazine
Latest Issues
Current IssueSales: From Pitch to PO
From the first cold call to finally receiving that first purchase order, the July PCB007 Magazine breaks down some critical parts of the sales stack. To up your sales game, read on!
The Hole Truth: Via Integrity in an HDI World
From the drilled hole to registration across multiple sequential lamination cycles, to the quality of your copper plating, via reliability in an HDI world is becoming an ever-greater challenge. This month we look at “The Hole Truth,” from creating the “perfect” via to how you can assure via quality and reliability, the first time, every time.
In Pursuit of Perfection: Defect Reduction
For bare PCB board fabrication, defect reduction is a critical aspect of a company's bottom line profitability. In this issue, we examine how imaging, etching, and plating processes can provide information and insight into reducing defects and increasing yields.
- Articles
- Columns
- Links
- Media kit
||| MENU - pcb007 Magazine
Novel High-Performance Substrate for Stretchable Electronics
June 15, 2015 | S. Yoshioka, T. Sawada and T. Abe, Panasonic CorporationEstimated reading time: 1 minute
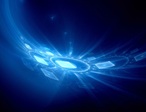
Stretchable circuits are an evolving branch of electronics interconnection technology and the subject of growing interest to product developers seeking to provide novel wearable electronic solutions for consumer and medical markets. Such circuits are designed and manufactured using resilient materials which allow them to expand and contract with the movements of the user or to conform to nonplanar surfaces making possible a wide range of innovative and fanciful electronic interconnection devices. Obviously, the material used is a key element in making a stretchable circuit.
There are a range of different types of thermoplastic polymers available in film form that can be effectively stretched; however, once stretched beyond their elastic limit the material deforms to a new length greater than that which was designed.
There are as well elastomeric materials, such as urethanes, which have seen use in the manufacture of circuits which can be stretched and return to their original length. These materials tend to be opaque, which limits the scope of possibility for their use. A new transparent, high-performance thermal setting stretchable material could open doors to a range of new and innovative products.
New stretchable material characteristics
The new material is capable of stretching to 150% of the original length without hysteresis. (Figure 1 provides a comparison of stress-strain plots of the new material compared with thermoplastic PEN.)
Another key attribute of the material is its ability to reliably return to the original length even when stretched numerous times, as will likely be required in numerous future applications. The new material excels in this regard.
The mechanical and thermal properties of the new material are superior in many important areas including total elongation and adhesion both to copper foil and FR-4 laminate. It is also unique in that is has no melt point making it amenable to soldering with higher temperature lead free solders.
Editor's Note: This article originally appeared in the June 2015 issue of The PCBMagazine.
Suggested Items
Silicon Mountain Contract Services Enhances SMT Capabilities with New HELLER Reflow Oven
07/17/2025 | Silicon Mountain Contract ServicesSilicon Mountain Contract Services, a leading provider of custom electronics manufacturing solutions, is proud to announce a significant upgrade to its SMT production capability with the addition of a HELLER 2043 MK5 10‑zone reflow oven to its Nampa facility.
Knocking Down the Bone Pile: Addressing End-of-life Component Solderability Issues, Part 4
07/16/2025 | Nash Bell -- Column: Knocking Down the Bone PileIn 1983, the Department of Defense identified that over 40% of military electronic system failures in the field were electrical, with approximately 50% attributed to poor solder connections. Investigations revealed that plated finishes, typically nickel or tin, were porous and non-intermetallic.
SHENMAO Strengthens Semiconductor Capabilities with Acquisition of PMTC
07/10/2025 | SHENMAOSHENMAO America, Inc. has announced the acquisition of Profound Material Technology Co., Ltd. (PMTC), a premier Taiwan-based manufacturer of high-performance solder balls for semiconductor packaging.
KYZEN to Highlight Understencil and PCB Cleaners at SMTA Querétaro Expo and Tech Forum
07/09/2025 | KYZEN'KYZEN, the global leader in innovative environmentally responsible cleaning chemistries, will exhibit at the SMTA Querétaro Expo & Tech Forum, scheduled to take place Thursday, July 24, at Centro de Congresos y Teatro Metropolitano de Querétaro.
Driving Innovation: Direct Imaging vs. Conventional Exposure
07/01/2025 | Simon Khesin -- Column: Driving InnovationMy first camera used Kodak film. I even experimented with developing photos in the bathroom, though I usually dropped the film off at a Kodak center and received the prints two weeks later, only to discover that some images were out of focus or poorly framed. Today, every smartphone contains a high-quality camera capable of producing stunning images instantly.