-
- News
- Books
Featured Books
- pcb007 Magazine
Latest Issues
Current IssueThe Hole Truth: Via Integrity in an HDI World
From the drilled hole to registration across multiple sequential lamination cycles, to the quality of your copper plating, via reliability in an HDI world is becoming an ever-greater challenge. This month we look at “The Hole Truth,” from creating the “perfect” via to how you can assure via quality and reliability, the first time, every time.
In Pursuit of Perfection: Defect Reduction
For bare PCB board fabrication, defect reduction is a critical aspect of a company's bottom line profitability. In this issue, we examine how imaging, etching, and plating processes can provide information and insight into reducing defects and increasing yields.
Voices of the Industry
We take the pulse of the PCB industry by sharing insights from leading fabricators and suppliers in this month's issue. We've gathered their thoughts on the new U.S. administration, spending, the war in Ukraine, and their most pressing needs. It’s an eye-opening and enlightening look behind the curtain.
- Articles
- Columns
- Links
- Media kit
||| MENU - pcb007 Magazine
All About Flex: High-Temperature Performance Flexible Circuits
January 21, 2016 | Dave Becker, All FlexEstimated reading time: 2 minutes
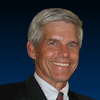
Markets requiring thermal exposure at elevated temperatures include down-hole oil drilling, semiconductor processing, medical diagnostics and a multitude of military/aerospace requirements. But a limitation of flexible circuitry has been performance at extremely high temperatures. For purposes of this discussion, the definition of “extremely high” is temperatures that exceed 150–200°C on a continuous basis or 288°C on an intermittent basis[1]. The flexible circuit industry has made inroads improving this product feature with recent developments and significantly improved high-temperature performance, which is being accomplished with new material constructions requiring some unique fabrication processing.
The adhesive system used to bond the various layers in a flexible circuit is normally considered the weakest link when parts are exposed to high temperature or a harsh chemical environment. This weakness has driven adoption of adhesiveless base laminate technology (the word “laminate” remains an industry term but is a bit misguiding when describing adhesiveless structures as they are not generally produced with a laminating process). Multiple methods for creating an adhesiveless base laminate substrates have become common (copper sputtering, vacuum deposition, cast polyimide) and provide improved performance in both extreme thermal and chemical environments.
But the most frequently used “top side” flexible circuit insulation is generally another layer of polyimide film commonly called coverlay or coverfilm. This layer of film is coated with an uncured adhesive and positioned onto the etched circuitry pattern and then permanently fastened during a temperature/pressure lamination cycle in a platen press. Consequently, an adhesive has been reintroduced into the circuit composite, despite removing the adhesive in the base substrate. Another top side dielectric used in the world of flexible printed circuits is a photo-imaged soldermask, but this material often becomes brittle at elevated temperatures, and can fracture or flake off when bent or folded.
Page 1 of 2
Suggested Items
SHENMAO Strengthens Semiconductor Capabilities with Acquisition of PMTC
07/10/2025 | SHENMAOSHENMAO America, Inc. has announced the acquisition of Profound Material Technology Co., Ltd. (PMTC), a premier Taiwan-based manufacturer of high-performance solder balls for semiconductor packaging.
KYZEN to Highlight Understencil and PCB Cleaners at SMTA Querétaro Expo and Tech Forum
07/09/2025 | KYZEN'KYZEN, the global leader in innovative environmentally responsible cleaning chemistries, will exhibit at the SMTA Querétaro Expo & Tech Forum, scheduled to take place Thursday, July 24, at Centro de Congresos y Teatro Metropolitano de Querétaro.
Driving Innovation: Direct Imaging vs. Conventional Exposure
07/01/2025 | Simon Khesin -- Column: Driving InnovationMy first camera used Kodak film. I even experimented with developing photos in the bathroom, though I usually dropped the film off at a Kodak center and received the prints two weeks later, only to discover that some images were out of focus or poorly framed. Today, every smartphone contains a high-quality camera capable of producing stunning images instantly.
Hands-On Demos Now Available for Apollo Seiko’s EF and AF Selective Soldering Lines
06/30/2025 | Apollo SeikoApollo Seiko, a leading innovator in soldering technology, is excited to spotlight its expanded lineup of EF and AF Series Selective Soldering Systems, now available for live demonstrations in its newly dedicated demo room.
Indium Corporation Expert to Present on Automotive and Industrial Solder Bonding Solutions at Global Electronics Association Workshop
06/26/2025 | IndiumIndium Corporation Principal Engineer, Advanced Materials, Andy Mackie, Ph.D., MSc, will deliver a technical presentation on innovative solder bonding solutions for automotive and industrial applications at the Global Electronics A