-
- News
- Books
Featured Books
- pcb007 Magazine
Latest Issues
Current IssueThe Hole Truth: Via Integrity in an HDI World
From the drilled hole to registration across multiple sequential lamination cycles, to the quality of your copper plating, via reliability in an HDI world is becoming an ever-greater challenge. This month we look at “The Hole Truth,” from creating the “perfect” via to how you can assure via quality and reliability, the first time, every time.
In Pursuit of Perfection: Defect Reduction
For bare PCB board fabrication, defect reduction is a critical aspect of a company's bottom line profitability. In this issue, we examine how imaging, etching, and plating processes can provide information and insight into reducing defects and increasing yields.
Voices of the Industry
We take the pulse of the PCB industry by sharing insights from leading fabricators and suppliers in this month's issue. We've gathered their thoughts on the new U.S. administration, spending, the war in Ukraine, and their most pressing needs. It’s an eye-opening and enlightening look behind the curtain.
- Articles
- Columns
- Links
- Media kit
||| MENU - pcb007 Magazine
Manufacturing Institutes Can Boost the Nation
March 10, 2016 | Dr. John Mitchell, IPCEstimated reading time: 2 minutes
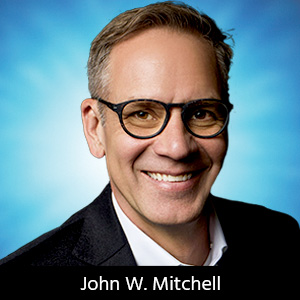
In his most recent State of the Union address, President Obama highlighted a remarkable trend of recent years: the turnaround in many corners of America’s manufacturing sector. Nearly 900,000 new jobs have been created by U.S. manufacturers in the last six years. To accelerate this trend President Obama has promoted the launch of a network of “next-generation” manufacturing hubs— including the new NextFlex Institute in Mountain View, and six others established over the last year.
But the long-term growth outlook is unclear. The number of jobs in the manufacturing sector is still 1.4 million below the level when the recession began in December 2007; and in late 2015 the nation’s leading manufacturing index contracted at its fastest pace since June 2009, following a months-long slide.
Clearly, there is more work to do to shore up U.S. manufacturing, and the innovation hubs mentioned by President Obama are part of the solution.
As proposed by the President in 2012 and authorized by Congress in 2014, the National Network for Manufacturing Innovation (NNMI) is bringing together private companies, government agencies, universities, community colleges, and other state and local organizations with a goal of bridging the gap between basic research and product development. They aim to accelerate innovation by pooling resources and investment in emerging manufacturing technologies with broad applications. The institutes also give companies access to cutting-edge equipment and opportunities for workforce training.
The NextFlex Institute in San Jose, CA announced last August, is the seventh incubator in the network, and the first on the West Coast. Last year, a consortium of 96 companies, 11 laboratories and non-profits, 43 universities, and 15 state and regional organizations, including the City of San Jose, secured an award of $75 million from the Pentagon and $108 million in private funding to launch the “flexible hybrid electronics” initiative.
Unlike traditional circuit boards mounted on rigid green plastic, flexible circuits embedded in fabric or film could pave the way to many exciting innovations: medical implants that conform to bones and organs; lighter communications gear built into military uniforms; or solar cells on a roll of plastic.
IPC has joined NextFlex as a partner and will apply its strength and expertise in standards development to assist the institute in creating roadmaps for industry standards for flexible hybrid electronics manufacturing. Our collaborative efforts will provide the printed electronics community with the standards and education needed to advance this technology, shorten product lead times, and improve product performance.
Other NNMI institutes are focusing on hot areas such as 3D printing, lightweight materials, and advanced semiconductors.
But here again, the good news is tempered by a dose of reality. Congress, the Executive Branch, and all of the institute’s partners must keep up their long-term commitment to adequate funding and coordination.
Congressional appropriators—including Silicon Valley’s Rep. Mike Honda— provided $25 million in 2016 funding for new institutes and $5 million for coordination by the National Institute for Standards and Technology (NIST). This funding level is small in comparison to the scope of the challenge and the demonstrated appetite from the private sector. But the return on investment on even that amount should be huge. Congress will have another opportunity to provide more innovation seed money in the 2017 budget.
In an era of partisan rancor, the bipartisan support for the NNMI reveals a strong consensus in favor of accelerating the nation’s manufacturing sector and reinvesting in America’s technology leadership. Now more than ever, U.S. policymakers need to nurture the green shoots of the manufacturing revival.
Dr. John Mitchell is president of IPC – Association Connecting Electronics Industries, representing an estimated 800,000 people employed in 2,200 U.S. member facilities.
Suggested Items
NEPCON ASIA 2025: Innovating Smart Manufacturing Ecosystems and Bridging Global Opportunities
07/11/2025 | PRNewswireTaking place from October 28 to 30, 2025 at the Shenzhen World Exhibition & Convention Center (Bao'an), NEPCON ASIA is the premier platform to discover the latest technologies and market trends, connect with new suppliers and products, and explore potential partnerships and distribution opportunities.
Mycronic Delivers Strong Q2 Performance and Raises 2025 Outlook to SEK 7.5 Billion
07/11/2025 | MycronicMycronic reported a 35% increase in Q2 net sales and a 27% EBIT margin, prompting an upward revision of its full-year 2025 revenue forecast to SEK 7.5 billion.
Kitron Reports Strengthening Momentum in Q2 2025
07/10/2025 | KitronKitron reported solid quarterly sales and profits, particularly driven by the Defence & Aerospace market sector.
Seeing a Future in Mexico
07/09/2025 | Michelle Te, I-Connect007The Global Electronics Association (formerly known as IPC) has been instrumental in fostering a partnership with Guanajuato, a state north of Mexico City with 12 industrial clusters and close to 150 companies involved in electronics. This past spring, Alejandro Hernández, the undersecretary for investment promotion in Guanajuato, attended IPC APEX EXPO 2025 at the invitation of IPC Mexico Director Lorena Villanueva, where he met with several companies to discuss the opportunities available in Mexico. He is inviting electronics-related companies seeking long-term investment in a centrally located area with access to highways, railways, and ports.
Webinar Review: A Global Trade and Economy in Flux
07/09/2025 | I-Connect007 Editorial TeamIn a July 8 webinar, Global Electronics Association Chief Economist Shawn DuBravac provided a comprehensive analysis of the evolving international trade environment, its implications for inflation, monetary policy, and labor dynamics, and a sober assessment of market valuations. In “Navigating a Shifting Landscape” DuBravac painted a picture of a global economy in flux, where shifting trade alliances and tariff structures are redrawing the supply chain map and influencing the broader economic landscape, while also conveying an overall bullish market outlook.