-
- News
- Books
Featured Books
- pcb007 Magazine
Latest Issues
Current IssueThe Hole Truth: Via Integrity in an HDI World
From the drilled hole to registration across multiple sequential lamination cycles, to the quality of your copper plating, via reliability in an HDI world is becoming an ever-greater challenge. This month we look at “The Hole Truth,” from creating the “perfect” via to how you can assure via quality and reliability, the first time, every time.
In Pursuit of Perfection: Defect Reduction
For bare PCB board fabrication, defect reduction is a critical aspect of a company's bottom line profitability. In this issue, we examine how imaging, etching, and plating processes can provide information and insight into reducing defects and increasing yields.
Voices of the Industry
We take the pulse of the PCB industry by sharing insights from leading fabricators and suppliers in this month's issue. We've gathered their thoughts on the new U.S. administration, spending, the war in Ukraine, and their most pressing needs. It’s an eye-opening and enlightening look behind the curtain.
- Articles
- Columns
- Links
- Media kit
||| MENU - pcb007 Magazine
The Sum of All Parts: Planning for a First-Time-Right PCB Design
May 17, 2016 | Sam Sangani, PNC Inc.Estimated reading time: 2 minutes
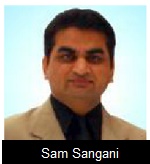
The development of highly integrated and high-speed, chip-based circuit boards brings several functional benefits. But at the same time, these can introduce additional challenges to the actual board itself. Therefore, developing an effective plan for designing, developing, testing and producing the final PCBs is a good business practice.
Lack of communication between PCB designers and PCB fabricators is one of the most significant issues we have faced in our industry. This has led to disconnect in the mutual understanding between these two entities. Subsequently, a scenario has arisen where manufacturers lack the understanding of design guidelines and some designers are not always aware of the manufacturing processes and capabilities of a PCB manufacturer during their design/layout phase.
If we are going to succeed—particularly at the domestic level—we need to open up channels of communication.
Several steps in the PCB design and manufacturing process include areas that allow enhancements that would improve the ease with which boards can be manufactured and decrease the loss rate. Many elements of the process, from the design process to final board test, should be reviewed for improvements that can affect the board’s manufacturability. The ideal way to negate the aforementioned drawbacks would be to design and produce under one roof but, until such a time where this is possible on a large scale, certain measures can be taken to optimize the process as much as possible.
Here are five reasons why designers and PCB manufacturers need to communicate:
1. Critical tolerances vs. yield
With regard to determining what the process can and cannot do, this is a very important factor which affects yield and cost associated in PCB manufacturing.
2. Component placement and solderability
A variation in component density over a PCB surface impacts the uniformity of the soldering of components. Very dense areas may not get enough heat during the reflow process and could result in cold solder joints.
3. Size and uniformity
As the surface area of a PCB gets larger, it brings unwanted irregularities in manufacturing such as the registration of via to pad and warpage on the board surface, making SMT pads or BGA balls unconnected to the PCB. If the proper thickness and stack-up design are taken into account in the initial stages, it would help resolve these types of issues earlier.
4. Transparency
Designers and fabricators working side by side on R&D projects opens up doors not only for the parties involved, but also makes an overall contribution to the industry. Stay up-to-date on new development in processes and technologies. The industry—especially now—is changing rapidly.
5. Long-term business relationships
Once a designer and the PCB manufacturer are actively engaged and get know each other, designers are less likely to try to switch PCB suppliers and start building their relations from scratch. Instead, they can keep building better products when they better understand each other.
Fortunately, communications are moving in the right direction. More and more designers and board houses are starting to engage in productive discussions. Designers are reaching out for plant tours and are developing an interest in the manufacturing process. Golden advice to designers: Do not miss open houses and seminars organized by PCB vendors. Golden advice to PCB suppliers: Do your best to understand designers’ needs.
Sam Sangani is president and CEO of PNC Inc.
Suggested Items
Knocking Down the Bone Pile: Addressing End-of-life Component Solderability Issues, Part 4
07/15/2025 | Nash Bell -- Column: Knocking Down the Bone PileIn 1983, the Department of Defense identified that over 40% of military electronic system failures in the field were electrical, with approximately 50% attributed to poor solder connections. Investigations revealed that plated finishes, typically nickel or tin, were porous and non-intermetallic.
SHENMAO Strengthens Semiconductor Capabilities with Acquisition of PMTC
07/10/2025 | SHENMAOSHENMAO America, Inc. has announced the acquisition of Profound Material Technology Co., Ltd. (PMTC), a premier Taiwan-based manufacturer of high-performance solder balls for semiconductor packaging.
KYZEN to Highlight Understencil and PCB Cleaners at SMTA Querétaro Expo and Tech Forum
07/09/2025 | KYZEN'KYZEN, the global leader in innovative environmentally responsible cleaning chemistries, will exhibit at the SMTA Querétaro Expo & Tech Forum, scheduled to take place Thursday, July 24, at Centro de Congresos y Teatro Metropolitano de Querétaro.
Driving Innovation: Direct Imaging vs. Conventional Exposure
07/01/2025 | Simon Khesin -- Column: Driving InnovationMy first camera used Kodak film. I even experimented with developing photos in the bathroom, though I usually dropped the film off at a Kodak center and received the prints two weeks later, only to discover that some images were out of focus or poorly framed. Today, every smartphone contains a high-quality camera capable of producing stunning images instantly.
Hands-On Demos Now Available for Apollo Seiko’s EF and AF Selective Soldering Lines
06/30/2025 | Apollo SeikoApollo Seiko, a leading innovator in soldering technology, is excited to spotlight its expanded lineup of EF and AF Series Selective Soldering Systems, now available for live demonstrations in its newly dedicated demo room.