-
- News
- Books
Featured Books
- pcb007 Magazine
Latest Issues
Current IssueSales: From Pitch to PO
From the first cold call to finally receiving that first purchase order, the July PCB007 Magazine breaks down some critical parts of the sales stack. To up your sales game, read on!
The Hole Truth: Via Integrity in an HDI World
From the drilled hole to registration across multiple sequential lamination cycles, to the quality of your copper plating, via reliability in an HDI world is becoming an ever-greater challenge. This month we look at “The Hole Truth,” from creating the “perfect” via to how you can assure via quality and reliability, the first time, every time.
In Pursuit of Perfection: Defect Reduction
For bare PCB board fabrication, defect reduction is a critical aspect of a company's bottom line profitability. In this issue, we examine how imaging, etching, and plating processes can provide information and insight into reducing defects and increasing yields.
- Articles
- Columns
- Links
- Media kit
||| MENU - pcb007 Magazine
All About Flex: Flexible Circuit Fabrication and Cleanroom Manufacturing
May 30, 2016 | Dave Becker, All Flex Flexible Circuits LLCEstimated reading time: 1 minute
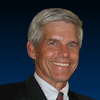
Facility cleanliness is a vital part of process control for flexible circuit fabricators. As higher density requirements continue a relentless drive toward finer traces and spaces, particles and foreign material can cause problems in a number of operations. A particle can cause conductor width and spacing issues at imaging. Conductive material can cause current leaking when trapped under a coverlay or embedded in solder mask. Dirt, dust, or other unintended material may reduce layer-to-layer adhesion. Engineering models suggest hair and fibers can affect insulation resistance and impedance. How big does a particle need to be to cause issues? Consider that typical outdoor ambient air has a normal distribution of particles that can be as small as 0.5 microns and as large as 16 microns. An ultra-high-density flexible circuit might get to 25 micron spacing.
Roughly speaking, one 7−8 micron particle could cause a conductor width and spacing quality criteria violation if it landed on coated resist, or on the photo artwork, or is deposited directly on the photo-sensitive resist during image exposure. With circuitry at ultra-high density, particles in ambient air might cause issues, however, particle size is not the only factor. Quantity and/or density of particles is also a consideration. Ambient air contains 35 million particles per cubic meter, so in an uncontrolled environment, thousands of particles might easily be deposited in a small area. And even if particles don’t settle on material, they can refract collimated light sources that are often used during exposing for creating the circuit image.
These particles also accumulate on work surfaces and are a risk to contaminate in-process materials or operators. It is certainly fair to say the biggest source of contamination is not from ambient air, but the human operator. Human hair is approximately 60 microns in diameter and can be several millimeters in length or longer.
Editor's Note: This article originally appeared in the May 2016 issue of The PCB Magazine.
Suggested Items
Silicon Mountain Contract Services Enhances SMT Capabilities with New HELLER Reflow Oven
07/17/2025 | Silicon Mountain Contract ServicesSilicon Mountain Contract Services, a leading provider of custom electronics manufacturing solutions, is proud to announce a significant upgrade to its SMT production capability with the addition of a HELLER 2043 MK5 10‑zone reflow oven to its Nampa facility.
Knocking Down the Bone Pile: Addressing End-of-life Component Solderability Issues, Part 4
07/16/2025 | Nash Bell -- Column: Knocking Down the Bone PileIn 1983, the Department of Defense identified that over 40% of military electronic system failures in the field were electrical, with approximately 50% attributed to poor solder connections. Investigations revealed that plated finishes, typically nickel or tin, were porous and non-intermetallic.
SHENMAO Strengthens Semiconductor Capabilities with Acquisition of PMTC
07/10/2025 | SHENMAOSHENMAO America, Inc. has announced the acquisition of Profound Material Technology Co., Ltd. (PMTC), a premier Taiwan-based manufacturer of high-performance solder balls for semiconductor packaging.
KYZEN to Highlight Understencil and PCB Cleaners at SMTA Querétaro Expo and Tech Forum
07/09/2025 | KYZEN'KYZEN, the global leader in innovative environmentally responsible cleaning chemistries, will exhibit at the SMTA Querétaro Expo & Tech Forum, scheduled to take place Thursday, July 24, at Centro de Congresos y Teatro Metropolitano de Querétaro.
Driving Innovation: Direct Imaging vs. Conventional Exposure
07/01/2025 | Simon Khesin -- Column: Driving InnovationMy first camera used Kodak film. I even experimented with developing photos in the bathroom, though I usually dropped the film off at a Kodak center and received the prints two weeks later, only to discover that some images were out of focus or poorly framed. Today, every smartphone contains a high-quality camera capable of producing stunning images instantly.