-
-
News
News Highlights
- Books
Featured Books
- pcb007 Magazine
Latest Issues
Current IssueThe Hole Truth: Via Integrity in an HDI World
From the drilled hole to registration across multiple sequential lamination cycles, to the quality of your copper plating, via reliability in an HDI world is becoming an ever-greater challenge. This month we look at “The Hole Truth,” from creating the “perfect” via to how you can assure via quality and reliability, the first time, every time.
In Pursuit of Perfection: Defect Reduction
For bare PCB board fabrication, defect reduction is a critical aspect of a company's bottom line profitability. In this issue, we examine how imaging, etching, and plating processes can provide information and insight into reducing defects and increasing yields.
Voices of the Industry
We take the pulse of the PCB industry by sharing insights from leading fabricators and suppliers in this month's issue. We've gathered their thoughts on the new U.S. administration, spending, the war in Ukraine, and their most pressing needs. It’s an eye-opening and enlightening look behind the curtain.
- Articles
- Columns
- Links
- Media kit
||| MENU - pcb007 Magazine
Estimated reading time: 1 minute
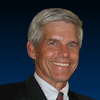
All About Flex: Flexible Circuit Fabrication and Cleanroom Manufacturing
Facility cleanliness is a vital part of process control for flexible circuit fabricators. As higher density requirements continue a relentless drive toward finer traces and spaces, particles and foreign material can cause problems in a number of operations. A particle can cause conductor width and spacing issues at imaging. Conductive material can cause current leaking when trapped under a coverlay or embedded in solder mask. Dirt, dust, or other unintended material may reduce layer-to-layer adhesion. Engineering models suggest hair and fibers can affect insulation resistance and impedance. How big does a particle need to be to cause issues? Consider that typical outdoor ambient air has a normal distribution of particles that can be as small as 0.5 microns and as large as 16 microns. An ultra-high-density flexible circuit might get to 25 micron spacing.
Roughly speaking, one 7−8 micron particle could cause a conductor width and spacing quality criteria violation if it landed on coated resist, or on the photo artwork, or is deposited directly on the photo-sensitive resist during image exposure. With circuitry at ultra-high density, particles in ambient air might cause issues, however, particle size is not the only factor. Quantity and/or density of particles is also a consideration. Ambient air contains 35 million particles per cubic meter, so in an uncontrolled environment, thousands of particles might easily be deposited in a small area. And even if particles don’t settle on material, they can refract collimated light sources that are often used during exposing for creating the circuit image.
These particles also accumulate on work surfaces and are a risk to contaminate in-process materials or operators. It is certainly fair to say the biggest source of contamination is not from ambient air, but the human operator. Human hair is approximately 60 microns in diameter and can be several millimeters in length or longer.
Editor's Note: This article originally appeared in the May 2016 issue of The PCB Magazine.
More Columns from All About Flex
All About Flex: Terms and ConditionsAll About Flex: ISO 9001 Basics
All About Flex: FAQs on UL Listings for Flexible Circuits
All About Flex: Avoiding Trace Fracturing in a Flexible Circuit
Polyimide vs. Silicone for Flexible Heaters
All About Flex: Copper Thickness Requirements for Flex Circuits
All About Flex: Copper Grain Direction
All About Flex: Options for Purchasing Flexible Heaters