-
- News
- Books
Featured Books
- pcb007 Magazine
Latest Issues
Current IssueSales: From Pitch to PO
From the first cold call to finally receiving that first purchase order, the July PCB007 Magazine breaks down some critical parts of the sales stack. To up your sales game, read on!
The Hole Truth: Via Integrity in an HDI World
From the drilled hole to registration across multiple sequential lamination cycles, to the quality of your copper plating, via reliability in an HDI world is becoming an ever-greater challenge. This month we look at “The Hole Truth,” from creating the “perfect” via to how you can assure via quality and reliability, the first time, every time.
In Pursuit of Perfection: Defect Reduction
For bare PCB board fabrication, defect reduction is a critical aspect of a company's bottom line profitability. In this issue, we examine how imaging, etching, and plating processes can provide information and insight into reducing defects and increasing yields.
- Articles
- Columns
- Links
- Media kit
||| MENU - pcb007 Magazine
All About Flex: Creating Via Holes in Flexible Laminates
July 28, 2016 | Dave Becker, All Flex Flexible Circuits LLCEstimated reading time: 4 minutes
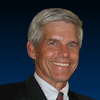
Almost all double-sided and multilayer flexible circuits require through-holes or vias to enable an electrical connection between conductive layers. Creating a reliable plated via requires several critical steps. The first one is creating the through-hole.
Typical methods for creating through-holes in flexible laminates are:
- Numerically controlled drilling
- Laser drilling
- Hard tool punching
Numerically Controlled Drilling
Numerically controlled (NC) drilling is the most common method used in flexible circuit and printed circuit board manufacturing. Panels can be stacked several layers high and are sandwiched between entry and exit materials to ensure cleanly cut holes. Many NC drilling machines have multiple spindles, which allow multiple holes to be drilled simultaneously. Multiple spindle drilling combined with stacking make NC drilling a very efficient operation with a locational accuracy of about +0.001” from hole to hole. This technology has been around for decades but remains the workhorse process for making holes in panels of flexible and rigid circuit board material.
Drill bits can come in all shapes and sizes; most are carbide steel. The bit has angular sharp grooves that evacuate the material by a shredding action as the rotation of the drill cuts then pulls the material out of the way. The smaller the via diameter, the faster the drill should spin to achieve maximum cutting efficiency. Drill sizes may be as large as 0.250” for creating tooling locations and can go down to about 0.005” for the creation of electrical vias. While customers frequently ask “what is the smallest via you can drill?” practically speaking, an 0.008” diameter is close to the lower limit for efficient volume production.
While the side view of a drilled hole is smooth to the naked eye, it actually has spiraling microgrooves along the sidewall. Most substrates are composites with layers of copper, adhesive and polyimide. This complicates drilling as it must cut cleanly through several different types of materials. Drill bits can get hot and soften the adhesive, smearing it around the diameter of the hole. The bit temperature is a function of drill speed and the design of the bit. Optimal bit designs maximize material evacuation while minimizing temperature rise. Adhesive smear can create an insulation layer around the circumference of the drilled hole. This can prevent the copper plating from creating the layer-to-layer electrical connection. As a result, many double-sided and multilayer circuits are next processed through a plasma desmear operation to remove this dielectric layer.
Laser Drilling
In laser drilling, a highly focused beam of energy ablates or vaporizes the material. The laser beam consists of pulses of various intensities and wavelengths. Laminates comprised of multiple materials such as copper, polyimide and adhesive require specific process algorithms to address the material differences, since different materials ablate at different laser settings. Polyimide and adhesive are quickly removed while copper is much slower and requires increased energy. While NC drilling can handle a stack of multiple layers of material, laser drilling is only performed on a single substrate layer.
Virtually any size or shape opening can be created with laser drilling. The larger the hole, the more energy required and the higher the cost. Lasers can drill very small holes, but for flexible circuits, via sizes smaller than 0.002” may be difficult to plate due to the inherent limitations of the plating chemistries and processes. For high-density circuits with vias in the 0.002” to 0.006” range, laser drilling is often preferred over NC drilling. NC drilling would most likely be preferred for larger vias because of the higher throughput rate.
Laser drilling can be highly controlled in the X, Y and Z directions as well as be tuned to selectively ablate specific materials. This capability makes the technology useful for multilayer fabrication where blind and buried vias are required. It is also used to create dual access openings on top and bottom sides of a single-sided circuit by selectively removing polyimide and adhesive. Even with a finely tuned laser output, there is often some carbon debris remaining in the hole requiring removal. This is usually accomplished with a plasma etch process. Alternative chemical cleaning processes are also employed.
Punching
Punching vias is usually performed using a male-female die set. The upper section of the tool is a punch and the lower part is the die. Laminate is placed between the upper and lower plate. The top punch is pushed into the material and a sheering action creates the hole. The slug created by the punch is pushed through the lower die plate.
Punching is the least frequently used process for flexible circuit fabrication, especially for low volume or quick turn parts. It does find favor with ultra-high volume, lower density circuits and lends itself well to continuous reel-to-reel circuit fabrication. Die sets can be quite expensive depending on the number and size of holes in the pattern. A die set can be built to accommodate a variety of shapes and sizes but this process has limitations for creating vias in high density circuit applications. For most manufacturers, 0.015” to 0.020” diameter punches are the practical limitation for via size with a punch tool.
Of the three methods, punching puts the highest level of mechanical stress on the substrate. At a microscopic level, a punched hole will look deformed when compared to NC or laser drilling. A dull punch can result in the substrate layers pulling apart, or the adhesive layer smearing over the copper part of the sidewall. This can cause problems at plating and result in a poorly metalized through-hole. An undetected broken punch is also an obvious problem.
Hard tooling, NC drilling, and laser drilling all have advantages and disadvantages in flexible circuit processing. The preferred method depends on circuit density, production volume and laminate configuration. From a plating standpoint, there are no inherent advantages among the three alternatives.
Dave Becker is vice president of sales and marketing at All Flex Flexible Circuits LLC.
Suggested Items
I-Connect007 Editor’s Choice: Five Must-Reads for the Week
07/18/2025 | Nolan Johnson, I-Connect007It may be the middle of the summer, but the news doesn’t quit, and there’s plenty to talk about this week, whether you’re talking technical or on a global scale. When I have to choose six items instead of my regular five, you know it’s good. I start by highlighting my interview with Martyn Gaudion on his latest book, share some concerning tariff news, follow that up with some promising (and not-so-promising) investments, and feature a paper from last January’s inaugural Pan-European Design Conference.
Elephantech Launches World’s Smallest-Class Copper Nanofiller
07/17/2025 | ElephantechJapanese deep-tech startup Elephantech has launched its cutting-edge 15 nm class copper nanofiller – the smallest class available globally. This breakthrough makes Elephantech one of the first companies in the world to provide such advanced material for commercial use.
Copper Price Surge Raises Alarms for Electronics
07/15/2025 | Global Electronics Association Advocacy and Government Relations TeamThe copper market is experiencing major turbulence in the wake of U.S. President Donald Trump’s announcement of a 50% tariff on imported copper effective Aug. 1. Recent news reports, including from the New York Times, sent U.S. copper futures soaring to record highs, climbing nearly 13% in a single day as manufacturers braced for supply shocks and surging costs.
I-Connect007 Editor’s Choice: Five Must-Reads for the Week
07/11/2025 | Andy Shaughnessy, Design007 MagazineThis week, we have quite a variety of news items and articles for you. News continues to stream out of Washington, D.C., with tariffs rearing their controversial head again. Because these tariffs are targeted at overseas copper manufacturers, this news has a direct effect on our industry.I-Connect007 Editor’s Choice: Five Must-Reads for the Week
Digital Twin Concept in Copper Electroplating Process Performance
07/11/2025 | Aga Franczak, Robrecht Belis, Elsyca N.V.PCB manufacturing involves transforming a design into a physical board while meeting specific requirements. Understanding these design specifications is crucial, as they directly impact the PCB's fabrication process, performance, and yield rate. One key design specification is copper thieving—the addition of “dummy” pads across the surface that are plated along with the features designed on the outer layers. The purpose of the process is to provide a uniform distribution of copper across the outer layers to make the plating current density and plating in the holes more uniform.