-
-
News
News Highlights
- Books
Featured Books
- smt007 Magazine
Latest Issues
Current IssueIPC APEX EXPO 2025: A Preview
It’s that time again. If you’re going to Anaheim for IPC APEX EXPO 2025, we’ll see you there. In the meantime, consider this issue of SMT007 Magazine to be your golden ticket to planning the show.
Technical Resources
Key industry organizations–all with knowledge sharing as a part of their mission–share their technical repositories in this issue of SMT007 Magazine. Where can you find information critical to your work? Odds are, right here.
The Path Ahead
What are you paying the most attention to as we enter 2025? Find out what we learned when we asked that question. Join us as we explore five main themes in the new year.
- Articles
- Columns
Search Console
- Links
- Media kit
||| MENU - smt007 Magazine
Koh Young Discusses Latest 3D AOI Innovations
June 16, 2017 | Stephen Las Marias, I-Connect007Estimated reading time: 6 minutes
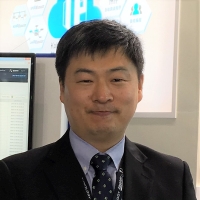
At the recent NEPCON China event in Shanghai, I caught up with Koh Young Technology’s Overseas Sales Team Manager Scott Kim, to talk about the latest challenges and developments happening in inspection technologies. We also discussed the key factors to consider when it comes to buying inspection systems.
Stephen Las Marias: Scott, what are the new demands or requirements from your customers when it comes to inspection?
Scott Kim: Recently, more and more customers want to have 3D based technology, especially for measuring component heights. Previously, customers once checked the defects based on 2D technology, but now it's already moved to 3D. 3D has almost become the standard in this industry.
Las Marias: What’s the key factor here for users to move to 3D?
Kim: The key factors are the false-call rate, escape rate and productivity. Comparing 2D inspection technology to 3D, there’s a big gap when it comes to these parameters. So, more and more customers, once they evaluate a 3D AOI system, and compare the performance to their existing 2D systems, eventually they select 3D for their inspection technology.
Las Marias: Does it make sense to have both 2D and 3D inspection systems in a line?
Kim: Yes, as there’s another key difference between 2D and 3D technology. In 2D, usually you just find the defects. Normally, 2D users are focusing on just defect rejects without paying attention to false calls. Meanwhile, 3D is different. We are measuring something, not just detecting defects.
For instance, we measure the height so that we have data, and based on that data, we set the tolerance. Beyond that tolerance means a defect, and within the tolerance, it’s a pass. So, before having a reject, we have measurement data, which is the key advantage of 3D AOI. We can utilize the measurement data. It’s a really big data, which includes volume information and offsets, everything. With that measurement data, you can optimize and improve the process. Eventually you will get very good productivity. That's the key factor of the 3D AOI.
Las Marias: How do you help your customers understand this so that they can fully appreciate the benefits they can get in 3D?
Kim: To persuade customers and help them understand the concept of 3D AOI, we need a tool. That’s the software. Without a good, easy-to-use software, we cannot convince customers. That’s what we are emphasizing today. That is the multi-line concept of production management, based on an intelligent platform. Intelligent platform means automation and more intelligent management provided by artificial intelligence. We are putting a lot of resource to develop that area. Eventually, we want to make more automation and less human element in inspection.
Without having that kind of strong, powerful software technology or automation, it’s garbage. You cannot handle such big data. Therefore, someone needs to help to analyze the data. That’s one of the things that we are targeting and we are focusing on. More automation and more intelligent software platforms.
Las Marias: What is your strategy towards Industry 4.0?
Kim: Our strategy for Industry 4.0 is a multi-line management concept. Previously, many customers had multiple lines, for example, 10 lines and 10 pieces of inspection equipment. This means the user has to manage 10 times of work because each system has no correlation. Although in the modern day, everything is the same, but actually they work differently. For 3D technology, as I mentioned, we have measuring data. If we calibrate the system, the measurement data should be equal regardless of environmental change.
That means we can do centralized management. That's one of the things which we are targeting for Industry 4.0. A centralized concept so it doesn't matter if it’s 10 systems or 100 systems, they will all work like one system.
Las Marias: What other developments are happening in the 3D AOI space?
Kim: This year we are introducing another new technology. For example, although we have 3D technology, actually the camera projects from top. It means we get the information from the top. That's one of the limitations for 3D AOI. You cannot see beneath the components. This time, we introduced a camera technology from the side as well. Now we can cover both the top and side. Conventionally, 2D AOI also has a side camera solution as an option, but this time, what's different between our 3D side camera and those of the others is that we developed our side camera with 3D technology, which is why we call it a 3D multi-measurement camera.
We use four side cameras, but each side camera has 3D information—the same as the top camera. For example, there’s a solder joint. If we use the top camera, maybe the information is limited. We still have 3D, but the information is limited. However, if you use the side cameras as well in 3D, you will get solder joint shape, volume, height, everything. It’s much more accurate than just having the top camera. And then we combine both data to deliver our customer a perfect solution.
Las Marias: Previously, manufacturers say inspection doesn't add value. But nowadays, there is an increasing effort to install inspection systems in electronics assembly lines. What changed?
Kim: The main change is the size of the component and the density of the component. Previously, the components were bigger, so inspection can be done by operators without any problem. However, component sizes now have become smaller and smaller, and PCB assemblies have become denser. It's very difficult to control the production and therefore the defects. It’s necessary to use an automated inspection system.
However, it also leads to another issue. If the equipment isn’t accurate, it causes more false calls, therefore the operator still must check whether the false calls are indeed false calls or a real defect. For customers, it means higher cost and more human resources. Just because you are using an automated optical inspection system doesn’t mean your inspection is good. You need to use the accurate equipment to save you cost.
Las Marias: Having said that, what are the key factors to consider when it comes to 3D AOI?
Kim: Customer now are using very small-sized chips and components, so they should check whether 3D AOI is the type of the tool that can inspect for defects from the small sized components—which the normal 2D AOI couldn't check properly. That's the first one. Second, the labor cost is increasing nowadays, so customers should use an automated system without too many false calls to make their work easier and simpler. Now, we are even targeting automated programming and automated fine tuning. Eventually we think we can realize unmanned production by AI technology. So that's also the reason why we are putting a lot of resource into developing our AI technology, not just the equipment itself.
Las Marias: Scott, is there anything else you would like to talk about?
Kim: Other than the software and some accurate machine performance, we still have many new applications that can deliver good benefits for the customers. For example, we introduced a new feature in the SPI system. Conventionally, the inspection system only checks for defects, but this time, we delivered a solder dispensing solution with SPI, in which the SPI inspects the defect, for example, in soft shell solder or no solder pad. And then it can dispense solder and improve the solder joint. This can help improve the production yield.
Las Marias: Scott, thank you very much for your time.
Kim: You're welcome.
Suggested Items
KYZEN to Highlight Stencil and Cleaning Solutions at SMTA Monterrey
03/27/2025 | KYZEN'KYZEN, the global leader in innovative environmentally friendly cleaning chemistries, will exhibit at the SMTA Monterrey Expo & Tech Forum scheduled to take place on Thursday, April 10 at the Cintermex Convention Center in Monterrey, Nuevo León. KYZEN cleaning experts will be on-site highlighting stencil cleaning chemistries KYZEN E5631J and CYBERSOLV C8882.
Indium to Showcase Proven EV Products and High-Reliability Alloys at Productronica China
03/26/2025 | Indium CorporationAs a global materials supplier and trusted partner in electric vehicle (EV) and e-Mobility manufacturing, Indium Corporation® is proud to showcase its high-reliability alloys and soldering solutions at Productronica China, March 26-28, in Shanghai, China.
SolderKing Enhances Brainboxes' Electronics Manufacturing with Expert Support and Advanced Materials
03/26/2025 | SolderKingIn modern electronics manufacturing, success relies on more than high-quality soldering materials. Technical knowledge and process expertise are just as crucial for achieving consistent results. SolderKing, a leading UK manufacturer, provides both, combining advanced consumables with specialist support to help manufacturers optimise their soldering processes.
AIM to Highlight Type 5 Solder and Other Leading Products at SMTA Monterrey Expo & Tech Forum
03/20/2025 | AIM SolderAIM Solder, a leading global manufacturer of solder assembly materials for the electronics industry, is pleased to announce its participation in the upcoming SMTA Monterrey Expo & Tech Forum taking place on April 10 at Cintermex in Monterrey, Nuevo Leon, Mexico.
Hentec Industries/RPS Automation to Showcase Valence 2508 at IPC Expo 2025
03/17/2025 | Hentec Industries/RPS AutomationThe Valence 2508 Selective Soldering System is engineered for high-mix, high-volume, advanced PCB production. It supports boards ranging from 25 x 25 mm to 559 x 559 mm (1 x 1 in. to 22 x 22 in.), with a maximum processing area of 508 x 508 mm (20 x 20 in.).