-
- News
- Books
Featured Books
- smt007 Magazine
Latest Issues
Current IssueDo You Have X-ray Vision?
Has X-ray’s time finally come in electronics manufacturing? Join us in this issue of SMT007 Magazine, where we answer this question and others to bring more efficiency to your bottom line.
IPC APEX EXPO 2025: A Preview
It’s that time again. If you’re going to Anaheim for IPC APEX EXPO 2025, we’ll see you there. In the meantime, consider this issue of SMT007 Magazine to be your golden ticket to planning the show.
Technical Resources
Key industry organizations–all with knowledge sharing as a part of their mission–share their technical repositories in this issue of SMT007 Magazine. Where can you find information critical to your work? Odds are, right here.
- Articles
- Columns
Search Console
- Links
- Media kit
||| MENU - smt007 Magazine
On the Smart Move: Industry 4.0 in Electronics Production
August 25, 2017 | Günter Schindler, ASM Assembly Systems GmbH & Co. KGEstimated reading time: 12 minutes
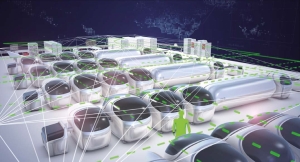
Industry 4.0—googling this still very young term gives you approximately 200 million hits, almost as many as you get when you enter "automation", a term that has been around for decades. When you add alternative or supplemental terms like industrial Internet, smart factory or Internet of Things (IoT), the number of hits grows even larger. These are indicators that the industrial world is in motion, as we face a revolution in terms of processes, organizational structures, hardware and software in our companies.
Many critics complain that terms like Industry 4.0 and smart factory are rather arbitrary and lack concrete meaning. That is correct. What is also true, however, is that technical progress always starts out with a vision, which is then put into concrete terms as time moves on.
In this paper, I want to help put this visionary force to use while filling these new concepts with life in the field of electronics manufacturing. In concrete terms: what tasks must electronics manufacturers perform in order to implement these new production concepts in their factories?
A Market-Driven Development
Advances in automation have rapidly reduced the costs of mass production while delivering huge jumps in efficiency in recent decades. Refinements like enhanced specialization and the division of labor between companies, lean manufacturing, process and value chain orientation and the use of IT-supported communication have further enhanced its positive impact on cost, quality, product diversity, and cycle times.
But today’s global markets demand even more. Products must be offered in more and increasingly customized variants while product life cycles are getting shorter and shorter. For electronics manufacturers, this means having to accommodate ever smaller lot sizes and more frequent product changeovers. On top of this, globalized markets are extremely volatile. Trendy products must be available in huge quantities immediately after they have been announced (and sometimes long before), while other products disappear shortly after they have been introduced to the market. OEMs regularly outsource their production operations and are quick to shift them to other parts of the world if other service providers can do the job better or adapt more efficiently to the OEM’s processes. Regional, political and economic crises affect markets and demand all over the world.
As a result, production facilities must become more flexible and be able to respond quickly to product changes by scaling their capacities up or down in line with demand. For SMT plants, this means that classic production concepts, rigid line concepts and the inflexible planning and control hierarchies from the age of mass production are no longer capable of keeping up.
It should therefore come as no surprise that the production concepts we are talking about are making headlines all over the world. New technologies like the Internet of Things (IoT), machine-to-machine communication, more flexible software architectures and big data create new opportunities for companies that have to find answers to the changing requirements of their markets.
Part 1: Connectivity and Security
The first prerequisite for the implementation of Industry 4.0 is the consistent networking of machines, production lines and locations. What seems like matter-of-course in an electronics manufacturer’s office turns out to be a challenge on the factory floor, though.
Printers, SPI systems, placement machines, reflow ovens and AOI systems—even single lines often consist of machines from many different manufacturers. Cross-machine data communication is still more the exception than the rule, because there are no generally accepted standards for protocols and interfaces. This is an area where manufacturers and international industry associations must quickly approve and establish minimum standards, because it is the only way to keep integration costs on a reasonable level for electronics manufacturers. If Industry 4.0 is to become reality, networking your production equipment must become a lot easier and simpler.
To put it succinctly, the machine of the future will produce not only products but data, which it then makes available to other systems as an open service on the network. With modern bus systems and contemporary software, this does not pose a technical problem—web interfaces are already a standard feature on many of these machines. The general recommendation for the electronics industry is therefore to establish standards that are based largely on those in the IT industry. The systems must be able to read data from the machine in real time (status and progress messages, error messages, sensor data, etc.) as well as control machine parameters. Initiatives of equipment manufacturers who publish their interfaces are a good start.
Future components in an SMT line should function similar to printers on an office network. They integrate themselves automatically, provide performance, status and diagnostic information to all authorized entities, and can be configured individually and remotely for each process.
The electronics manufacturer can then decide which of this information he wants to use for his processes. For example, many of our customers already use the fill level data from our placement machines to automatically request fresh supplies from the warehouse long before the component reel runs empty. Innovative, modular and highly compact storage systems will soon be able to perform this job directly on the line. Engineers are even working on systems that can set up refills automatically with no human interaction.
Besides this type of horizontal networking on the production and shop floor level, the vertical integration with MES and ERP systems is another point that engineers are working on. Their goal: making the entire production with all its resources fully transparent. Many special tasks in the areas of programming, planning and optimization can be performed anywhere in the world, and the results of this work can be put to use instantly in any of the company’s locations.
The next networking stage will be between companies, which enables customers to call up information from their suppliers directly in the form of regular reports or even in real time via dashboards. Orders from end customers can trigger schedule changes or new production orders at the EMS provider, and suppliers can be notified automatically of any changes in demand.
On the other hand, new capabilities like these also entail new risks, especially with regard to IT security. BOMs, CAD drawings, component prices, production quantities, product plans—all of these are data that needs to be protected. Large EMS companies are already spending a lot of money to keep information from reaching other customers or third parties.
Page 1 of 3
Suggested Items
Intervala Hosts Employee Car and Motorcycle Show, Benefit Nonprofits
08/27/2024 | IntervalaIntervala hosted an employee car and motorcycle show, aptly named the Vala-Cruise and it was a roaring success! Employees had the chance to show off their prized wheels, and it was incredible to see the variety and passion on display.
KIC Honored with IPC Recognition for 25 Years of Membership and Contributions to Electronics Manufacturing Industry
06/24/2024 | KICKIC, a renowned pioneer in thermal process and temperature measurement solutions for electronics manufacturing, is proud to announce that it has been recognized by IPC for 25 years of membership and significant contributions to electronics manufacturing.
Boeing Starliner Spacecraft Completes Successful Crewed Docking with International Space Station
06/07/2024 | BoeingNASA astronauts Barry "Butch" Wilmore and Sunita "Suni" Williams successfully docked Boeing's Starliner spacecraft to the International Space Station (ISS), about 26 hours after launching from Cape Canaveral Space Force Station.
KIC’s Miles Moreau to Present Profiling Basics and Best Practices at SMTA Wisconsin Chapter PCBA Profile Workshop
01/25/2024 | KICKIC, a renowned pioneer in thermal process and temperature measurement solutions for electronics manufacturing, announces that Miles Moreau, General Manager, will be a featured speaker at the SMTA Wisconsin Chapter In-Person PCBA Profile Workshop.
The Drive Toward UHDI and Substrates
09/20/2023 | I-Connect007 Editorial TeamPanasonic’s Darren Hitchcock spoke with the I-Connect007 Editorial Team on the complexities of moving toward ultra HDI manufacturing. As we learn in this conversation, the number of shifting constraints relative to traditional PCB fabrication is quite large and can sometimes conflict with each other.