-
-
News
News Highlights
- Books
Featured Books
- smt007 Magazine
Latest Issues
Current IssueIPC APEX EXPO 2025: A Preview
It’s that time again. If you’re going to Anaheim for IPC APEX EXPO 2025, we’ll see you there. In the meantime, consider this issue of SMT007 Magazine to be your golden ticket to planning the show.
Technical Resources
Key industry organizations–all with knowledge sharing as a part of their mission–share their technical repositories in this issue of SMT007 Magazine. Where can you find information critical to your work? Odds are, right here.
The Path Ahead
What are you paying the most attention to as we enter 2025? Find out what we learned when we asked that question. Join us as we explore five main themes in the new year.
- Articles
- Columns
Search Console
- Links
- Media kit
||| MENU - smt007 Magazine
Rework and Reliability: Less is More!
September 15, 2017 | Karen Tellefsen, Alpha Assembly SolutionsEstimated reading time: 4 minutes
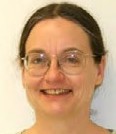
Circuit boards are not always perfect after reflow or wave soldering. Scrapping boards with one or two defects is expensive, so rework happens. A good concept for rework is less is more, especially less flux. Use as little rework flux as possible, as in the old Brylcreem ads, "Just a little dab'll do ya."
Liquid flux for rework is often supplied in felt-tipped applicator pens that make applying a few microliters of flux to a solder joint easy. Small squeeze bottles with tiny needle tips also work well. Paste/gel flux can be supplied in small syringes; use a small applicator tip to ensure that only a small dot of flux is applied to the rework site. Of course, using only no-clean, flux-cored solder wire without any assisting flux is the most electrochemically reliable way to do no-clean rework. The core flux in the wire will be properly heat deactivated because it will not flow until the wire is melted. Additionally, because core flux is mostly rosin or resin and hard, any activator remaining will be trapped in the flux residue. No-clean core fluxes are usually light colored and glass-like in appearance, providing nice cosmetics.
Most low solids, no-clean soldering fluxes must be exposed to soldering temperatures to become deactivated. The activator systems of these fluxes contain organic acids that remove oxides and allow solder to wet. When these organic acids are exposed to high enough temperatures for a long enough time, the activators volatilize and go away. If this doesn’t happen, the unheated or under-heated flux residues can allow electrochemical failures to occur, such as corrosion, reduction of insulation resistance, and, worst of all, electrochemical migration (Figure 1). If too much flux is applied to a rework site, some of the flux can move to nearby parts of the board that will not be exposed to the heat of the soldering tool. This often happens when flux is dispensed in large squeeze bottles with coarse tips. All those spikes in the SIR of the unheated flux are caused by the formation of dendrites between conductors.
Figure 1: SIR measurement of heated and unheated liquid, low-solids, no-clean flux.
So, how do unheated flux residues (and other contaminants) allow electrochemical problems to happen? A diagram showing these failure mechanisms is given in Figure 2. Many flux residues are hygroscopic, that is they absorb moisture from the air. This forms an electrolytic film on the board. The presence of this film allows small currents to flow between conductors at different voltages, reducing the surface insulation resistance (SIR). In some cases, the small current may cause electrolytic corrosion, which is the dissolution of metal from positively biased conductors. This rarely will cause a conductor to be completely eaten away and become an open circuit. It also can provide metal cations in the electrolyte film.
Figure 2: Electrochemical failure mechanisms caused by contaminants on circuit boards.
Now comes the worse and most destructive failure, electrochemical migration (ECM). Those metal ions in the electrolyte film will migrate to the cathodic, or negatively bias conductor because of the electrical field between the two conductors. When the metal cation gets to the cathode, it can pick up some electrons and deposit on the conductor. This deposition will usually occur at high energy locations, causing the formation of tree-like structures called dendrites. These dendrites will grow all the way to the opposing conductor causing a short circuit. These dendrites are delicate and can be destroyed by the resistive heating current flowing though the thin conductor. Noise results from the repeated forming and breaking of the dendrites, as seen in Figure 1.
Only J-STD-004B type -L0 and -L1 fluxes should be used for no-clean rework; fluxes that contain some rosin or a similar encapsulating resin, such as ROL0 and REL1, are even better. The rosin or resin in the flux will harden and help trap activators that weren’t completely heat deactivated.
Some circuit assemblers clean reworked areas with isopropyl alcohol or another solvent. For no-clean material rework, this is usually done for cosmetic reasons and more likely to hurt the electrochemical reliability than help it. No-clean fluxes are designed to be left on the circuit board. Spot cleaning may only move the dirt around. For circuits boards that are usually cleaned, spot cleaning reworked areas are not recommended. The board should be reworked with washable fluxes, and it should be put through the usual washing process again to ensure all rework fluxes are adequately removed from the board. This is especially important if the finished circuit is to be conformally coated, as coating over some flux residues can be worse than not coating at all.
In conclusion, be careful not to leave excessive or improperly heated flux residues after reworking circuit boards, or you might have more problems.
This article was originally published in the September 2017 issue of SMT Magazine.
Suggested Items
KYZEN to Highlight Stencil and Cleaning Solutions at SMTA Monterrey
03/27/2025 | KYZEN'KYZEN, the global leader in innovative environmentally friendly cleaning chemistries, will exhibit at the SMTA Monterrey Expo & Tech Forum scheduled to take place on Thursday, April 10 at the Cintermex Convention Center in Monterrey, Nuevo León. KYZEN cleaning experts will be on-site highlighting stencil cleaning chemistries KYZEN E5631J and CYBERSOLV C8882.
Indium to Showcase Proven EV Products and High-Reliability Alloys at Productronica China
03/26/2025 | Indium CorporationAs a global materials supplier and trusted partner in electric vehicle (EV) and e-Mobility manufacturing, Indium Corporation® is proud to showcase its high-reliability alloys and soldering solutions at Productronica China, March 26-28, in Shanghai, China.
SolderKing Enhances Brainboxes' Electronics Manufacturing with Expert Support and Advanced Materials
03/26/2025 | SolderKingIn modern electronics manufacturing, success relies on more than high-quality soldering materials. Technical knowledge and process expertise are just as crucial for achieving consistent results. SolderKing, a leading UK manufacturer, provides both, combining advanced consumables with specialist support to help manufacturers optimise their soldering processes.
AIM to Highlight Type 5 Solder and Other Leading Products at SMTA Monterrey Expo & Tech Forum
03/20/2025 | AIM SolderAIM Solder, a leading global manufacturer of solder assembly materials for the electronics industry, is pleased to announce its participation in the upcoming SMTA Monterrey Expo & Tech Forum taking place on April 10 at Cintermex in Monterrey, Nuevo Leon, Mexico.
Hentec Industries/RPS Automation to Showcase Valence 2508 at IPC Expo 2025
03/17/2025 | Hentec Industries/RPS AutomationThe Valence 2508 Selective Soldering System is engineered for high-mix, high-volume, advanced PCB production. It supports boards ranging from 25 x 25 mm to 559 x 559 mm (1 x 1 in. to 22 x 22 in.), with a maximum processing area of 508 x 508 mm (20 x 20 in.).