-
- News
- Books
Featured Books
- smt007 Magazine
Latest Issues
Current IssueWhat's Your Sweet Spot?
Are you in a niche that’s growing or shrinking? Is it time to reassess and refocus? We spotlight companies thriving by redefining or reinforcing their niche. What are their insights?
Moving Forward With Confidence
In this issue, we focus on sales and quoting, workforce training, new IPC leadership in the U.S. and Canada, the effects of tariffs, CFX standards, and much more—all designed to provide perspective as you move through the cloud bank of today's shifting economic market.
Intelligent Test and Inspection
Are you ready to explore the cutting-edge advancements shaping the electronics manufacturing industry? The May 2025 issue of SMT007 Magazine is packed with insights, innovations, and expert perspectives that you won’t want to miss.
- Articles
- Columns
- Links
- Media kit
||| MENU - smt007 Magazine
Indium on Voiding and Auto Electronics Test Standard
October 9, 2018 | Stephen Las Marias, I-Connect007Estimated reading time: 8 minutes
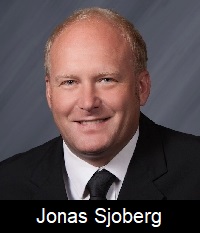
Based in Kuala Lumpur, Malaysia, Indium Corporation Technical Manager Jonas Sjoberg handles technical support for Asia. In this interview, Sjoberg discusses voiding and other key challenges in soldering, as well as an automotive electronics testing standard based out of South Korea that is seeing increased utilization all over Asia.
Stephen Las Marias: Jonas, tell us a little more about Indium Corporation and your role in the company.
Jonas Sjoberg: Indium Corporation is one of the major suppliers in the electronic market. We manufacture a lot of different products, including solder pastes, fluxes, preforms, and new solder materials for both the traditional PCBA assembly and semiconductor markets. As a company, we have grown a lot over the last 84 years and now have over 800 employees globally.
I handle technical support for Asia, which is a very big market for Indium Corporation. I think one of the key responsibilities for a material supplier is not only to sell material, but also to work closely with the customers to really understand their requirements. If we don't understand their requirements or the markets they are in, we can’t recommend the right product or even develop new products to meet their needs.
To ensure that we can provide technical support for our products, we need to understand some elements of design, reliability requirements, and material costs. We also need to understand total cost, because that's what's important to our customers. If we understand these things, we can create a win-win solution for our customers, which is a must for sustaining these types of business-to-business relationships. I think this perspective is what drives our technical support and sales teams.
Las Marias: In your conversations with customers, what are some of the critical challenges they continue to face?
Sjoberg: There are a few different areas. Of course, voiding is a big concern. Not everyone is looking at it, but a lot of customers (especially in the automotive industry) see voiding as a major concern.
There is also what we call MS-184, which is the standard that’s being used in South Korea by Kia and Hyundai. [NOTE: MS-184 is a testing specification developed by Hyundai and Kia that tests the properties of a material and how it performs in specific reliability tests, including SIR, thermocycling, and tin whisker testing. It is being required by many other automotive manufacturers as well.]That also spills over to their EMS in China. We have a lot of customers that may be running one line for a certain automotive company and a separate line for another, but they require this standard for all their customers.
Another challenge our customers face is something we call “electrochemical migration” (ECM), which is electrical failure issues in the BTC components or QFN components. That's something that a lot of customers are encountering, and the solution goes back to the flux residues. From a reliability standpoint, I would say those are the main challenges our customers face.
A less discussed but important issue for our customers is printing. We're seeing a trend, especially in the mobile consumer space, of people moving to Type 5 and possibly Type 6 powders. In fact, we are supplying a lot of Type 6 powders in semiconductors today. This trend of moving to finer powder sizes is gaining momentum, but it also creates its own challenges. You see, the finer the powder, the bigger the surface area you create, which results in more oxide. A lot of productions with finer powders, like Type 5 and Type 6 powders, need to use nitrogen. Some companies in China, especially in Southeast Asia, don’t use nitrogen in their production; that’s a big step for them to incorporate into their process. Also, maintaining production when you are running with nitrogen, especially with a reflow oven, is a bit more critical. If you're running with air reflow and your gaskets on the reflow oven are not perfect, it doesn’t matter so much; however, if you're running with nitrogen, the machine will start leaking, and you will have to use a lot of nitrogen to keep the level of oxygen down.
Thermal management is also an issue. That's why a lot of people are talking about voiding, especially on the thermal tests and QFNs. If you look back maybe five years, many companies said that 50% voiding was acceptable for a QFN. Now, a lot of customers are asking for lower than 10% voiding. That's where it becomes challenging, especially with solder paste. You might have to do a vacuum reflow, which some of our automotive customers are already doing. You might be forced into using preforms instead of solder paste. So yes, thermal management is a big concern in the market.
Las Marias: Speaking of nitrogen in reflow, is that a new technology that they're using now?
Sjoberg: Nitrogen has been used for in reflow for many, many years; however, with consumer electronics, you have to be very cost sensitive and nitrogen is an extra cost. Many companies are now forced to use nitrogen when transitioning to Type 5 and Type 6 powders. A lot of infrastructure customers have been using it. The boards are very expensive. With consumer electronics, people try and stay away from it, but we can see a clear shift where customers have started using nitrogen because of the finer powder. Your process window when you run with nitrogen is bigger. When you move into Type 5 and Type 6 powders, in many cases, you have to run nitrogen.
Las Marias: How do you help your customers on this front?
Sjoberg: Our first step is to listen to what they have to say and not make assumptions regarding what they need. Once we understand the requirements, we can give them the right product recommendation. If we know the products, let's say with voiding, we would recommend Indium8.9HF or Indium10.1HF. If the customer needs a fast printing application, which is quite common in some lower-end electronics, we might recommend a different material. It’s important to really hear and understand the requirements from the customer and not just assume that we know what they need.
Page 1 of 2
Suggested Items
Hands-On Demos Now Available for Apollo Seiko’s EF and AF Selective Soldering Lines
06/30/2025 | Apollo SeikoApollo Seiko, a leading innovator in soldering technology, is excited to spotlight its expanded lineup of EF and AF Series Selective Soldering Systems, now available for live demonstrations in its newly dedicated demo room.
SolderKing’s Successful Approach to Modern Soldering Needs
06/18/2025 | Nolan Johnson, I-Connect007Chris Ward, co-founder of the family-owned SolderKing, discusses his company's rapid growth and recent recognition with the King’s Award for Enterprise. Chris shares how SolderKing has achieved these award-winning levels of service in such a short timeframe. Their secret? Being flexible in a changing market, technical prowess, and strong customer support.
E-tronix Announces Upcoming Webinar with ELMOTEC: Optimizing Soldering Quality and Efficiency with Robotic Automation
05/30/2025 | E-tronixE-tronix, a Stromberg Company, is excited to host an informative webinar presented by Raphael Luchs, CEO of ELMOTEC, titled "Optimize Soldering Quality and Efficiency with Robotic Automation," taking place on Wednesday, June 4, 2025 at 12:00 PM CDT.
SMTA Releases Final Batch of Training Resources Donated by Bob Willis
05/29/2025 | SMTAThe Surface Mount Technology Association (SMTA) announces the release of several more webinars, poster sets, and photo libraries to conclude a generous donation from renowned industry expert Bob Willis.
Altus Supports Phoenix Systems in Advancing THT Assembly with Robotic Soldering
05/27/2025 | Altus GroupAltus Group, a leading distributor of capital equipment in the UK and Ireland, has successfully supported Phoenix Systems UK Ltd in its investment in robotic soldering technology to further enhance its through-hole technology (THT) assembly processes.