-
- News
- Books
Featured Books
- smt007 Magazine
Latest Issues
Current IssueWhat's Your Sweet Spot?
Are you in a niche that’s growing or shrinking? Is it time to reassess and refocus? We spotlight companies thriving by redefining or reinforcing their niche. What are their insights?
Moving Forward With Confidence
In this issue, we focus on sales and quoting, workforce training, new IPC leadership in the U.S. and Canada, the effects of tariffs, CFX standards, and much more—all designed to provide perspective as you move through the cloud bank of today's shifting economic market.
Intelligent Test and Inspection
Are you ready to explore the cutting-edge advancements shaping the electronics manufacturing industry? The May 2025 issue of SMT007 Magazine is packed with insights, innovations, and expert perspectives that you won’t want to miss.
- Articles
- Columns
- Links
- Media kit
||| MENU - smt007 Magazine
AWS Electronics Achieves Successful Transition to Latest Medical Standard ISO 13485:2016
January 11, 2019 | AWS ElectronicsEstimated reading time: 1 minute
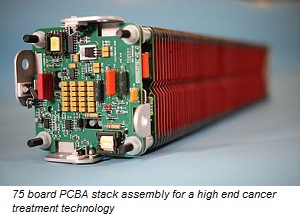
AWS Electronics has announced successful transition to the latest revision of globally recognised quality standard, ISO 13485:2016, at its Newcastle-under-Lyme manufacturing facility.
An internationally agreed standard, ISO 13485:2016 sets out the requirements for a quality management system specific to the medical devices industry. The recently revised standard places greater emphasis on risk management and risk-based decision making, in addition to changes related to the increased regulatory requirements for organisations in the supply chain. With a growing customer base in the medical sector, achievement of the standard demonstrates AWS’ ongoing commitment to ensure the highest levels of quality are met in the development and manufacture of medical devices.
Paul Deehan, CEO AWS Electronics Group, comments: “We strive to ensure our accreditations are up to the latest revision standards—not only to improve our internal processes and procedures, but also to ensure that we deliver on our strategy and commitment to customers. We are delighted to have updated our medical certification to ISO 13485:2016, with a number of our customers based in the sectors of medical and scientific instrumentation. This approval aligns with the many others we hold for the various sectors in which we work.”
AWS are pleased to support customers in a large number of industries, with accreditations held in defense and aerospace (NADCAP & AS 9100D); automotive (IATF 16949); environmental (ISO 14001) and more. AWS also work in accordance with numerous other standards such as ATEX Intrinsically Safe, ensuring that clients’ specific process and procedural requirements are met at all times.
Suggested Items
I-Connect007 Editor’s Choice: Five Must-Reads for the Week
06/27/2025 | Nolan Johnson, I-Connect007While news outside our industry keeps our attention occupied, the big news inside the industry is the rechristening of IPC as the Global Electronics Association. My must-reads begins with Marcy LaRont’s exclusive and informative interview with Dr. John Mitchell, president and CEO of the Global Electronics Association. For designers, have we finally reached the point in time where autorouters will fulfill their potential?
Knocking Down the Bone Pile: Tin Whisker Mitigation in Aerospace Applications, Part 3
06/25/2025 | Nash Bell -- Column: Knocking Down the Bone PileTin whiskers are slender, hair-like metallic growths that can develop on the surface of tin-plated electronic components. Typically measuring a few micrometers in diameter and growing several millimeters in length, they form through an electrochemical process influenced by environmental factors such as temperature variations, mechanical or compressive stress, and the aging of solder alloys.
RTX, the Singapore Economic Development Board Sign MOU Outlining 10-year Growth Roadmap
06/20/2025 | RTXRTX and the Singapore Economic Development Board (EDB) have signed a Memorandum of Understanding (MoU) which outlines a 10-year roadmap to further long-term strategic collaboration in Singapore.
Indra Signs Agreement with AXISCADES to Boost Production of Cutting-Edge Systems in India
06/18/2025 | PRNewswireParis Air Show -- Indra and the Indian technology company AXISCADES have signed an agreement to collaborate on the production of solutions for the aerospace and defense markets.
GKN Aerospace Delivers First High Voltage EWIS System for Clean Aviation’s SWITCH Project
06/16/2025 | GKN AerospaceGKN Aerospace has completed and delivered the first high voltage Electrical Wiring Interconnection System (EWIS) for the Clean Aviation SWITCH project.