-
- News
- Books
Featured Books
- smt007 Magazine
Latest Issues
Current IssueWhat's Your Sweet Spot?
Are you in a niche that’s growing or shrinking? Is it time to reassess and refocus? We spotlight companies thriving by redefining or reinforcing their niche. What are their insights?
Moving Forward With Confidence
In this issue, we focus on sales and quoting, workforce training, new IPC leadership in the U.S. and Canada, the effects of tariffs, CFX standards, and much more—all designed to provide perspective as you move through the cloud bank of today's shifting economic market.
Intelligent Test and Inspection
Are you ready to explore the cutting-edge advancements shaping the electronics manufacturing industry? The May 2025 issue of SMT007 Magazine is packed with insights, innovations, and expert perspectives that you won’t want to miss.
- Articles
- Columns
- Links
- Media kit
||| MENU - smt007 Magazine
Four Hidden Materials Handling Costs Every OEM Should Know
March 22, 2019 | Neil Sharp, JJS ManufacturingEstimated reading time: 4 minutes
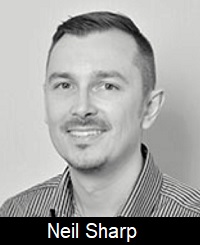
Many of the expenses within your electronics manufacturing business are highly visible and undergo regular scrutiny. But there can also be much to be gained by keeping track of those less obvious material costs that may not be formally accounted for in your monthly reporting. Taking the time to identify and review any hidden costs and assess the impact that they may be having on your bottom line could present a golden opportunity to create visible and measurable savings.
In this article, I highlight four hidden material handling costs OEMs should consider in more detail to make small but significant improvements in efficiency and profitability.
1. Procurement Costs
Your purchasing department is tasked with liaising with multiple vendors and managing all of the relational nuances of those vendor agreements. On any given day, they’re likely to source new suppliers, negotiate purchase contracts, work through daily replenishment reports, respond to urgent shortage fulfilments, or manage supplier queries. But while many of these tasks are often expected and considered to be core parts of the process, they also take time.
Some questions you may want to consider include the following. How much are these urgent shortage fulfilments really going to cost? Are there any trends, and if so, what are the causes for them? Even if the unit cost of the material is only a few pence, such as a surface-mount resistor or capacitor, what could this mean if the material is needed on the production line right then? How much is the production line costing you on an hourly basis? What other jobs is this downtime impacting? Do you need a premium to deliver the parts on the same day, and will you have to buy excess stock of the part?
Every business will have its own strategies for dealing with each scenario, but it’s worth bearing in mind that what might be on the face of it simply a penny part could be costing you a lot more in real terms.
2. Receipt Costs
The physical process of inspecting and booking materials into your system is a measurable activity. But even if you’re already monitoring supplier delivery and quality performance in some way, are you also taking into account the hidden costs of receipting your materials?
There could be value in taking a look at a few of the metrics that may not be featured in your monthly reports. Even the smallest details can make a substantial difference. Consider the number of times that the goods inward door is opened and closed to greet couriers, and how many minutes are spent accessing specialist equipment to unload goods. Further, how much time and human resources are required to implement health and safety procedures as well as the unpacking, sorting, and recycling of supplier packaging?
While many of these processes may seem obvious, it’s likely that a number of them are taking place on an hourly basis with your deliveries. Once you factor in how many deliveries you’re getting every day, these costs can soon add up. How are you recovering these costs?
3. Warehousing Costs
Physical stock accuracy is one of the more scrutinized monthly material costs. But what about the effects of some of the less desirable stock control issues, such as stock discrepancies, write-offs, damages, minimum order quantities, or obsolescence? It’s important that these less obvious losses are measured and appropriately apportioned within your business.
The physical area that you have available and how you make use of it can be another major contributor to your overall costs, and can represent a significant visible expense on your profit and loss (P&L) statement. What would you do with all of that floor space if you didn’t have to hold so much stock? Could it be used for manufacturing, or would it give you some much-needed office space?
Where your raw materials or finished goods are located within your warehouse and how easily accessible they are by your pickers could also be costing you in terms of the time taken to access them. Using your space efficiently can help your staff to complete their tasks more quickly, increase your production levels, and remove the need to expand into larger premises.
4. Pre-production Costs
One of your manufacturing team’s top priorities is to ensure that all of your labor and capital equipment are being utilized as efficiently as possible. And this can often mean a request for some element of material presentation before printed circuit board assembly (PCBA)—whether that relates to device preparation (such as cropping or pre-forming), moisture storage, handling or packaging requirements, pre-programming, or test. It's important that these additional activities have either already been captured within your overall costing model, or that they’re going to be reflected elsewhere.
Conclusion
So, there you have it: four small but surprisingly significant hidden material handling costs that, if addressed, could have a positive impact on your company’s bottom line. In an increasingly competitive manufacturing environment where every penny counts, staying mindful of even a few of these hidden costs could offer some substantial benefits for your PCBA productivity and profitability.
Neil Sharp is the director of marketing for JJS Manufacturing.
Suggested Items
The Big Picture: Our Big ‘Why’ in the Age of AI
06/25/2025 | Mehul Davé -- Column: The Big PictureWith advanced technology, Tesla, Google, Microsoft, and OpenAI can quickly transform life as we know it. Several notable artificial intelligence (AI) studies, including the 2024 McKinsey Global Survey on AI, have offered insights into AI’s adoption, impact, and trajectory. The McKinsey study revealed that AI adoption continues to grow, with 50% of respondents reporting using AI in at least one business area.
Meet Thiago Guimaraes, IPC's New Director of Industry Intelligence
05/05/2025 | Chris Mitchell, IPC VP, Global Government RelationsThe fast pace of innovation in the electronics manufacturing industry means business owners must continuously adapt their processes and capabilities to meet changing customer demands and market trends. To that end, IPC has hired Thiago Guimaraes as the new director of Industry Intelligence. In this interview, Thiago shares key goals and objectives that could revolutionize the industry as he helps stakeholders navigate industry trends and challenges.
Stocks Tumble as Nvidia Warns of Major Hit From U.S.-China Export Curbs
04/17/2025 | I-Connect007 Editorial TeamU.S. stocks slid sharply Wednesday after Nvidia warned that new U.S. export restrictions on chips to China could slash billions from its revenue, deepening investor anxiety over the broader economic fallout of President Donald Trump’s ongoing trade war.
Samsung and Google Cloud Expand Partnership
04/09/2025 | PRNewswireSamsung Electronics Co., Ltd and Google Cloud today announced an expanded partnership to bring Google Cloud's generative AI technology to Ballie, a new home AI companion robot from Samsung.
Insulectro Technology Village to Feature 35 Powerchats at IPC APEX EXPO 2025
03/11/2025 | InsulectroInsulectro, the largest distributor of materials for use in the manufacture of PCBs and printed electronics, will present its popular and successful 13.5-minute PowerChats™ during this year’s IPC APEX EXPO at the Anaheim Convention Center, March 18-20, 2025.