-
-
News
News Highlights
- Books
Featured Books
- smt007 Magazine
Latest Issues
Current IssueWhat's Your Sweet Spot?
Are you in a niche that’s growing or shrinking? Is it time to reassess and refocus? We spotlight companies thriving by redefining or reinforcing their niche. What are their insights?
Moving Forward With Confidence
In this issue, we focus on sales and quoting, workforce training, new IPC leadership in the U.S. and Canada, the effects of tariffs, CFX standards, and much more—all designed to provide perspective as you move through the cloud bank of today's shifting economic market.
Intelligent Test and Inspection
Are you ready to explore the cutting-edge advancements shaping the electronics manufacturing industry? The May 2025 issue of SMT007 Magazine is packed with insights, innovations, and expert perspectives that you won’t want to miss.
- Articles
- Columns
- Links
- Media kit
||| MENU - smt007 Magazine
Which IPC-A-610 Class is Best for Your PCBA?
April 8, 2019 | Neil Sharp, JJS ManufacturingEstimated reading time: 3 minutes
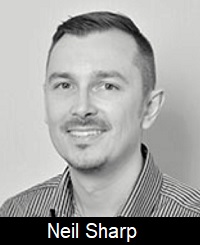
When you think about what makes a good electronics assembly, what are the most common expectations that come to mind? If the assembly works as intended, then surely that indicates a certain level of acceptability, right? But what about the product's longer-term reliability? And what if you'd also like it to look good too?
Printed circuit board assembly (PCBA) is a surprisingly complex thing. There’s the PCB itself with all of its materials, finishes, and various components, and the solder that holds everything together. Within that, there’s also a fair amount of scope for things to be good, bad, or somewhere in between.
For many electronics manufacturing services (EMS) providers, IPC-A-610: Acceptability of Electronic Assemblies is the agreed standard that we use to define what's acceptable and what's not in the world of PCBA production. The standard is comprised of three Classes: 1, 2, and 3. As an original equipment manufacturer (OEM), it’s important that you're clear on the basic principles that separate those classes so that you have a clear and realistic expectation of what the results are going to be.
Class 1
The lowest IPC-A-610 class, Class 1, is the most lenient when it comes to making allowances for potential defects. When we think of the functionality of the electronics assembly within a simple toy, for example, the PCBA is likely to be hidden well away inside the body of the item, so the quality of the solder joints or component positions may not be such a high priority. The product is also likely to be manufactured to very tight margins (read "as cheaply as possible"). So, as long as the item still functions as expected and its operational life sits within an acceptable timeframe, then that will probably be sufficient.
Class 2
Class 2 is typically the most requested for non-critical electronic assemblies where longer-term reliability is desirable, but perhaps not essential. Class 2 still allows for a certain degree of imperfection. Surface-mount components that have been placed slightly off pad, for instance, are usually still fine electrically and mechanically even though they may look wrong aesthetically.
Class 3
The highest standard of IPC-A-610 is Class 3, which means an electronic assembly must be built per all of the IPC criteria. This includes laminate selection, plating thickness, material qualifications, manufacturing processes, and inspection. Typically, Class 3 is aimed at more critical PCB assemblies.
However, achieving that standard may also come at a premium. It might be necessary to slow down the surface-mount machines to ensure the desired placement accuracy, which will mean a longer build time and additional cost. It may also be necessary to make allowance for higher degrees of scrap in cases where materials can’t be reworked or to allow time for extra inspection or additional cleaning.
Working With Your EMS partner
Many would argue that a reliable EMS provider will always aim to manufacture the products they build to the Class 3 standard, regardless. Any EMS provider that is genuinely serious about compliance is also undoubtedly going to have well-established internal training programs to promote awareness within their manufacturing facility. Also, this compliance is likely to extend not just to the inspection of the end products but also to monitoring every process of the build. The best way to achieve this and maintain the standards required will be for them to appoint in-house IPC trainers who will be externally re-certified.
In the majority of cases, the IPC-A-610 standard will suffice, but there may be situations where an OEM prefers to produce their own criteria to either enhance or replace the existing standard. If you do choose to create your own set of guidelines, then it will be important to ensure that your EMS partner is crystal clear about your expectations from the outset. Thus, you should reference your specific criteria on every request for quotation (RFQ) or purchase order that you submit.
Neil Sharp is the director of marketing for JJS Manufacturing.
Suggested Items
Silicon Mountain Contract Services Enhances SMT Capabilities with New HELLER Reflow Oven
07/17/2025 | Silicon Mountain Contract ServicesSilicon Mountain Contract Services, a leading provider of custom electronics manufacturing solutions, is proud to announce a significant upgrade to its SMT production capability with the addition of a HELLER 2043 MK5 10‑zone reflow oven to its Nampa facility.
Knocking Down the Bone Pile: Addressing End-of-life Component Solderability Issues, Part 4
07/16/2025 | Nash Bell -- Column: Knocking Down the Bone PileIn 1983, the Department of Defense identified that over 40% of military electronic system failures in the field were electrical, with approximately 50% attributed to poor solder connections. Investigations revealed that plated finishes, typically nickel or tin, were porous and non-intermetallic.
SHENMAO Strengthens Semiconductor Capabilities with Acquisition of PMTC
07/10/2025 | SHENMAOSHENMAO America, Inc. has announced the acquisition of Profound Material Technology Co., Ltd. (PMTC), a premier Taiwan-based manufacturer of high-performance solder balls for semiconductor packaging.
KYZEN to Highlight Understencil and PCB Cleaners at SMTA Querétaro Expo and Tech Forum
07/09/2025 | KYZEN'KYZEN, the global leader in innovative environmentally responsible cleaning chemistries, will exhibit at the SMTA Querétaro Expo & Tech Forum, scheduled to take place Thursday, July 24, at Centro de Congresos y Teatro Metropolitano de Querétaro.
Driving Innovation: Direct Imaging vs. Conventional Exposure
07/01/2025 | Simon Khesin -- Column: Driving InnovationMy first camera used Kodak film. I even experimented with developing photos in the bathroom, though I usually dropped the film off at a Kodak center and received the prints two weeks later, only to discover that some images were out of focus or poorly framed. Today, every smartphone contains a high-quality camera capable of producing stunning images instantly.