-
-
News
News Highlights
- Books
Featured Books
- smt007 Magazine
Latest Issues
Current IssueWhat's Your Sweet Spot?
Are you in a niche that’s growing or shrinking? Is it time to reassess and refocus? We spotlight companies thriving by redefining or reinforcing their niche. What are their insights?
Moving Forward With Confidence
In this issue, we focus on sales and quoting, workforce training, new IPC leadership in the U.S. and Canada, the effects of tariffs, CFX standards, and much more—all designed to provide perspective as you move through the cloud bank of today's shifting economic market.
Intelligent Test and Inspection
Are you ready to explore the cutting-edge advancements shaping the electronics manufacturing industry? The May 2025 issue of SMT007 Magazine is packed with insights, innovations, and expert perspectives that you won’t want to miss.
- Articles
- Columns
- Links
- Media kit
||| MENU - smt007 Magazine
Estimated reading time: 2 minutes
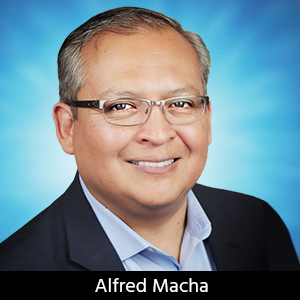
Process Validation Can Lead to Higher Performance Levels
Before we evaluate an effective approach to process validation, it is important to understand the quality system requirements of validation. In the ISO 9001:2015 standard—Clause 8.5.1—on control of production and service provision, there is a requirement for you to have controlled conditions for “validation and periodic revalidation of the ability to achieve planned results of the processes for production and service provision where the resulting output cannot be verified by subsequent monitoring or measurement.” In regulated industries, such as aerospace and medical devices, specific process validation requirements are called out in AS9100D—aerospace standard—Clause 8.5.1.2 “Validation and Control of Special Processes,” and ISO 13485:2016—medical devices, quality management systems—Clause 7.5.6 “Validation of Processes for Production and Service Provision.”
The FDA made process validation a regulatory requirement in CFR 820.75(a), process validation with supplemental guidance for industry—Process Validation: General Principles and Practices, Current Good Manufacturing Practices (CGMPs). These standards and regulations provide general guidance on the requirements but do not specify how process validation should be implemented. Each manufacturer is required to develop its own methodology best suited to its manufacturing environment. This is where manufacturers have the opportunity to implement a sustainable and effective process validation program that not only meets compliance to the standards but provides value to the manufacturer in ensuring that a process yields consistent and reliable product quality.
Continue reading this column to learn how to implement an effective process validation program in the May 2019 issue of SMT007 Magazine.
More Columns from Operational Excellence
Operational Excellence: Strengthen Your Design Transfer Process With Agile NPIOperational Excellence: Redefine Recruiting to Attract and Hire the Right Talent
Operational Excellence: Process Effectiveness Qualification
Operational Excellence: Working Remotely–Redesign Your Information Systems
Operational Excellence: Sharpening Your Organization’s Competencies
Operational Excellence: Hiring and Retaining Top Employees
Operational Excellence: Update Your Business Contingency Plan
Operational Excellence: The Gemba Transformation of Manufacturing With AI