-
- News
- Books
Featured Books
- smt007 Magazine
Latest Issues
Current IssueWhat's Your Sweet Spot?
Are you in a niche that’s growing or shrinking? Is it time to reassess and refocus? We spotlight companies thriving by redefining or reinforcing their niche. What are their insights?
Moving Forward With Confidence
In this issue, we focus on sales and quoting, workforce training, new IPC leadership in the U.S. and Canada, the effects of tariffs, CFX standards, and much more—all designed to provide perspective as you move through the cloud bank of today's shifting economic market.
Intelligent Test and Inspection
Are you ready to explore the cutting-edge advancements shaping the electronics manufacturing industry? The May 2025 issue of SMT007 Magazine is packed with insights, innovations, and expert perspectives that you won’t want to miss.
- Articles
- Columns
- Links
- Media kit
||| MENU - smt007 Magazine
Updates on Cleaning Standards and Committees
January 8, 2020 | Nolan Johnson, I-Connect007Estimated reading time: 1 minute
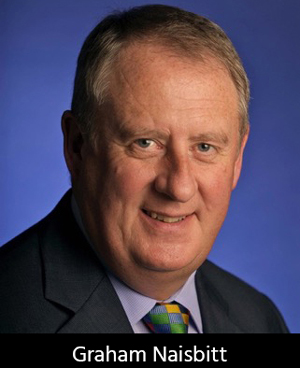
Graham Naisbitt of Gen3 discusses the changes he's seeing in cleaning, including how the WP-019 white paper has caused a closer look at electrochemical reliability. As a long-time head of committees, Graham also breaks down many of the topics he hopes are addressed at this year’s IPC APEX EXPO.
Nolan Johnson: Graham, even though so many members of this industry know who you are, I’m going to have you introduce yourself again.
Graham Naisbitt: On behalf of IPC and IEC, I am the vice-chair of the IPC 5-30 Committee, which embraces many different topics. I’m also vicechair or chair of both the SIR and the CAF test groups, and some major changes have taken place with the document that is used by the industry on how to assemble electronic circuits.
In October of 2018, J-STD-001 was changed with respect to Section 8 relating to cleaning, where we dropped the number that everyone has been relying on: 1.56 micrograms per centimeter squared of sodium chloride equivalence. The reasons for dropping that are covered comprehensively in the WP-019 white paper, which sets out the rationale for making these changes. It’s having a profound effect on the industry because with new products moving forward, we now have to look more closely at electrochemical reliability. Electrochemical reliability has become more and more relevant as the consequence of miniaturization in circuitry and circuit designs and working effectively in an increasingly hostile operating environment.
One of the challenges that the industry faces is that most process chemistries produced today have non-ionic additives that are used to aid wetting or de-wetting, as the case may be. These are not detectable by the existing or prevailing techniques. Insulation resistance testing, however, is something that has been used and embraced widely for at least the last 15–20 years, and I’ve been directly involved in most of the scientific research that originally kicked off around 1987 when we were dealing with the Montreal Protocol and the removal of CFCs, and that coincided with the introduction of no-clean processes.
To read this entire interview, which appeared in the January 2020 issue of SMT007 Magazine, click here.
Suggested Items
Meet the Author Podcast: Martyn Gaudion Unpacks the Secrets of High-Speed PCB Design
07/10/2025 | I-Connect007In this special Meet the Author episode of the On the Line with… podcast, Nolan Johnson sits down with Martyn Gaudion, signal integrity expert, managing director of Polar Instruments, and three-time author in I-Connect007’s popular The Printed Circuit Designer’s Guide to... series.
Intervala Hosts Employee Car and Motorcycle Show, Benefit Nonprofits
08/27/2024 | IntervalaIntervala hosted an employee car and motorcycle show, aptly named the Vala-Cruise and it was a roaring success! Employees had the chance to show off their prized wheels, and it was incredible to see the variety and passion on display.
KIC Honored with IPC Recognition for 25 Years of Membership and Contributions to Electronics Manufacturing Industry
06/24/2024 | KICKIC, a renowned pioneer in thermal process and temperature measurement solutions for electronics manufacturing, is proud to announce that it has been recognized by IPC for 25 years of membership and significant contributions to electronics manufacturing.
Boeing Starliner Spacecraft Completes Successful Crewed Docking with International Space Station
06/07/2024 | BoeingNASA astronauts Barry "Butch" Wilmore and Sunita "Suni" Williams successfully docked Boeing's Starliner spacecraft to the International Space Station (ISS), about 26 hours after launching from Cape Canaveral Space Force Station.
KIC’s Miles Moreau to Present Profiling Basics and Best Practices at SMTA Wisconsin Chapter PCBA Profile Workshop
01/25/2024 | KICKIC, a renowned pioneer in thermal process and temperature measurement solutions for electronics manufacturing, announces that Miles Moreau, General Manager, will be a featured speaker at the SMTA Wisconsin Chapter In-Person PCBA Profile Workshop.