-
- News
- Books
Featured Books
- smt007 Magazine
Latest Issues
Current IssueWhat's Your Sweet Spot?
Are you in a niche that’s growing or shrinking? Is it time to reassess and refocus? We spotlight companies thriving by redefining or reinforcing their niche. What are their insights?
Moving Forward With Confidence
In this issue, we focus on sales and quoting, workforce training, new IPC leadership in the U.S. and Canada, the effects of tariffs, CFX standards, and much more—all designed to provide perspective as you move through the cloud bank of today's shifting economic market.
Intelligent Test and Inspection
Are you ready to explore the cutting-edge advancements shaping the electronics manufacturing industry? The May 2025 issue of SMT007 Magazine is packed with insights, innovations, and expert perspectives that you won’t want to miss.
- Articles
- Columns
- Links
- Media kit
||| MENU - smt007 Magazine
Estimated reading time: 4 minutes
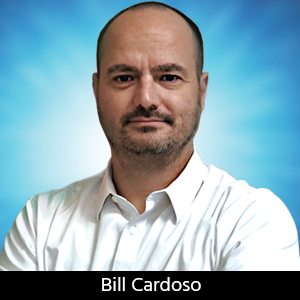
X-Rayted Files: Is Quality Really Priceless?
The short answer is no. Quality isn’t priceless. In the early 1970s, Ford needed a new car to compete with the imported sub-compacts. As the oil crises hit, Ford’s product line proudly offered “land yachts” like the Galaxie and the Fairlane (Figure 1). Compare that to the small and super economic cars offered by Honda and Toyota (Figure 2). Ford was in trouble, and they knew it. At that time, it took Ford 43 months to design and build a new car. The Pinto was designed and built in 25 months. Needless to say, they had to cut a few corners, and quality got a price tag.
As a result, Ford ended up selling cars they knew (from preliminary crash tests) carried a high risk of bursting into flame on impact and continued to do so for years. Twenty-seven people died in Pinto fires, and countless others suffered serious burns. But Ford had a sub-compact car in the market.
In the process of making anything from a car to a toaster, it comes a time where you ask yourself, “What will happen if this thing fails?” The answer is different if the toaster is to be sold at a local mart for $10 or to be installed in a Boeing 747. Similarly, the answer is different if you’re designing a car to grow market share or to barely survive a vicious competitive attack. As part of this process, at some point, you need to define the budget to make your product “good enough” for the application.
Then, you get to estimate the cost of the proposed quality assurance equipment. In a day and age when we can learn virtually anything online, manufacturers still manage to be opaque about pricing, especially when it comes to specialty equipment. After all, “Quality is priceless,” they say, but it isn’t. When I hear that, I’m always left with the impression that a sleazy salesperson will try to clean up my pockets. To make inquiries with potential vendors can mean a flood of emails and phone calls that result in more questions than answers, and who wants that?
The most common question we get is, “What does an X-ray machine cost?” It’s true that the honest answer to this question is, “It depends.” And since we’re not trying to be coy, let’s take a look at why it depends, and the things it depends on. Among the drivers of cost, first and foremost are the system’s key components: X-ray tube, detector, cabinet, and software.
X-ray tubes vary in two key characteristics, resolution, and power. For non-destructive testing, systems typically feature X-ray tubes with focal spot sizes under from several millimeters to a few micrometers (or less for electronics). And, you guessed it, the smaller the focal spot, the higher the tube cost. The power of an X-ray tube, commonly in the range of 50kV to 450kV, is the other primary factor in determining its cost. (A pet peeve to note here: Power is the product of voltage and current, but in the X-ray world, voltage defines penetration of the photon; thus, it’s common but incorrect to refer to power in kV.) Most simply, the more power, the greater the system’s ability to penetrate the sample being inspected, and as power increases, so does cost. High power and small focal spot mean lots of money.
In addition to the X-ray tube, another critical component in determining a system’s performance is its imaging detector. Like X-ray tubes, there is a wide variety, and their cost is primarily influenced by their sensitivity, pixel size, and the number of pixels. Different materials respond better or worse to X-ray photons, thus impacting their ability to convert a few (or many) X-rays to visible light. Smaller pixels help resolve small features of your sample, and a big detector can fit more of your sample in the image.
But we’re not done yet. All of the components must be housed in a shielded and safe cabinet. Radiation leakage is no joke, and safety is always job number 1. Big samples need big cabinets since your sample needs to go inside the cabinet. Really big samples (airplane wings, for example) don’t need a cabinet, but that’s a topic for a future column.
How much an X-ray system costs is not simply a product of its components but also of its functionality. Software with sophisticated analysis tools can increase both capabilities and costs. Manually operated systems, as you might imagine, are among the least expensive machines available. If inspection relies on an experienced operator in a relatively low volume environment, a manual system might be just the ticket. But for high-volume production facilities demanding short cycle times, investing in an automated inspection system will likely pay dividends.
When you consider the real cost of training and retaining experienced operators, autonomous inspection enabled by artificial intelligence may be the best choice for the most demanding applications. Autonomous is not automated. In an autonomous X-ray machine, the system not only moves samples in and out of the cabinet automatically, but it also makes pass/fail decisions on its own.
Quality has a price, and it’s your job to define it. Ford made what some consider to be the right decision at the time, while some argue it forever tarnished their brand. One thing that’s certain is they taught us all an important lesson.
Dr. Bill Cardoso is CEO of Creative Electron.
More Columns from X-Rayted Files
X-Rayted Files: Best Practices in Buying MachinesX-Rayted Files: ’23 and Me?
X-Rayted Files: Battery-Powered Advancements Keep on Ticking
X-Rayted Files: What’s Cooler Than X-ray?
X-Rayted Files: My Favorite BGA Assembly Ever, Part 3
X-Rayted Files: My Favorite BGA Assembly Ever, Part 2
X-Rayted Files: My Favorite BGA Assembly Ever
X-Rayted Files: Smart vs. Intelligent SMT Factory