-
- News
- Books
Featured Books
- smt007 Magazine
Latest Issues
Current IssueWhat's Your Sweet Spot?
Are you in a niche that’s growing or shrinking? Is it time to reassess and refocus? We spotlight companies thriving by redefining or reinforcing their niche. What are their insights?
Moving Forward With Confidence
In this issue, we focus on sales and quoting, workforce training, new IPC leadership in the U.S. and Canada, the effects of tariffs, CFX standards, and much more—all designed to provide perspective as you move through the cloud bank of today's shifting economic market.
Intelligent Test and Inspection
Are you ready to explore the cutting-edge advancements shaping the electronics manufacturing industry? The May 2025 issue of SMT007 Magazine is packed with insights, innovations, and expert perspectives that you won’t want to miss.
- Articles
- Columns
- Links
- Media kit
||| MENU - smt007 Magazine
Estimated reading time: 1 minute
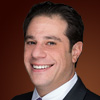
U.S. Military Tools to Prevent Counterfeit Electronics
By now, it should come as no surprise to those who are involved in electronics procurement that the industry is facing an epidemic of counterfeit parts. To stem the tide of fake electronics, both private and military supply chains are taking action through the implementation of new authentication and testing programs.
To reiterate the severity of this issue, I point to a case that made headlines because it exposed an area with the potential to impact U.S. nuclear submarines. Massachusetts resident Peter Picone was charged recently convicted of importing counterfeit semiconductors and then selling them to customers throughout the United States. Many of these parts were intended for use on U.S. nuclear submarines. This is but one of many reports on counterfeit components entering our military’s supply chain, and it comes at a very important time.
The announcement of Picone’s guilty plea comes nearly one month after the Defense Federal Acquisition Regulation Supplement (DFARS) Case 2012-D055 was finalized. This final rule will have a huge impact on prime contractors and will ultimately flow down to any supplier doing business that involve parts which end up in the hands of the government. Had these requirements been in place from 2007–2012, it is highly unlikely that Picone’s organization could have committed the fraud and deceit that it did.
This ruling provides a much needed framework for how prime defense contractors should go about mitigating their exposure to counterfeit components. The Department of Defense has also recently officially adopted the AS6081 Counterfeit Avoidance Standard for distributors. AS6081 is an internationally accredited standard developed by SAE International. It is the result of the aerospace and defense industries uniting to both provide a solution to the problem of counterfeiting and to prevent additional counterfeit components from entering the military supply chain.
Read the full column here.
Editor's Note: This column originally appeared in the September 2014 issue of SMT Magazine.
More Columns from Kramer on Counterfeits
A Summary of Counterfeit Avoidance: Development & ImpactKramer on Counterfeits: Bad Customers
Kramer on Counterfeits: Counterfeit Electronic Parts Avoidance - Profitability or Catastrophe
U.S. Military Tools to Prevent Counterfeit Electronics
Kramer on Counterfeits: DFARS Flow Downs and Trusted Suppliers
Kramer on Counterfeits: Testing Requirements for Components from Unauthorized Sources
Kramer on Components: Independent Distributor - Supply Chain's Best Friend or Worst Enemy?
Kramer on Counterfeits: Protecting Your Supply Chain from Counterfeits & Liability