-
-
News
News Highlights
- Books
Featured Books
- smt007 Magazine
Latest Issues
Current IssueWhat's Your Sweet Spot?
Are you in a niche that’s growing or shrinking? Is it time to reassess and refocus? We spotlight companies thriving by redefining or reinforcing their niche. What are their insights?
Moving Forward With Confidence
In this issue, we focus on sales and quoting, workforce training, new IPC leadership in the U.S. and Canada, the effects of tariffs, CFX standards, and much more—all designed to provide perspective as you move through the cloud bank of today's shifting economic market.
Intelligent Test and Inspection
Are you ready to explore the cutting-edge advancements shaping the electronics manufacturing industry? The May 2025 issue of SMT007 Magazine is packed with insights, innovations, and expert perspectives that you won’t want to miss.
- Articles
- Columns
- Links
- Media kit
||| MENU - smt007 Magazine
Estimated reading time: 2 minutes
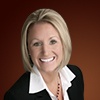
More Stencil Questions (and the Answers!)
My March The Short Scoop column, "10 Common Stencil Questions," brought in a slew of new questions from customers. Do you know the answers?
1. What are my fiducial choices and how do they differ?
Yes, stencils require fiducial markings to make sure the stencils are aligned correctly to properly print the pattern, as most people know. What they might not know is that there are actually several types of fiducials, and when you select a stencil, you must choose one of them.
The fiducial choices available today depend on the stencil manufacturer you use and/or your own requests, but truthfully, there really are only two predominate types. One is half-etched and filled, which have an etched pocket in the stencil at the fiducial location that is then filled with a black epoxy. Ultimately, these offer one of the strongest contrasts for the visual printer cameras, but they are an older technology and often, the epoxy falls out at the least opportune time.
The other predominate type is a laser tattooed fiducial, which is a relatively newer technology. These are applied by a laser (usually the same one that cuts the apertures for a laser stencil). In this technology, the laser truly burns the fiducial to the stencil. The benefits are that it lasts forever and the epoxy doesn’t fall out. Laser tattooed fiducials provide the tightest location tolerance of any fiducial and most companies are moving toward this technology. It is imperative to note, however, that the darkness of the laser fiducials have varying contrasts from one stencil to another. This is usually due to the material type, the pattern density of the stencil, laser type, and several other factors. I mention this because some printers struggle with the contrast that is less than what they might have had previously in the half-etched and filled fiducials.
2. What CAD information and files are needed to make my stencil and how will I receive my check plots?
These are very important questions so that manufacturers know what to expect and don’t waste time or effort preparing something that isn’t usable by the stencil manufacturer. Additionally, they don’t have to go back to a format that is different from what is usually done. We use IGI and Valor, which are software systems that can custom design each stencil.
Read the full column here.
Editor's Note: This column originally appeared in the July 2014 issue of SMT Magazine.
More Columns from The Short Scoop
Adapting Stencils to Manufacturing Challenges in 2015The Short Scoop: Stencil Printing in PCB Cavities
The Short Scoop: Printing Two-level PCBs in One Step with a 3D Electroform Stencil
The Short Scoop: Improving Stencil Printing Results
The Short Scoop: More Stencil Questions (and the Answers!)
The Short Scoop: Selecting a Stencil Frame
The Short Scoop: Screen Printing Solutions for Small Die & Precision
The Short Scoop: 10 Common Stencil Questions