-
-
News
News Highlights
- Books
Featured Books
- smt007 Magazine
Latest Issues
Current IssueWhat's Your Sweet Spot?
Are you in a niche that’s growing or shrinking? Is it time to reassess and refocus? We spotlight companies thriving by redefining or reinforcing their niche. What are their insights?
Moving Forward With Confidence
In this issue, we focus on sales and quoting, workforce training, new IPC leadership in the U.S. and Canada, the effects of tariffs, CFX standards, and much more—all designed to provide perspective as you move through the cloud bank of today's shifting economic market.
Intelligent Test and Inspection
Are you ready to explore the cutting-edge advancements shaping the electronics manufacturing industry? The May 2025 issue of SMT007 Magazine is packed with insights, innovations, and expert perspectives that you won’t want to miss.
- Articles
- Columns
- Links
- Media kit
||| MENU - smt007 Magazine
Rework Challenges for Smartphones and Tablets
November 19, 2014 |Estimated reading time: 1 minute
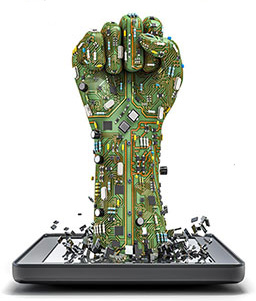
Smartphones are complex, costly devices and therefore need to be reworked correctly the first time.
To meet the ever-growing demand for performance, the complexity of mobile devices has increased immensely, with 70% more packages now found inside a mobile device than just a few years ago. For instance, a 1080P HD camera with video capabilities is now available on most high-end smartphones or tablet computers, making their production more elaborate and expensive.
The printed circuit boards for these devices are no longer considered disposable goods, and their bill of materials start from $150, with higher-end smartphones going up to $238, and tablets well over $300.
The implementation of surface mount devices is crucial for smartphone manufacturers, offering increased component density and improved performance. For example, the newer style DDR memory integrated components use less power and work at twice the speed of former versions. It is not surprising that most component manufacturers now produce these surface mount devices as small as 1 mm square.
Mobile products generally use an epoxy underfill to adhere components to the printed circuit board to meet the mechanical strength requirements of a drop test. Reworking glued components is the most difficult application in the electronics industry, and must be addressed as a process.
Rework Challenges
The removal of a glued component from a PCB assembly requires a specific order of operations. The first step is to remove the glue fillet located between the component and the circuit board. Mobile products generally have many types of components glued to the PCB in order to meet the industry standards outlined in JESD22-B111 Board Level Drop Test Method of Components for Handheld Electronic Devices and JESD22-B110 Subassembly Mechanical Shock. The epoxy is applied to the components to prevent the common failure modes of cracks in the laminate, cracks near the intermetallic, and cracks in the bulk solder. The addition of the epoxy increases the robustness of the design and enhances reliability for the user.
Read the full article here.
Editor's Note: This article originally appeared in the November 2014 issue of SMT Magazine.
Suggested Items
PCBAA Wins Summit Silver Award from the American Society of Association Executives
07/18/2025 | PCBAAPCBAA was one of 38 associations that earned Silver Awards for outstanding contributions for an entry titled: Chips Don’t Float: More Printed Circuit Boards Must be Made in America.
July 2025 PCB007 Magazine: Sales—From Pitch to PO
07/18/2025 |Though all parts of a company are essential for holistic success, it is a foundational truth that a company lives and dies by its sales. If there are no sales, the company eventually ceases to exist, or as Henry Ford says, “Nothing happens until someone sells something.” In the July issue of PCB007 Magazine, we break down the sales stack and provide a guide to up your sales game.
Silicon Mountain Contract Services Enhances SMT Capabilities with New HELLER Reflow Oven
07/17/2025 | Silicon Mountain Contract ServicesSilicon Mountain Contract Services, a leading provider of custom electronics manufacturing solutions, is proud to announce a significant upgrade to its SMT production capability with the addition of a HELLER 2043 MK5 10‑zone reflow oven to its Nampa facility.
Technica USA Introduces Frank Silva as PCBA Representative for Southern CA and Southern NV Territories
07/16/2025 | Technica USATechnica USA is pleased to announce the partnership with veteran Frank Silva as our PCBA Sales Representative, supporting both supply partners and PCBA customers across Southern California and Southern Nevada.
Beyond Design: Refining Design Constraints
07/17/2025 | Barry Olney -- Column: Beyond DesignBefore starting any project, it is crucial to develop a thorough plan that encompasses all essential requirements. This ensures that the final product not only aligns with the design concept but is also manufacturable, reliable, and meets performance expectations. High-speed PCB design requires us to not only push technological boundaries but also consider various factors related to higher frequencies, faster transition times, and increased bandwidths during the design process.