-
- News
- Books
Featured Books
- smt007 Magazine
Latest Issues
Current IssueWhat's Your Sweet Spot?
Are you in a niche that’s growing or shrinking? Is it time to reassess and refocus? We spotlight companies thriving by redefining or reinforcing their niche. What are their insights?
Moving Forward With Confidence
In this issue, we focus on sales and quoting, workforce training, new IPC leadership in the U.S. and Canada, the effects of tariffs, CFX standards, and much more—all designed to provide perspective as you move through the cloud bank of today's shifting economic market.
Intelligent Test and Inspection
Are you ready to explore the cutting-edge advancements shaping the electronics manufacturing industry? The May 2025 issue of SMT007 Magazine is packed with insights, innovations, and expert perspectives that you won’t want to miss.
- Articles
- Columns
- Links
- Media kit
||| MENU - smt007 Magazine
Estimated reading time: Less than a minute
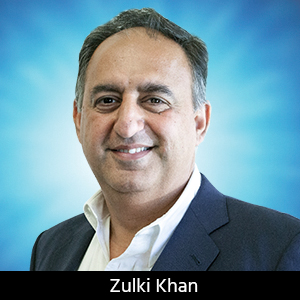
Another Look at AOI
PCB inspection is taking on greater significance as boards and packaging become increasingly smaller, with greater functionality. Automated optical inspection (AOI) and its backup associate, X-ray, team up to catch a variety of board assembly problems. But it’s AOI that’s at the forefront of this process.
AOI takes on a variety of key assignments, such as checking out the numbers labeled on passive and active devices and matching them with the database to assure they’re legitimate components, as specified in the bill of materials (BOM). Also, if alternate parts are used, the AOI machine is trained to verify them, regardless of manufacturer, as long as the device has the same footprint, value, tolerance, voltage, package type, etc.
That’s only the beginning. AOI is excellent at detecting missing or wrong components and misalignments. If a component is misaligned, say at 30° or 45°, AOI catches it. It also catches opens and bridging, and it can check for skewed parts and tombstoning. AOI can detect anything as long as it’s written on the component.
Read the full column here.
Editor's Note: This column originally appeared in the October 2013 issue of SMT Magazine.
More Columns from Zulki's PCB Nuggets
Zulki's PCB Nuggets: Cleanliness is Next to ReliabilityZulki’s PCB Nuggets: Thermal Compression Bonding for Extra Fine Pitch Flip Chips
Zulki’s PCB Nuggets: WBAN Steps Into PCB Microelectronics Assembly
Zulki’s PCB Nuggets: Photonics Comes to PCB Microelectronics Assembly
Zulki’s PCB Nuggets: Sub-Micron Die Bonding—Don’t Be Misled by Five Micron Placement Standard
Zulki’s PCB Nuggets: Meet the New Player in PCB Microelectronics Assembly—Interposers
Zulki’s PCB Nuggets: How Effective Is Your PCB Microelectronics Assembly?
Zulki’s PCB Nuggets: Five Key Benefits for Onshoring PCB Microelectronics Assembly