-
-
News
News Highlights
- Books
Featured Books
- smt007 Magazine
Latest Issues
Current IssueWhat's Your Sweet Spot?
Are you in a niche that’s growing or shrinking? Is it time to reassess and refocus? We spotlight companies thriving by redefining or reinforcing their niche. What are their insights?
Moving Forward With Confidence
In this issue, we focus on sales and quoting, workforce training, new IPC leadership in the U.S. and Canada, the effects of tariffs, CFX standards, and much more—all designed to provide perspective as you move through the cloud bank of today's shifting economic market.
Intelligent Test and Inspection
Are you ready to explore the cutting-edge advancements shaping the electronics manufacturing industry? The May 2025 issue of SMT007 Magazine is packed with insights, innovations, and expert perspectives that you won’t want to miss.
- Articles
- Columns
- Links
- Media kit
||| MENU - smt007 Magazine
Estimated reading time: 1 minute
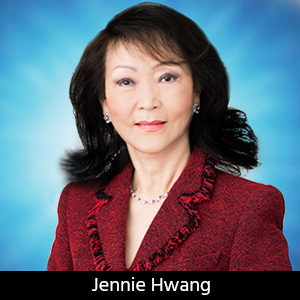
Capsulization
Since lead-free implementation, concerns about tin whiskers have intensified. For the past 12 years, studies and research by various laboratories and organizations have delivered burgeoning reports and papers, and my column has devoted an entire series to this subject. This article aims to capsulize the important areas of the subject. (Note: For expression, “whisker” is used as both noun and verb.)
The tin whisker issue and its potential mishaps have been recognized for more than six decades in electronic, electrical, and industrial applications. Some metals are prone to whiskering, or protruding from the surface of the substrate. In addition to tin, the metals that have exhibited whiskers include zinc, cadmium, silver, gold, aluminum, copper, lead, and others.
The whiskering phenomenon is distinct and unique. It is the result of a process different from other known phenomena (e.g., dendrites). And tin whisker and tin pest are separate metallurgical phenomena (SMT Magazine, May 2013). However, whiskers share commonality with dendrites in two aspects: Both are the result of a physical metallurgical process, thus following the science of physical metallurgy; and both could cause a product failure.
Uncertainty about tin whisker growth is most insidious. Stock markets do not like uncertainty, nor does the electronics industry. Our effort is to alleviate the uncertainty.
Practical Criteria
As some metals can whisker when accommodating conditions are met, the goal should be set with the differentiation between whisker-resistant and whisker-proof.
Overall, for testing or evaluation of the whisker propensity of a system, the key questions to be addressed are, is the system whisker-prone or whisker-resistant (not whisker-proof), and how does the system’s whisker resistance stand in reference to the intended benchmark?
Read the full article here.
Editor's Note: This article originally appeared in the July 2014 issue of SMT Magazine.
More Columns from SMT Perspectives and Prospects
SMT Perspectives and Prospects: Artificial Intelligence, Part 5: Brain, Mind, IntelligenceSMT Perspectives and Prospects: Artificial Intelligence, Part 4—Prompt Engineering
SMT Perspectives and Prospects: The AI Era, Part 3: LLMs, SLMs, and Foundation Models
SMT Perspectives and Prospects: A Dose of Wisdom
SMT Prospects and Perspectives: AI Opportunities, Challenges, and Possibilities, Part 1
SMT Perspectives and Prospects: Critical Materials—A Compelling Case, Part 3
SMT Prospects and Perspectives: AI—A Prelude to Opportunities, Challenges and Possibilities
SMT Perspectives and Prospects: Pearls of Wisdom