-
-
News
News Highlights
- Books
Featured Books
- smt007 Magazine
Latest Issues
Current IssueWhat's Your Sweet Spot?
Are you in a niche that’s growing or shrinking? Is it time to reassess and refocus? We spotlight companies thriving by redefining or reinforcing their niche. What are their insights?
Moving Forward With Confidence
In this issue, we focus on sales and quoting, workforce training, new IPC leadership in the U.S. and Canada, the effects of tariffs, CFX standards, and much more—all designed to provide perspective as you move through the cloud bank of today's shifting economic market.
Intelligent Test and Inspection
Are you ready to explore the cutting-edge advancements shaping the electronics manufacturing industry? The May 2025 issue of SMT007 Magazine is packed with insights, innovations, and expert perspectives that you won’t want to miss.
- Articles
- Columns
- Links
- Media kit
||| MENU - smt007 Magazine
Estimated reading time: 1 minute
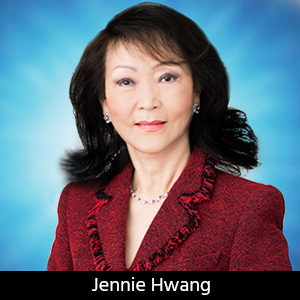
Cyber Security: From Boardroom to Factory Floor
We are living in a digital world. The digital world is characterized by big data, social media, mobile-gaming, Internet communication, cloud computing, and ultra-connectivity. As a result, we benefit immensely from various new tools and vast information flow, which were not available as recent as just 25 years ago. Regardless of which industry we serve and which capacity we hold, we are now working in the cyberspace. Cyberspace is changing the way we do business and every aspect of our lives. Living in this global network of computers also comes with new demands and challenges.
As data has become a new asset of the digital world, various incidents of cyber attacks and extortion attempting to take data as hostage have occurred. For example, when a company’s computer system is broken into, its access codes and passwords are then changed and its customers are locked out of its own system, and a ransom is demanded. This could be triggered by an insider (employee) or an outsider (hacker in any locale). Futher, a cyber thief could just simply steal the corporate secrets or confidential and proprietary information, and then demand a ransom.
Cyber attacks are and will continue to be a huge concern to U.S. corporations in the foreseeable future. It's a matter of when, not if. It is not industry-specific and every company will have to deal with this challenge. The earlier preparation is made, the better a company is positioned to fend off the attack. The most insidious nature of cyber attack is that it could happen with ease anywhere, anytime, without physical boundaries and across national borders.
Read the full column here.
Editor's Note: This column originally appeared in the July 2013 issue of SMT Magazine.
More Columns from SMT Perspectives and Prospects
SMT Perspectives and Prospects: Artificial Intelligence, Part 5: Brain, Mind, IntelligenceSMT Perspectives and Prospects: Artificial Intelligence, Part 4—Prompt Engineering
SMT Perspectives and Prospects: The AI Era, Part 3: LLMs, SLMs, and Foundation Models
SMT Perspectives and Prospects: A Dose of Wisdom
SMT Prospects and Perspectives: AI Opportunities, Challenges, and Possibilities, Part 1
SMT Perspectives and Prospects: Critical Materials—A Compelling Case, Part 3
SMT Prospects and Perspectives: AI—A Prelude to Opportunities, Challenges and Possibilities
SMT Perspectives and Prospects: Pearls of Wisdom