-
- News
- Books
Featured Books
- smt007 Magazine
Latest Issues
Current IssueWhat's Your Sweet Spot?
Are you in a niche that’s growing or shrinking? Is it time to reassess and refocus? We spotlight companies thriving by redefining or reinforcing their niche. What are their insights?
Moving Forward With Confidence
In this issue, we focus on sales and quoting, workforce training, new IPC leadership in the U.S. and Canada, the effects of tariffs, CFX standards, and much more—all designed to provide perspective as you move through the cloud bank of today's shifting economic market.
Intelligent Test and Inspection
Are you ready to explore the cutting-edge advancements shaping the electronics manufacturing industry? The May 2025 issue of SMT007 Magazine is packed with insights, innovations, and expert perspectives that you won’t want to miss.
- Articles
- Columns
- Links
- Media kit
||| MENU - smt007 Magazine
Estimated reading time: 3 minutes
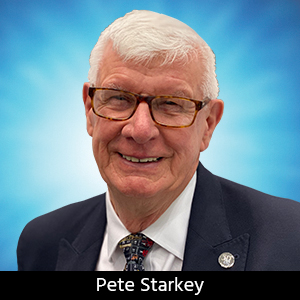
Contact Columnist Form
SMART Group Webinar: Advances in AOI technology
Systems for automated optical inspection (AOI) of electronic assemblies have undergone dramatic evolution and development in recent years, from very basic 2D image recognition via “2.5D” and “pseudo 3D” to full 3D techniques. SMART Group recently presented a webinar to clarify the fundamentals of AOI technology and discuss the strengths and weaknesses of the equipment options currently available. SMART Group Chairman Keith Bryant drew upon many years’ experience as a specialist in X-ray and AOI techniques to give a clear and comprehensive overview, with detailed explanations of attributes and applications.
“Through the eye of a needle” was the analogy that Bryant used to illustrate the trend in component size and spacing. Indeed the eye of a needle and the head of a pin looked huge compared with the 01005 chips he showed next to them. And when these chips were placed at 0.1 mm spacing, covering up to 83% of the local real estate, inspecting them for placement accuracy and solder joint quality became a real challenge. At the other end of the packaging scale were the Z-axis issues of inspecting BGAs and QFNs for coplanarity and PoPs for warpage.
Lots of good equipment was available for traditional inspection: Magnifiers, comparators, digital imaging devices, and video microscopes, but all depended ultimately on the human eye. “Is there a standard eye test for assembly operators?” Bryant asked. (Apparently there is in some aerospace specifications!). But in reality, the missed-defects rate was disturbingly high. The second consideration was the inconsistency of “judgement of what is acceptable.” Guidelines existed, for example IPC-A-610, but it was the operator’s interpretation that determined whether a defect was rejectable.
So what were the automated options? Bryant listed functional test of finished product, electrical test of partial or finished assemblies, in-circuit test of circuits and components, automated X-ray inspection for soldering and presence of components, AOI for soldering and components, and automatic solder paste inspection. He chose to focus on AOI for detail discussion.
First decision to be made was whereabouts in the process to use AOI most effectively--inspection of solder paste, component placement, solder post-reflow, or all three? Three machines on-line or a single machine off-line, able to perform all three functions on a sample basis? Whatever the decision, AOI would give more consistent results than the human eye, and, if used pre-reflow, would check for attributes such as component presence and position, component identity, orientation, polarity, and alignment. Most importantly in Bryant’s view, it would replace the “dangerous tweezer-people.” Post-reflow, the inspection task became particularly demanding. In Bryant’s words, “It’s hard to define a good solder joint--it’s even harder to define a good-enough solder joint!”
Bryant went on to explain the principles of AOI technology, the various illumination, image-capture, and image-analysis techniques available, their relative costs and capabilities, and the differences between the terms “2D,” “2.5D,” “pseudo 3D,” and “real 3D.” He discussed in detail the value of true z-axis information, particularly in solder paste inspection, citing the widely accepted view that over 60% of assembly defects originate from the solder paste printing stage, then showed several examples illustrating the limitations of 2D post-reflow inspection and some of the of subtle defects that could be revealed by high-end 3D systems.
Page 1 of 2
More Columns from The European Angle
CircuitData: A New Open Standard for PCB Fab Data ExchangeI Never Realised It Was So Complicated!
The European Angle: Institute of Circuit Technology 43rd Annual Symposium
Ventec International Group's Martin Cotton Celebrates 50 Years in PCB Design
Reporting on the Institute of Circuit Technology Spring Seminar
EuroTech: Raw Materials Supply Chain—Critical Challenges Facing the PCB Industry
EuroTech: ENIPIG—Next Generation of PCB Surface Finish
EuroTech: Institute of Circuit Technology Northern Seminar 2016, Harrogate