-
-
News
News Highlights
- Books
Featured Books
- smt007 Magazine
Latest Issues
Current IssueWhat's Your Sweet Spot?
Are you in a niche that’s growing or shrinking? Is it time to reassess and refocus? We spotlight companies thriving by redefining or reinforcing their niche. What are their insights?
Moving Forward With Confidence
In this issue, we focus on sales and quoting, workforce training, new IPC leadership in the U.S. and Canada, the effects of tariffs, CFX standards, and much more—all designed to provide perspective as you move through the cloud bank of today's shifting economic market.
Intelligent Test and Inspection
Are you ready to explore the cutting-edge advancements shaping the electronics manufacturing industry? The May 2025 issue of SMT007 Magazine is packed with insights, innovations, and expert perspectives that you won’t want to miss.
- Articles
- Columns
- Links
- Media kit
||| MENU - smt007 Magazine
Estimated reading time: 4 minutes
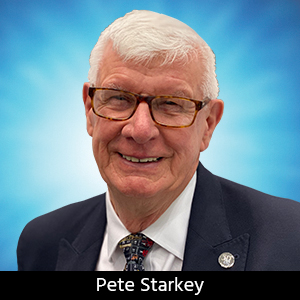
Contact Columnist Form
SMART Group Webinar: Electronics in Harsh Environments
SMART Group presented a webinar June 2, 2014 to introduce issues to be explored in depth at a seminar on July 2, 2014 at the National Physical Laboratory (NPL). Technical Director Bob Willis moderated a programme of four presentations from Technical Committee specialists Sue Knight, Richard Boyle, Chris Hunt, and Ian Fox.
Sue Knight from STI gave an introductory overview: Why are electronics needed in harsh environments? "I’ll outline the problems; the other presenters will explain how to solve them!” said Knight. She listed applications in satellite communications and base stations, oil exploration and power generation, and aerospace, automotive, and industrial instrumentation, sensors, and controls.
Against this background, she summarised the main environmental factors affecting the performance and reliability of electronic assemblies. Temperature was the biggest issue: Standard industrial components were typically rated for 85°C maximum operating temperature, and mil-aero components to 125°C. Standard high temperature laminate was only usable in applications up to about 175°C. And solder joints were unreliable when equipment operating temperature approached the melting point of standard solder alloys, particularly if accompanied by mechanical shock and vibration.
Other environmental concerns were the effects of oil, water, mud, and chemicals. How did the harsh environment considerations typically associated with military and aerospace applications relate to everyday electronics? She explained how research and development generated from those areas was often subsequently applied to benefit the functionality and reliability of commercially available equipment.
RoHS had prohibited the use of lead in solders for all but certain specific applications where no practicable or proven alternative existed. High-lead alloys had for many years been used for die-attach and had given reliable results as solders for high-temperature environments. Under current RoHS and ELV legislation, they could continue to be used in selected electronics and automotive applications, but if and when suitable alternatives to high-lead solders were found then it was likely that the legislation would be amended to prohibit all use of lead-containing materials.
Solder specialist Richard Boyle from Henkel discussed the EMEA Solder Replacement Umbrella Programme, which had the initial aims of finding suitable replacements in terms of electrical, thermal, and mechanical performance, developing products in compliance with 2014 RoHS and ELV standards, and ideally producing drop-in alternatives to existing paste, wire and preforms. The preliminary focus was on paste, potentially the simplest option. The programme was taking a multi-faceted approach, looking at different solutions for sub-segments of the market, in respect of application, cost and performance, and was considering organic-based, metallurgic-based, and combination organic-metallurgic approaches including high silver-content organic die attach, epoxy-solder paste based on tin-antimony alloys, transient liquid phase sintering, and silver sintering.
Boyle’s reference to silver sintering was expanded upon by Dr. Chris Hunt, who discussed current research at NPL on sintered silver interconnect technology with different component types and PCB finishes, and NPL’s participation in the TSB-funded Electronic Component Sintered Interconnections (ELCOSINT) project, aimed at development of novel polymeric, sintered interconnection materials to replace high-lead solders and further increase the operating temperature of electronic assemblies. These materials, based on nano-silver, would be suitable for components subjected to operating temperatures of 250° or more, and the technology was designed to be compatible with standard microelectronics manufacturing processes. Several challenges remained to be addressed and mechanical performance and reliability had not yet been fully characterised.
Page 1 of 2
More Columns from The European Angle
CircuitData: A New Open Standard for PCB Fab Data ExchangeI Never Realised It Was So Complicated!
The European Angle: Institute of Circuit Technology 43rd Annual Symposium
Ventec International Group's Martin Cotton Celebrates 50 Years in PCB Design
Reporting on the Institute of Circuit Technology Spring Seminar
EuroTech: Raw Materials Supply Chain—Critical Challenges Facing the PCB Industry
EuroTech: ENIPIG—Next Generation of PCB Surface Finish
EuroTech: Institute of Circuit Technology Northern Seminar 2016, Harrogate