-
-
News
News Highlights
- Books
Featured Books
- smt007 Magazine
Latest Issues
Current IssueWhat's Your Sweet Spot?
Are you in a niche that’s growing or shrinking? Is it time to reassess and refocus? We spotlight companies thriving by redefining or reinforcing their niche. What are their insights?
Moving Forward With Confidence
In this issue, we focus on sales and quoting, workforce training, new IPC leadership in the U.S. and Canada, the effects of tariffs, CFX standards, and much more—all designed to provide perspective as you move through the cloud bank of today's shifting economic market.
Intelligent Test and Inspection
Are you ready to explore the cutting-edge advancements shaping the electronics manufacturing industry? The May 2025 issue of SMT007 Magazine is packed with insights, innovations, and expert perspectives that you won’t want to miss.
- Articles
- Columns
- Links
- Media kit
||| MENU - smt007 Magazine
Estimated reading time: 15 minutes
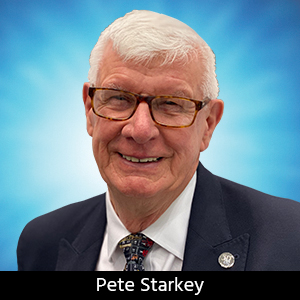
Contact Columnist Form
NPL/SMART Group Conformal Coating & Cleaning Experience
By far the best-attended seminar-workshop event at an excellent National Electronics Week (NEW) show was the NPL/SMART Group Conformal Coating and Cleaning Experience, seamlessly organised, coordinated, and managed by SMART Group Technical Director and showman extraordinaire Bob Willis.
Day One
Willis combined the exhibition and demonstration area with the seminar theatre to offer an integrated learning experience dedicated to cleaning and coating. The area was a bustle of activity for the three days of the show, several visitors having travelled from mainland Europe and Eastern Europe with attendance at this NPL/SMART event as their primary objective, and several UK assemblers I spoke to were looking to gain a clear understanding of the technology and available options before embarking upon in-house conformal coating.
An hourly series of short, punchy presentations from industry experts, interspersed with opportunities to ask questions and to see equipment and materials in real-time action, maintained a consistent momentum. In Willis' words: “It’s about getting them interested to start with!”
Getting people interested in design considerations was a task expertly undertaken by David Greenman from Humiseal. Appropriate and adequate conformal coating drawings were rarely provided, and conformal coatings were commonly specified for historical reasons rather than properly selected to suit the anticipated operating environment. It was important to check the compatibility of a coating with the components of the assembly, and particularly to determine the wettability of the solder mask to ensure good adhesion. “No clean is no option” was his comment about surface cleanliness prior to coating and he recommended SIR testing as a means of qualifying the complete assembly process.
Page 1 of 7
More Columns from The European Angle
CircuitData: A New Open Standard for PCB Fab Data ExchangeI Never Realised It Was So Complicated!
The European Angle: Institute of Circuit Technology 43rd Annual Symposium
Ventec International Group's Martin Cotton Celebrates 50 Years in PCB Design
Reporting on the Institute of Circuit Technology Spring Seminar
EuroTech: Raw Materials Supply Chain—Critical Challenges Facing the PCB Industry
EuroTech: ENIPIG—Next Generation of PCB Surface Finish
EuroTech: Institute of Circuit Technology Northern Seminar 2016, Harrogate