-
-
News
News Highlights
- Books
Featured Books
- smt007 Magazine
Latest Issues
Current IssueWhat's Your Sweet Spot?
Are you in a niche that’s growing or shrinking? Is it time to reassess and refocus? We spotlight companies thriving by redefining or reinforcing their niche. What are their insights?
Moving Forward With Confidence
In this issue, we focus on sales and quoting, workforce training, new IPC leadership in the U.S. and Canada, the effects of tariffs, CFX standards, and much more—all designed to provide perspective as you move through the cloud bank of today's shifting economic market.
Intelligent Test and Inspection
Are you ready to explore the cutting-edge advancements shaping the electronics manufacturing industry? The May 2025 issue of SMT007 Magazine is packed with insights, innovations, and expert perspectives that you won’t want to miss.
- Articles
- Columns
- Links
- Media kit
||| MENU - smt007 Magazine
Opportunities for 3D Printed Structural Electronics
January 28, 2015 | Dr. Jon Harrop, IDTechExEstimated reading time: 1 minute
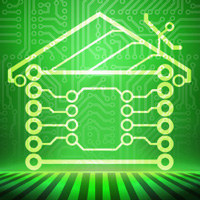
3D printing refers to the physical construction of an object from a digital description through the selective deposition of material. Today’s 3D printers have many limitations, but the boundaries are being pushed and exciting developments are continuously being made. One of the most promising recent developments in the world of 3D printing is multimaterial printing, not least because it is the key to the emergence of 3D printed electronics. Today’s commercially available multimaterial 3D printers are limited to providing a variety of mechanical characteristics such as rigidity as well as color and transparency, but the seemingly simple inclusion of UV curable conductive inks could make these machines capable of manufacturing objects that contain conductive traces.
This is naturally regarded by many as a direct alternative to traditional PCB manufacture and, in many respects, not a very good one. The logical application for 3D PCBs plays to the traditional strengths of 3D printing: rapid prototyping. However, the ability to lay down conductive traces inside a 3D object has far more potential. There is no longer any requirement to use flat designs. The added design freedom has the potential to greatly simplify circuit layout but will require a new generation of software tools. Furthermore, the natural evolution of this design freedom is the ability to embed electronics in the structure of anything. This is known as structural electronics.
Structural electronics is one of the most important technological developments of this century. It forms a key part of the dream, first formulated 30 years ago, of computing disappearing into the fabric of society. It also addresses, in a particularly elegant manner, the dream of Edison in 1880 that electricity should be made where it is needed. Structural electronics is often biomimetic—it usefully imitates nature in ways not previously feasible.
Suggested Items
TT Electronics Secures Multi-Million-Pound Defense Contract with Ultra PCS
07/18/2025 | TT ElectronicsTT Electronics, a leading provider of global manufacturing solutions and engineered technologies, announced that it has been awarded a significant new contract with long-standing customer Ultra PCS Ltd (Ultra Precision Control Systems).
Tata Electronics, Bosch Sign MoU for Strategic Collaboration in Electronics and Semiconductor Manufacturing
07/18/2025 | Tata ElectronicsTata Electronics, a leading player in the Indian electronics and semiconductor manufacturing sector, and Robert Bosch GmbH, a leading global supplier of technology and services, announced that they have signed a Memorandum of Understanding (MoU) to collaborate on several key areas within the electronics and semiconductor industries.
Microchip Enters into Partnership Agreement with Delta Electronics on Silicon Carbide Solutions
07/18/2025 | Globe NewswireThe growth of artificial intelligence (AI) and the electrification of everything are driving an ever-increasing demand for higher levels of power efficiency and reliability.
Hyliion Awarded U.S. Navy Contract to Advance Multi-Unit KARNO Power Module
07/18/2025 | BUSINESS WIREHyliion Holdings Corp., a leading provider of innovative KARNOTM Power Modules, announced it has been awarded a Phase II Small Business Innovation Research (SBIR) contract in the amount of $1.5 million from the U.S. Navy to further develop and refine its scalable multi-megawatt platform for shipboard and stationary military applications.
Libra Industries Launches In-House High Precision Underfill Capabilities
07/17/2025 | Libra IndustriesLibra Industries, a leading provider of systems integration and electronics manufacturing services (EMS), is excited to announce the addition of high-precision underfill to its in‑house manufacturing capabilities.