-
- News
- Books
Featured Books
- smt007 Magazine
Latest Issues
Current IssueWhat's Your Sweet Spot?
Are you in a niche that’s growing or shrinking? Is it time to reassess and refocus? We spotlight companies thriving by redefining or reinforcing their niche. What are their insights?
Moving Forward With Confidence
In this issue, we focus on sales and quoting, workforce training, new IPC leadership in the U.S. and Canada, the effects of tariffs, CFX standards, and much more—all designed to provide perspective as you move through the cloud bank of today's shifting economic market.
Intelligent Test and Inspection
Are you ready to explore the cutting-edge advancements shaping the electronics manufacturing industry? The May 2025 issue of SMT007 Magazine is packed with insights, innovations, and expert perspectives that you won’t want to miss.
- Articles
- Columns
- Links
- Media kit
||| MENU - smt007 Magazine
Solder Paste Printing: Quality Assurance Methodology
June 2, 2015 | Lars Bruno, Ericsson AB, and Tord Johnson, MTEK Consulting ABEstimated reading time: 1 minute
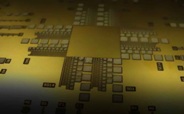
Solder paste printing is known as one of the most difficult processes to quality assure in electronic manufacturing. The challenge increases as the technology development moves toward a mix between large modules and small chip components on large and densely populated printed circuit boards. Having a process for quality assurance of the solder paste print is fast becoming a necessity. This article describes a method to ensure quality secured data from both solder paste printers and inspection machines in electronic assembly manufacturing. This information should be used as feedback in order to improve the solder paste printing process.
Introduction
This article has its roots in the need to improve capacity and quality levels at an electronics manufacturing site. Solder paste printing was identified early on as an area that needed to be secured with many of the new demands put onto the process by recent development in the manufactured products’ technology level.
A. The Solder Paste Printing Process
Solder paste printing is one of the most critical processes in electronic manufacturing. The purpose of the process is to apply the correct amount of paste, at the correct position, with the correct form and to do this every time a print is performed. Even though the process can be considered relatively simple, the quality results of the print together with the PCB provide the foundation for the rest of the surface mount process. A good print result is a prerequisite for a good soldering result, while a poor print will lead to additional process issues as the product travels through the manufacturing chain.
The printing process has the following demands and properties:
• Solder paste properties: the viscosity drops when the paste is handled
• Stencil surface friction: must be relatively high to force the paste to roll instead of skid
• Squeegee surface friction: shall be relatively low in order to allow for the paste to roll and release properly when lifted
Editor's Note: This article originally appeared in the May 2015 issue of SMT Magazine.
Suggested Items
Driving Innovation: Direct Imaging vs. Conventional Exposure
07/01/2025 | Simon Khesin -- Column: Driving InnovationMy first camera used Kodak film. I even experimented with developing photos in the bathroom, though I usually dropped the film off at a Kodak center and received the prints two weeks later, only to discover that some images were out of focus or poorly framed. Today, every smartphone contains a high-quality camera capable of producing stunning images instantly.
Hands-On Demos Now Available for Apollo Seiko’s EF and AF Selective Soldering Lines
06/30/2025 | Apollo SeikoApollo Seiko, a leading innovator in soldering technology, is excited to spotlight its expanded lineup of EF and AF Series Selective Soldering Systems, now available for live demonstrations in its newly dedicated demo room.
Indium Corporation Expert to Present on Automotive and Industrial Solder Bonding Solutions at Global Electronics Association Workshop
06/26/2025 | IndiumIndium Corporation Principal Engineer, Advanced Materials, Andy Mackie, Ph.D., MSc, will deliver a technical presentation on innovative solder bonding solutions for automotive and industrial applications at the Global Electronics A
Fresh PCB Concepts: Assembly Challenges with Micro Components and Standard Solder Mask Practices
06/26/2025 | Team NCAB -- Column: Fresh PCB ConceptsMicro components have redefined what is possible in PCB design. With package sizes like 01005 and 0201 becoming more common in high-density layouts, designers are now expected to pack more performance into smaller spaces than ever before. While these advancements support miniaturization and functionality, they introduce new assembly challenges, particularly with traditional solder mask and legend application processes.
Knocking Down the Bone Pile: Tin Whisker Mitigation in Aerospace Applications, Part 3
06/25/2025 | Nash Bell -- Column: Knocking Down the Bone PileTin whiskers are slender, hair-like metallic growths that can develop on the surface of tin-plated electronic components. Typically measuring a few micrometers in diameter and growing several millimeters in length, they form through an electrochemical process influenced by environmental factors such as temperature variations, mechanical or compressive stress, and the aging of solder alloys.