-
- News
- Books
Featured Books
- smt007 Magazine
Latest Issues
Current IssueMoving Forward With Confidence
In this issue, we focus on sales and quoting, workforce training, new IPC leadership in the U.S. and Canada, the effects of tariffs, CFX standards, and much more—all designed to provide perspective as you move through the cloud bank of today's shifting economic market.
Intelligent Test and Inspection
Are you ready to explore the cutting-edge advancements shaping the electronics manufacturing industry? The May 2025 issue of SMT007 Magazine is packed with insights, innovations, and expert perspectives that you won’t want to miss.
Do You Have X-ray Vision?
Has X-ray’s time finally come in electronics manufacturing? Join us in this issue of SMT007 Magazine, where we answer this question and others to bring more efficiency to your bottom line.
- Articles
- Columns
- Links
- Media kit
||| MENU - smt007 Magazine
In-line Solder Penetration Testing with 3D X-ray Inspection
June 10, 2015 | Andreas Turk, Goepel ElectronicEstimated reading time: 2 minutes
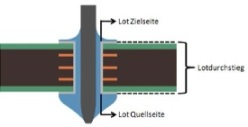
Through-hole technology (THT) is probably the oldest assembly technology in the field of PCB manufacturing. However, even in this modern age of surface-mounted technology (SMT), it still has its place. Even today, wired components are often assembled using wave soldering—in keeping with the tradition of times past. This has the disadvantage of requiring additional manufacturing equipment. It is therefore advisable to use reflow soldering for connectors and other wired components.
To this end, through-hole components were devised for automatic assembly and for high thermal loads in the furnace, which led to the birth of the term, through-hole reflow (THR). With this technology, it is now possible to process components in through-hole technology within the SMT process. But how can these solder joints be reliably tested? What technology is needed in order to be able to assess the solder penetration, for example?
Acceptance Criteria for THT/THR Solder Joints
Figure 1 is a schematic representation of a THT solder joint in cross-section. The solder wave flows from the solder source side to the solder target side (component side), due to capillary action. In so doing, it wets the connecting surface of the solder side, surrounds the pin and forms a solder meniscus on account of the protrusion of the pin on the solder side.
The acceptance criteria are defined in IPCA610 in order to distinguish between good and bad solder joints after successful soldering. Table 1 gives an overview of the criteria in excerpts.
It is now necessary to select testing technology which meets the specified acceptance criteria. Based on the example of a multi-row connector (Figure 2), the following table provides an overview of the test coverage of AOI and 3D AXI systems.
AOI systems are highly suited to assessment of the peripheral wetting of the pin and the sleeve and to evaluation of the wetted connecting surface on the solder side of a THT solder joint. The disadvantage of a traditional 2D AOI or an innovative 3D AOI system here, however, is that it is often only possible to assess the solder side because the pins on the component side are usually concealed by the component body itself. An assessment of the solder joints on the component side is therefore not possible with an AOI system. The solder penetration also remains hidden from traditional AOI technology.
A modern 3D X-ray system can provide a remedy. The 3D X-ray inspection not only makes the solder joints on the component side (i.e., below the component housing) visible, but is also able to calculate the solder penetration and the solder volume.
Editor's Note: This article originally appeared in the June 2015 issue of SMT Magazine.
Suggested Items
Hands-On Demos Now Available for Apollo Seiko’s EF and AF Selective Soldering Lines
06/30/2025 | Apollo SeikoApollo Seiko, a leading innovator in soldering technology, is excited to spotlight its expanded lineup of EF and AF Series Selective Soldering Systems, now available for live demonstrations in its newly dedicated demo room.
Indium Corporation Expert to Present on Automotive and Industrial Solder Bonding Solutions at Global Electronics Association Workshop
06/26/2025 | IndiumIndium Corporation Principal Engineer, Advanced Materials, Andy Mackie, Ph.D., MSc, will deliver a technical presentation on innovative solder bonding solutions for automotive and industrial applications at the Global Electronics A
Fresh PCB Concepts: Assembly Challenges with Micro Components and Standard Solder Mask Practices
06/26/2025 | Team NCAB -- Column: Fresh PCB ConceptsMicro components have redefined what is possible in PCB design. With package sizes like 01005 and 0201 becoming more common in high-density layouts, designers are now expected to pack more performance into smaller spaces than ever before. While these advancements support miniaturization and functionality, they introduce new assembly challenges, particularly with traditional solder mask and legend application processes.
Knocking Down the Bone Pile: Tin Whisker Mitigation in Aerospace Applications, Part 3
06/25/2025 | Nash Bell -- Column: Knocking Down the Bone PileTin whiskers are slender, hair-like metallic growths that can develop on the surface of tin-plated electronic components. Typically measuring a few micrometers in diameter and growing several millimeters in length, they form through an electrochemical process influenced by environmental factors such as temperature variations, mechanical or compressive stress, and the aging of solder alloys.
SolderKing’s Successful Approach to Modern Soldering Needs
06/18/2025 | Nolan Johnson, I-Connect007Chris Ward, co-founder of the family-owned SolderKing, discusses his company's rapid growth and recent recognition with the King’s Award for Enterprise. Chris shares how SolderKing has achieved these award-winning levels of service in such a short timeframe. Their secret? Being flexible in a changing market, technical prowess, and strong customer support.