-
- News
- Books
Featured Books
- smt007 Magazine
Latest Issues
Current IssueBox Build
One trend is to add box build and final assembly to your product offering. In this issue, we explore the opportunities and risks of adding system assembly to your service portfolio.
IPC APEX EXPO 2024 Pre-show
This month’s issue devotes its pages to a comprehensive preview of the IPC APEX EXPO 2024 event. Whether your role is technical or business, if you're new-to-the-industry or seasoned veteran, you'll find value throughout this program.
Boost Your Sales
Every part of your business can be evaluated as a process, including your sales funnel. Optimizing your selling process requires a coordinated effort between marketing and sales. In this issue, industry experts in marketing and sales offer their best advice on how to boost your sales efforts.
- Articles
- Columns
Search Console
- Links
- Events
||| MENU - smt007 Magazine
Intertronics Launches New DYMAX BlueWave QX4
August 6, 2015 | IntertronicsEstimated reading time: 1 minute
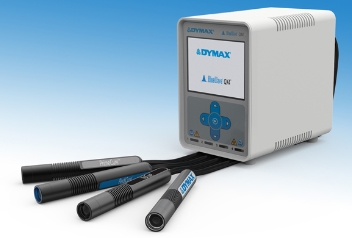
The new DYMAX BlueWave QX4 from Intertronics brings together the benefits of LED UV curing in a small and compact package that enables users to operate quickly and with more control. The QX4 multi-wand UV spot curing system puts the high intensity LEDs and lenses close to the substrate in each emitting head, with lightweight flexible connecting leads in place of light guides. This enables easy placement of up to four heads of high output power (up to 1 watt per head), which can deal with complex geometries or multiple cure points.
The system is modular with wands available in three wavelengths – 365nm, 385nm and 405nm - to suit varying compatible adhesives, coatings, sealants or other light cure materials. Lens of 3mm, 5mm and 8mm diameter can be changed on each wand to refine the cure window. The small form factor of the QX4 is useful on crowded work stations in streamlining production space. It offers a simple, easy to use interactive touch screen control panel and foot pedal operation, or PLC interface for fully automated output.
The BlueWave QX4 features instant on/off operation with no warm up required, low operating temperature, 20,000 hour light source life with no performance degradation, and low energy consumption.
For further information please see www.intertronics.co.uk/qx4 or visit their blog at www.adhere.uk.com – also see www.youtube.com/intertronicsadhere.
Suggested Items
Lockheed Martin Australia, The Department Of Defence Sign Strategic Partnership Head Contract
04/26/2024 | Lockheed MartinLockheed Martin Australia signed a landmark AUD$500 million contract with the Department of Defence to build Australia’s future Joint Air Battle Management System under project - AIR6500 Phase 1 (AIR6500-1).
Cadence, TSMC Collaborate on Wide-Ranging Innovations to Transform System and Semiconductor Design
04/25/2024 | Cadence Design SystemsCadence Design Systems, Inc. and TSMC have extended their longstanding collaboration by announcing a broad range of innovative technology advancements to accelerate design, including developments ranging from 3D-IC and advanced process nodes to design IP and photonics.
Siemens’ Breakthrough Veloce CS Transforms Emulation and Prototyping with Three Novel Products
04/24/2024 | Siemens Digital Industries SoftwareSiemens Digital Industries Software launched the Veloce™ CS hardware-assisted verification and validation system. In a first for the EDA (Electronic Design Automation) industry, Veloce CS incorporates hardware emulation, enterprise prototyping and software prototyping and is built on two highly advanced integrated circuits (ICs) – Siemens’ new, purpose-built Crystal accelerator chip for emulation and the AMD Versal™ Premium VP1902 FPGA adaptive SoC (System-on-a-chip) for enterprise and software prototyping.
Taiyo Circuit Automation Installs New DP3500 into Fuba Printed Circuits, Tunisia
04/25/2024 | Taiyo Circuit AutomationTaiyo Circuit Automation is proud to be partnered with Fuba Printed Circuits, Tunisia part of the OneTech Group of companies, a leading printed circuit board manufacturer based out of Bizerte, Tunisia, on their first installation of Taiyo Circuit Automation DP3500 coater.
Vicor Power Orders Hentec Industries/RPS Automation Pulsar Solderability Testing System
04/24/2024 | Hentec Industries/RPS AutomationHentec Industries/RPS Automation, a leading manufacturer of selective soldering, lead tinning and solderability test equipment, is pleased to announce that Vicor Power has finalized the purchase of a Pulsar solderability testing system.