-
-
News
News Highlights
- Books
Featured Books
- smt007 Magazine
Latest Issues
Current IssueWhat's Your Sweet Spot?
Are you in a niche that’s growing or shrinking? Is it time to reassess and refocus? We spotlight companies thriving by redefining or reinforcing their niche. What are their insights?
Moving Forward With Confidence
In this issue, we focus on sales and quoting, workforce training, new IPC leadership in the U.S. and Canada, the effects of tariffs, CFX standards, and much more—all designed to provide perspective as you move through the cloud bank of today's shifting economic market.
Intelligent Test and Inspection
Are you ready to explore the cutting-edge advancements shaping the electronics manufacturing industry? The May 2025 issue of SMT007 Magazine is packed with insights, innovations, and expert perspectives that you won’t want to miss.
- Articles
- Columns
- Links
- Media kit
||| MENU - smt007 Magazine
Acceptance Testing Of Low-Ag Reflow Solder Alloys (Part 2)
August 13, 2015 | K. Troxel, A. Allen, E.E. Benedetto, R. Joshi, Hewlett-Packard Co.Estimated reading time: 7 minutes
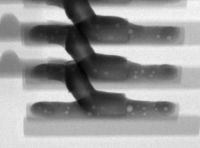
In Part 2 of this two-part article series, the authors discussed the test results for low-silver alloys using these solder paste alloy assessment protocols for BGAs and leaded components, and the impact of the alloys on printed circuit assembly process windows.
Test Results and Discussion
Manufacturing DoE Results
IMC Thickness
Measured on BGA Manufacturing DoE Test Boards (see Figure 1 in Part 1) that were reflowed 3 times with a peak reflow temperature of 250 °C and 120 seconds TAL.
Two BGA body sizes were evaluated [14 mm and 23 mm]. IMC thicknesses for alloys A and B were normally distributed with no significant difference between the large and small BGA. For alloys C and D, greater variability in the large BGA IMC thickness resulted in values significantly different than smaller BGA (as seen in Figure 1 and Table 1).
Figure 1: IMC thickness distribution by Alloy (A-D) and BGA size (large/small)
Table 1: Summary of IMC thicknesses (microns)
Copper Dissolution
This was measured on the BGA Manufacturing DoE Test Boards (see Figure 1 in Part 1) that were reflowed 3 times with a peak reflow temperature of 250°C and 120 seconds TAL.
Cu thickness measurements were made at each solder joint, in the middle of the joint and underneath the soldermask adjacent to the joint. Cu removed was the difference in copper thickness at these two locations. Cu dissolved was determined by subtracting Epsilon (thickness of Cu removed during soldermask etch in the PCB fab process) from the Cu removed values.
Figure 2: Cu dissolution distribution by alloy
Table 2: Summary of Cu dissolved (microns)
The amount of Cu dissolved after soldering was less for the low silver alloys than that for SAC305. The Cu dissolution results were normally distributed for the evaluated alloys but varied with alloy and BGA size (as seen in Figure 2 and Table 2). The Cu dissolution performance varied by BGA size, though not in a consistent fashion. While alloy B showed comparable Cu dissolved values between the 2 BGA sizes, alloy C and D both had more Cu dissolved for the larger BGA while alloy A had greater Cu dissolution values for the small BGA (this could be attributable to bare board Cu characteristics between the different vendors).
Page 1 of 3
Suggested Items
Knocking Down the Bone Pile: Addressing End-of-life Component Solderability Issues, Part 4
07/15/2025 | Nash Bell -- Column: Knocking Down the Bone PileIn 1983, the Department of Defense identified that over 40% of military electronic system failures in the field were electrical, with approximately 50% attributed to poor solder connections. Investigations revealed that plated finishes, typically nickel or tin, were porous and non-intermetallic.
SHENMAO Strengthens Semiconductor Capabilities with Acquisition of PMTC
07/10/2025 | SHENMAOSHENMAO America, Inc. has announced the acquisition of Profound Material Technology Co., Ltd. (PMTC), a premier Taiwan-based manufacturer of high-performance solder balls for semiconductor packaging.
KYZEN to Highlight Understencil and PCB Cleaners at SMTA Querétaro Expo and Tech Forum
07/09/2025 | KYZEN'KYZEN, the global leader in innovative environmentally responsible cleaning chemistries, will exhibit at the SMTA Querétaro Expo & Tech Forum, scheduled to take place Thursday, July 24, at Centro de Congresos y Teatro Metropolitano de Querétaro.
Driving Innovation: Direct Imaging vs. Conventional Exposure
07/01/2025 | Simon Khesin -- Column: Driving InnovationMy first camera used Kodak film. I even experimented with developing photos in the bathroom, though I usually dropped the film off at a Kodak center and received the prints two weeks later, only to discover that some images were out of focus or poorly framed. Today, every smartphone contains a high-quality camera capable of producing stunning images instantly.
Hands-On Demos Now Available for Apollo Seiko’s EF and AF Selective Soldering Lines
06/30/2025 | Apollo SeikoApollo Seiko, a leading innovator in soldering technology, is excited to spotlight its expanded lineup of EF and AF Series Selective Soldering Systems, now available for live demonstrations in its newly dedicated demo room.