-
- News
- Books
Featured Books
- smt007 Magazine
Latest Issues
Current IssueWhat's Your Sweet Spot?
Are you in a niche that’s growing or shrinking? Is it time to reassess and refocus? We spotlight companies thriving by redefining or reinforcing their niche. What are their insights?
Moving Forward With Confidence
In this issue, we focus on sales and quoting, workforce training, new IPC leadership in the U.S. and Canada, the effects of tariffs, CFX standards, and much more—all designed to provide perspective as you move through the cloud bank of today's shifting economic market.
Intelligent Test and Inspection
Are you ready to explore the cutting-edge advancements shaping the electronics manufacturing industry? The May 2025 issue of SMT007 Magazine is packed with insights, innovations, and expert perspectives that you won’t want to miss.
- Articles
- Columns
- Links
- Media kit
||| MENU - smt007 Magazine
Reducing Print Cycle Time
October 22, 2015 | Mitch Holtzer and Lourenco Nampo, AlphaEstimated reading time: 2 minutes
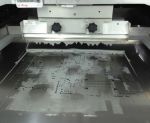
Of the several steps in the SMT process, an effective method of increasing throughput is to reduce the cycle time of the rate-controlling process step. Depending on the type of assembly and equipment set used, the process step with the longest cycle time could potentially be printing, solder paste inspection (SPI), component placement or reflow oven conveyor speed. This article will discuss two simple experiments that may lead to increased throughput and increased profitability (assuming the selling price exceeds the marginal cost of each assembly).
Print cycle time can be the bottleneck if the electronic assembly has relatively few components or if the production line used has a well equipped set of placement devices. If this is the case, there are two simple experiments that can be carried out to evaluate if a reduction in print cycle time can increase production volumes without reducing quality. Producing bad boards fast is much worse than producing good boards slowly. The first experiment is to increase the speed of the squeegee stoke. Figure 1 shows the relationship of the squeegee speed, stroke length and the time required for the solder paste to be printed.
Figure 1: Stroke time versus speed (inches per second) and distance.
If a slow squeegee speed is currently being used (<2 inches/second), there is a greater opportunity for increasing throughput. When running the experiment at increasing squeegee speeds, review the CpK recorded on your SPI equipment for a gain or reduction in process capability. Some solder pastes give better print volume reproducibility at higher speeds. This results in a win-win, higher production and improved process yields.
One important thing to look for when increasing the squeegee speed is paste left on the stencil. When a higher squeegee speed is used, it is usually necessary to increase the pressure of the blade on the stencil until the residue disappears.
The second experiment to reduce print process cycle time is to examine how often you clean the bottom side of the stencil. This is commonly referred to as wipe frequency. Cleaning the stencil removes solder paste that may be building up in the apertures. It also removes any paste that may be trapped under the stencil, waiting to be transfer printed to an undesired place on the circuit card, later to be blamed as a spatter.
Editor's Note: This article originally appeared in the October 2015 issue of SMT Magazine.
Suggested Items
SHENMAO Strengthens Semiconductor Capabilities with Acquisition of PMTC
07/10/2025 | SHENMAOSHENMAO America, Inc. has announced the acquisition of Profound Material Technology Co., Ltd. (PMTC), a premier Taiwan-based manufacturer of high-performance solder balls for semiconductor packaging.
KYZEN to Highlight Understencil and PCB Cleaners at SMTA Querétaro Expo and Tech Forum
07/09/2025 | KYZEN'KYZEN, the global leader in innovative environmentally responsible cleaning chemistries, will exhibit at the SMTA Querétaro Expo & Tech Forum, scheduled to take place Thursday, July 24, at Centro de Congresos y Teatro Metropolitano de Querétaro.
Driving Innovation: Direct Imaging vs. Conventional Exposure
07/01/2025 | Simon Khesin -- Column: Driving InnovationMy first camera used Kodak film. I even experimented with developing photos in the bathroom, though I usually dropped the film off at a Kodak center and received the prints two weeks later, only to discover that some images were out of focus or poorly framed. Today, every smartphone contains a high-quality camera capable of producing stunning images instantly.
Hands-On Demos Now Available for Apollo Seiko’s EF and AF Selective Soldering Lines
06/30/2025 | Apollo SeikoApollo Seiko, a leading innovator in soldering technology, is excited to spotlight its expanded lineup of EF and AF Series Selective Soldering Systems, now available for live demonstrations in its newly dedicated demo room.
Indium Corporation Expert to Present on Automotive and Industrial Solder Bonding Solutions at Global Electronics Association Workshop
06/26/2025 | IndiumIndium Corporation Principal Engineer, Advanced Materials, Andy Mackie, Ph.D., MSc, will deliver a technical presentation on innovative solder bonding solutions for automotive and industrial applications at the Global Electronics A