-
-
News
News Highlights
- Books
Featured Books
- smt007 Magazine
Latest Issues
Current IssueWhat's Your Sweet Spot?
Are you in a niche that’s growing or shrinking? Is it time to reassess and refocus? We spotlight companies thriving by redefining or reinforcing their niche. What are their insights?
Moving Forward With Confidence
In this issue, we focus on sales and quoting, workforce training, new IPC leadership in the U.S. and Canada, the effects of tariffs, CFX standards, and much more—all designed to provide perspective as you move through the cloud bank of today's shifting economic market.
Intelligent Test and Inspection
Are you ready to explore the cutting-edge advancements shaping the electronics manufacturing industry? The May 2025 issue of SMT007 Magazine is packed with insights, innovations, and expert perspectives that you won’t want to miss.
- Articles
- Columns
- Links
- Media kit
||| MENU - smt007 Magazine
Magnetically Aligned Novel ACA Revolutionizes 3D Chip Stacking
February 18, 2016 | Dr. S. Manian Ramkumar, Rochester Institute of TechnologyEstimated reading time: 1 minute
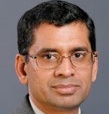
The use of anisotropic conductive adhesive (ACA) is not new within the electronics industry; however, drop-in replacements don't exist for lead-based and lead-free solder assemblies. Current ACAs require pressure and sequential assembly of components. Sunray Scientific's Novel ACA (ZTACH) is an excellent drop-in ACA replacement that will revolutionize the packaging industry and make electronic products more sustainable and green. ZTACH has been proven to enable the use of existing SMT equipment, lower the processing temperatures (75–150°C), and also eliminate the need to apply pressure, thereby eliminating the need to invest in new equipment and processes and reducing energy consumption.
ZTACH is composed of conductive, ferromagnetic particles in an epoxy matrix, which is printed or dispensed on the individual pads or the entire footprint of the components. The material is cured in a reflow oven, after all components are in place, in the presence of a magnetic field. The magnetic field aligns the conductive particles in the Z-axis direction, during curing, thereby eliminating the need for pressure. The formation of conductive columns within the adhesive matrix during cure provides a very high insulation resistance between adjacent conductors and also eliminates the need for precise printing or dispensing of adhesives onto individual fine pitch pads. Modification of the filler size and filler proportion enables control of the column density, column spacing and the required contact pad area for minimum resistance. ZTACH can be mass cured, eliminating the need for sequential component assembly. The formation of many parallel columns especially with micron and sub-micron sized particles between mating pads reduces the resistance considerably.
Editor's Note: This article originally appeared in the February 2016 issue of SMT Magazine.
Suggested Items
Silicon Mountain Contract Services Enhances SMT Capabilities with New HELLER Reflow Oven
07/17/2025 | Silicon Mountain Contract ServicesSilicon Mountain Contract Services, a leading provider of custom electronics manufacturing solutions, is proud to announce a significant upgrade to its SMT production capability with the addition of a HELLER 2043 MK5 10‑zone reflow oven to its Nampa facility.
Knocking Down the Bone Pile: Addressing End-of-life Component Solderability Issues, Part 4
07/16/2025 | Nash Bell -- Column: Knocking Down the Bone PileIn 1983, the Department of Defense identified that over 40% of military electronic system failures in the field were electrical, with approximately 50% attributed to poor solder connections. Investigations revealed that plated finishes, typically nickel or tin, were porous and non-intermetallic.
SHENMAO Strengthens Semiconductor Capabilities with Acquisition of PMTC
07/10/2025 | SHENMAOSHENMAO America, Inc. has announced the acquisition of Profound Material Technology Co., Ltd. (PMTC), a premier Taiwan-based manufacturer of high-performance solder balls for semiconductor packaging.
KYZEN to Highlight Understencil and PCB Cleaners at SMTA Querétaro Expo and Tech Forum
07/09/2025 | KYZEN'KYZEN, the global leader in innovative environmentally responsible cleaning chemistries, will exhibit at the SMTA Querétaro Expo & Tech Forum, scheduled to take place Thursday, July 24, at Centro de Congresos y Teatro Metropolitano de Querétaro.
Driving Innovation: Direct Imaging vs. Conventional Exposure
07/01/2025 | Simon Khesin -- Column: Driving InnovationMy first camera used Kodak film. I even experimented with developing photos in the bathroom, though I usually dropped the film off at a Kodak center and received the prints two weeks later, only to discover that some images were out of focus or poorly framed. Today, every smartphone contains a high-quality camera capable of producing stunning images instantly.