-
- News
- Books
Featured Books
- smt007 Magazine
Latest Issues
Current IssueMoving Forward With Confidence
In this issue, we focus on sales and quoting, workforce training, new IPC leadership in the U.S. and Canada, the effects of tariffs, CFX standards, and much more—all designed to provide perspective as you move through the cloud bank of today's shifting economic market.
Intelligent Test and Inspection
Are you ready to explore the cutting-edge advancements shaping the electronics manufacturing industry? The May 2025 issue of SMT007 Magazine is packed with insights, innovations, and expert perspectives that you won’t want to miss.
Do You Have X-ray Vision?
Has X-ray’s time finally come in electronics manufacturing? Join us in this issue of SMT007 Magazine, where we answer this question and others to bring more efficiency to your bottom line.
- Articles
- Columns
- Links
- Media kit
||| MENU - smt007 Magazine
High-reliability, Pb-free, Halogen-free Solder
November 18, 2014 | Ian Wilding and Gavin Jackson, Henkel Ltd., UKEstimated reading time: 1 minute
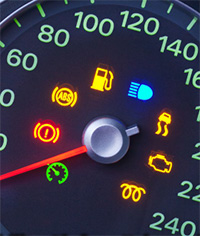
Abstract
With increasing demand for the use of Pb-free solder materials coupled with an increasing requirement for halogen-free solder paste formulations, some market sectors are experiencing several challenges using standard SnAgCu (SAC) halide-free solder materials, especially in electronic assemblies for automotive products experiencing harsh operating environments such as high operating temperatures, increased thermal cycling conditions, high levels of vibration and contact with liquids such as moisture and lubricants. For example, in automotive "under the hood" conditions, temperatures easily exceed 125°C and can cycle lower than -20°C. The reliability required to survive these harsh conditions is often greater than standard SAC solders can provide. In this paper, the performance of a specifically designed Pb-free solder alloy for increased reliability in high-temperature thermal cycling is discussed.
Reliability can also be impacted by no-clean post reflow residues adjacent to solder joints. These may potentially interact with other surface materials causing corrosion issues or lower insulation resistance. With halogen-free electronic assemblies arguably becoming more favourable than halide-free–even within some automotive manufacturers–solder paste manufacturers are now faced with the challenge of formulating halogen-free fluxes which can also demonstrate high reliability. While removing the halogen from a material is not difficult, replacing it with an activator set that can deliver a wide reflow process window whilst retaining or increasing reliability is a significant challenge. The paper also documents the challenges and breakthroughs in developing halogen-free or zero-halogen solder fluxes that are compatible with the Pb-free alloy specifically designed for higher reliability.
Introduction
Reliability testing of standard SAC-based alloys as a direct comparison to Pb-containing materials as a response to the implementation of the RoHS directive during the mid-2000s has been well documented. The results of the testing broadly concluded that little differences could be seen between SAC and SnPb alloys. Analysis of the data showed that, depending on the test vehicle configuration and the test conditions in some cases, SAC alloys gave improved reliability over SnPb alloys and in other examples the reverse result occurred. This testing focused on environmental conditions representative of the bulk of the electronics industry at that moment in time (-40°C to +125°C).
Read the full article here.
Editor's Note: This article originally appeared in the November 2014 issue of SMT Magazine.
Suggested Items
Hands-On Demos Now Available for Apollo Seiko’s EF and AF Selective Soldering Lines
06/30/2025 | Apollo SeikoApollo Seiko, a leading innovator in soldering technology, is excited to spotlight its expanded lineup of EF and AF Series Selective Soldering Systems, now available for live demonstrations in its newly dedicated demo room.
Indium Corporation Expert to Present on Automotive and Industrial Solder Bonding Solutions at Global Electronics Association Workshop
06/26/2025 | IndiumIndium Corporation Principal Engineer, Advanced Materials, Andy Mackie, Ph.D., MSc, will deliver a technical presentation on innovative solder bonding solutions for automotive and industrial applications at the Global Electronics A
Fresh PCB Concepts: Assembly Challenges with Micro Components and Standard Solder Mask Practices
06/26/2025 | Team NCAB -- Column: Fresh PCB ConceptsMicro components have redefined what is possible in PCB design. With package sizes like 01005 and 0201 becoming more common in high-density layouts, designers are now expected to pack more performance into smaller spaces than ever before. While these advancements support miniaturization and functionality, they introduce new assembly challenges, particularly with traditional solder mask and legend application processes.
Knocking Down the Bone Pile: Tin Whisker Mitigation in Aerospace Applications, Part 3
06/25/2025 | Nash Bell -- Column: Knocking Down the Bone PileTin whiskers are slender, hair-like metallic growths that can develop on the surface of tin-plated electronic components. Typically measuring a few micrometers in diameter and growing several millimeters in length, they form through an electrochemical process influenced by environmental factors such as temperature variations, mechanical or compressive stress, and the aging of solder alloys.
SolderKing’s Successful Approach to Modern Soldering Needs
06/18/2025 | Nolan Johnson, I-Connect007Chris Ward, co-founder of the family-owned SolderKing, discusses his company's rapid growth and recent recognition with the King’s Award for Enterprise. Chris shares how SolderKing has achieved these award-winning levels of service in such a short timeframe. Their secret? Being flexible in a changing market, technical prowess, and strong customer support.