-
- News
- Books
Featured Books
- smt007 Magazine
Latest Issues
Current IssueWhat's Your Sweet Spot?
Are you in a niche that’s growing or shrinking? Is it time to reassess and refocus? We spotlight companies thriving by redefining or reinforcing their niche. What are their insights?
Moving Forward With Confidence
In this issue, we focus on sales and quoting, workforce training, new IPC leadership in the U.S. and Canada, the effects of tariffs, CFX standards, and much more—all designed to provide perspective as you move through the cloud bank of today's shifting economic market.
Intelligent Test and Inspection
Are you ready to explore the cutting-edge advancements shaping the electronics manufacturing industry? The May 2025 issue of SMT007 Magazine is packed with insights, innovations, and expert perspectives that you won’t want to miss.
- Articles
- Columns
- Links
- Media kit
||| MENU - smt007 Magazine
Don’t Allow Standards to Get the Better of You
August 31, 2015 | Michael Ford, Mentor Graphics Valor DivisionEstimated reading time: 2 minutes
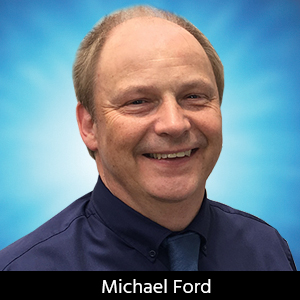
A standard should be complete, unequivocal, and consistent; it should be something that everyone can use and understand, promoting quality, responsibility, conformance, and compliance, as well as openness and visibility of information. In the electronics manufacturing industry, this just doesn’t seem to be the case, with so many different so-called standards for everything ranging from operational rules and documentation, to quality and traceability, which are confusing, incomplete, and represent a major cost and waste to manufacturing. Top-tier OEM companies are frustrated that they cannot get the information that they need, while manufacturers are also frustrated that they have so many different mandates to follow.
Surely, in the coming Internet of Manufacturing (IoM) age, where standardization of communication and storage of information will be critical, the current way in which we approach and adopt standards in electronics manufacturing cannot prevail, can it?
When OEM companies all did their own PCB assembly manufacturing in-house, it was the age of the engineer. Industrial engineers were responsible for the specification and execution of the various production processes and flows that connected them together.
Quality management engineers ensured that all products that left the factory were free of defects. The science of quality management and control as well as that of industrial engineering progressed rapidly. The comparison of market defect analysis with internal quality reports led to active quality management so that the scope and risk of defect creation during production execution is a part of the process specification. The two engineering families in many cases now work together very closely, or as one.
Within a vertically integrated manufacturing operation, the control and management of quality yielded more than just one order of magnitude reduction of defects, both internally and externally in the market, an important factor for all brand name companies as the cost of poor quality in the market can significantly affect sales.
The market then changed direction, where many companies decided that instead of a “profitless” manufacturing operation overhead, the use of EMS outsourcing was a good way to go. The lure included the ability to manufacture products in lower cost areas of the world without the need for investment, where specialist manufacturing companies would have access to greater discounts on material. How though to ensure that these remote external contractors would achieve the same levels of quality as the experienced in-house teams? Documentation related to internal manufacturing practices were formalized into standards. Many of these started out as based on the internal individual company practice.
Two key principles of control were formed, one that the process operation and flow would conform which the OEM needed, and the other pertaining to data collection as proof of correct operation, which doubled as a quality assurance tool, although this latter case is less used than many would believe.
Editor's Note: This article originally appeared in the August 2015 issue of SMT Magazine.
Suggested Items
Hon Hai Education Foundation Continues to Promote Quantum Education
07/04/2025 | FoxconnHon Hai Education Foundation has long been committed to promoting forward-looking technology education in Taiwan's high schools, and held the "High School Quantum Teacher Training Camp" in Tainan City on July 1.
Incap UK Achieves JOSCAR Zero Accreditation
07/04/2025 | IncapIncap Electronics UK has been accredited under JOSCAR Zero, a new sustainability-focused extension of the defence and aerospace sector’s supplier assurance system.
Kitron Secures Contract for Components Supporting Unmanned Aerial Systems
07/04/2025 | KitronKitron has received a contract with an estimated value between EUR 4 and 8 million for the production and supply of advanced electronic components used in unmanned aerial systems (UAS).
NOTE Receives Order Worth 132 MSEK and Expands Collaboration with Customer within Security & Defense
07/04/2025 | NOTENOTE has received an order worth SEK 132 million from one of its existing customers operating within Security & Defense. NOTE thereby strengthens its long-term collaboration with the industry-leading customer.
Delta SEA Partner Event 2025 Unites Regional Partners to Embrace a “Future Ready” Vision
07/03/2025 | Delta ElectronicsDelta Electronics (Thailand) Public Company Limited, successfully hosted its Delta SEA Partner Event 2025: Future Ready at Delta Chungli Plant 5, Taiwan on June 10 – 11 , 2025.