-
- News
- Books
Featured Books
- pcb007 Magazine
Latest Issues
Current IssueInventing the Future with SEL
Two years after launching its state-of-the-art PCB facility, SEL shares lessons in vision, execution, and innovation, plus insights from industry icons and technology leaders shaping the future of PCB fabrication.
Sales: From Pitch to PO
From the first cold call to finally receiving that first purchase order, the July PCB007 Magazine breaks down some critical parts of the sales stack. To up your sales game, read on!
The Hole Truth: Via Integrity in an HDI World
From the drilled hole to registration across multiple sequential lamination cycles, to the quality of your copper plating, via reliability in an HDI world is becoming an ever-greater challenge. This month we look at “The Hole Truth,” from creating the “perfect” via to how you can assure via quality and reliability, the first time, every time.
- Articles
- Columns
- Links
- Media kit
||| MENU - pcb007 Magazine
Rogers Highlights Thermally Enhanced 92ML Materials at electronica
November 21, 2016 | Judy Warner, I-Connect007Estimated reading time: 8 minutes
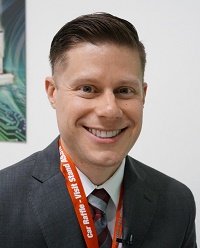
I met with Rogers Corporation Business Development Manager John Ranieri at Electronica in Germany recently. Ranieri’s professional focus is on the 92ML™ series of laminate, prepregs, and IMS, which was highlighted at the Munich show. The 92ML products are geared for the power electronics marketplace where thermal management is a major concern.
Judy Warner: John, you're a long-time friend from Rogers, and here we are at electronica 2016 on the last day of the show. I'm sure you're ready to get off your feet, as I am! Would you tell us a little bit about how electronica has been for Rogers?
John Ranieri: It's been very good. Just the sheer scope of the show is impressive. It’s far beyond anyone’s ability to see the whole show in one day. Every different type of electronics manufacturer is represented, too. I haven't experienced anything like it.
Warner: It is massive—I think about 12 halls in total. How has the booth traffic been for you?
Ranieri: It's been very good. We've got a lot of customers coming by. Of course, we like to see all the customers that we work with regularly but then also like to meet some new, potential customers as well.
Warner: John, we've known each other through Rogers Advanced Connectivity Solutions in relation to RF and microwave applications, which has been the primary focus of Rogers Circuit Materials. I understand recently you've had a change of position at Rogers and that you've launched a new material. Can you tell us a little bit about that?
Ranieri: That’s right, I'm working to promote and further develop a product platform called the ML Series™ of thermally enhanced FR-4 modified epoxy materials. The materials are available in laminate and prepreg form, which allows you to build multilayer PCBs, or as an insulated metal substrate (IMS). They are thermally conductive but electrically insulating. What that allows you to do is spread heat across the X and Y direction of the board, but also then conduct heat through the Z direction of the board. This allows the components and the junction temperature in the components to stay very cool, allowing you to sometimes avoid using more expensive and bulky types of thermal management solutions like heat spreaders, heat sinks, phase change materials, heat pipes, and the other myriad of solutions that are out there. Lower component temperature also leads to longer board life.
Warner: How did Rogers come about getting into thermal management solutions as opposed to their traditional high-speed materials?
Ranieri: Rogers has a lot of experience with power electronics. In fact, we have a whole division called Power Electronic Solutions, or PES. In that division we make direct bond copper materials, which is copper that is directly bonded to ceramic and used in very high-power applications. This specific product rolls up under our Advanced Connectivity Solutions and it's a material that we gained through the Arlon acquisition we completed last year in 2015. Like you had mentioned, it's a little bit different than the norm for us. Everybody knows Rogers for RF and microwave materials. If you think of Rogers in the printed circuit board industry, I think most people think of antennas and power amplifiers, for example. This is a little bit different point of focus for us, but again, we have a lot of experience as a company with these types of materials and we hope to leverage that in this new area for ACS.
Warner: If our readers are engineers and designers in a power electronics application, why would they chose the 92ML series?
Ranieri: First, we work directly with OEMs. Our sales force is advanced in working with OEMs and helping them with design for both performance and manufacturing. Specifically, with the ML series, the way that we think about it is there really are a few applications that require thermal management within a certain power range. One is LED materials, or LED electronics. Then there are some other applications like power converters, motor controllers, power supplies, engine control units, and inverters for solar power, for example, which require some level of thermal management. Where these materials are needed is where standard FR-4 materials are not good enough to manage the thermal performance that's required.
Warner: One thing came to mind when you were talking about the other, say, bulkier heat sinks and spreaders and things that are used in thermal management. Is the actual weight and footprint of some concern for these engineers?
Ranieri: In some circumstances, the weight can absolutely be an issue. In others, it's just a matter of the space. For example, if you look at consumer electronics, handheld electronics and wearable electronics, they have some critical thermal management issues they need to deal with in these areas. As far as generating heat inside the device, every year in designs they're trying to put more into every device, and in the case of wearables, devices are getting smaller and yet the outside temperature of the case must remain at 37° to 40°C because it comes into contact with a person's skin. In that case, the amount of thermal management that can be done inside these devices is somewhat limited. One of the solutions that you see is heat pipes, but heat pipes do have a cost to them and take up space. In using thermally conductive PCB materials, you're not taking up as much space as you would with a heat pipe because you already must have a PCB in that area. In the automotive area, space, weight, reliability, and cost are all critical. We think this solution addresses each of those issues.
Warner: You mentioned earlier something about it being environmentally friendly and halogen-free. Can you talk about the environmental impact of this material?
Ranieri: Absolutely. The 92ML materials are halogen-free. The challenge with making a material that's halogen-free is that most materials that are either epoxies or some sort of a thermoset resin system must have a flame retardant included in them. To build a material that has a flame retardant that is environmental friendly is often a challenge, and we've been able to do that with the 92ML materials.
Warner: What challenges are there for Rogers to create a halogen-free, environmentally friendly material?
Ranieri: Many applications have a UL requirement. There are a couple levels of UL requirement. One is just the flame rating. This is the UL94 rating system. These materials are what’s called UL 94 V-0, which is the strictest rating that you can get for these materials. That's a vertical flame test, essentially. What it means is that when you put the material under a flame it won't continue to burn on its own.
The other part of UL that's very important is MOT, which is the maximum operating temperature. That's a rating that tells you how high of a temperature you can continuously operate the material without significantly degrading it either electrically or mechanically over a long period. For these materials, the rating is 150°C over 3 mils. That is a very high rating for any FR-4 material. It's also very important in power electronics because a lot of designers are operating near those temperatures, and so it becomes a really important feature.
Warner: What is the availability of this material, and do you foresee engineers and designers having any trouble with getting timely access to these materials?
Ranieri: These materials come out of our factory in Suzhou, China. The current lead time is 20 days. We also have the ability if there are recurring programs beyond the prototype phase to stock material locally. We can stock material either in the U.S. or in Europe for programs that require it. We're committed to meeting our customers' needs for deliveries and lead times and we would like to work directly with our customers to meet those needs.
Warner: Lastly, I want to ask you about the fabricator's end of it. How easy and/or difficult is it to work with? It's FR-4, so I'm assuming that it’s easy to work with, but tell us what it's like for the fabricators to work with these materials.
Ranieri: Sure. We have several very high-volume programs out there right now that are using these materials successfully. In general, the materials fabricate very similar to FR-4. In fact, some of these designs require up to four ounces of very thick copper in the inner layers. There are some things that you need to do to make sure you're successful, but it's very feasible to do them. We have a technical service team that's committed to helping our fabricators use the materials.
The other thing that's great about the material is it's laserable. If you want to do buildup and, for example, you want to do a construction that has a center core with thin layers of buildup on the outside, you can do sequential lamination with microvias and it's easily laserable.
Warner: You have a great sales and marketing team. Did you go to market with this same team or is there a dedicated team for this product?
Ranieri: We’re using our same team. Your local sales engineer is the person to ask about these materials if you have an interest. Again, we also have a global technical service team available to help PCB fabricators. We take a holistic approach to managing our customers across the full supply chain. We get involved with OEMs and make sure that the designs are feasible for high-volume manufacturing. Then we're able to get our technical service team involved with fabricators to make sure that they're able to use the materials and that they're successful the first time they go out with a prototype, and that they can transfer that into volume production if necessary.
Warner: Where can engineers and designers go to find out about this material? Do you have datasheets on your website?
Ranieri: Yes. I would suggest starting with the Rogers Technical Support Hub, found on our website. Designers can go there and look at the product literature. If they'd like to contact their sales engineer, ask questions or read a little bit more, they can also do that on our website.
Warner: Very good. John, thank you for your time here at Electronica and we wish you the best of luck.
Ranieri: Thank you.
Testimonial
"In a year when every marketing dollar mattered, I chose to keep I-Connect007 in our 2025 plan. Their commitment to high-quality, insightful content aligns with Koh Young’s values and helps readers navigate a changing industry. "
Brent Fischthal - Koh YoungSuggested Items
SINBON Celebrates Opening of New US Manufacturing Facility
08/21/2025 | PRNewswireLeading electronics system integrator SINBON Electronics Co., Ltd. held an opening ceremony on August 18 to celebrate its new 59,000-square-foot facility in Clayton, Ohio.
PEDC Call for Abstracts Deadline Extended to Aug. 31
08/20/2025 | I-Connect007 Editorial TeamThe second Pan-European Electronics Design Conference (PEDC) will take place Jan. 21-22, 2026, in Prague, Czech Republic. The call for abstracts deadline has been extended to Aug. 31. Organized jointly by the German Electronics Design and Manufacturing Association (FED) and the Global Electronics Association (formerly IPC), PEDC serves as a European platform for knowledge exchange, networking, and innovation in electronics design and development.
Nano Silver Inks Market Forecast Report 2025-2030
08/20/2025 | Globe NewswireThe Nano Silver Inks Market is expected to grow from USD 427.415 million in 2025 to USD 836.160 million in 2030, at a CAGR of 14.36%.
VVDN Expands Manufacturing Footprint into the UAE to Meet Global Demand
08/20/2025 | PRNewswireVVDN Technologies, a global provider of software, product engineering and electronics manufacturing services & solutions, today announced it is setting up a new manufacturing facility in the UAE as part of its global expansion strategy.
Kimball Electronics Veterans ERG Members Proudly Participate in the 5th Annual Honor and Remember Run
08/20/2025 | Kimball ElectronicsVeterans and Military Service Advocacy (VMSA) Employee Resource Group (ERG) members Michael Mosher (Database Administration Engineer), Michael Stone (Test Technician Team Lead), and Joshua Belcher (Application Development Manager) took part in the 5th Annual Honor & Remember Run, a meaningful event dedicated to honoring fallen service members. The race featured a powerful memorial wall constructed from dog tags.