-
-
News
News Highlights
- Books
Featured Books
- pcb007 Magazine
Latest Issues
Current IssueThe Hole Truth: Via Integrity in an HDI World
From the drilled hole to registration across multiple sequential lamination cycles, to the quality of your copper plating, via reliability in an HDI world is becoming an ever-greater challenge. This month we look at “The Hole Truth,” from creating the “perfect” via to how you can assure via quality and reliability, the first time, every time.
In Pursuit of Perfection: Defect Reduction
For bare PCB board fabrication, defect reduction is a critical aspect of a company's bottom line profitability. In this issue, we examine how imaging, etching, and plating processes can provide information and insight into reducing defects and increasing yields.
Voices of the Industry
We take the pulse of the PCB industry by sharing insights from leading fabricators and suppliers in this month's issue. We've gathered their thoughts on the new U.S. administration, spending, the war in Ukraine, and their most pressing needs. It’s an eye-opening and enlightening look behind the curtain.
- Articles
- Columns
- Links
- Media kit
||| MENU - pcb007 Magazine
Embedding Active and Passive Components in Organic PCBs for More Reliability and Miniaturization
June 20, 2017 | Thomas Hofmann, HOFMANN LEITERPLATTEN GMBHEstimated reading time: 3 minutes
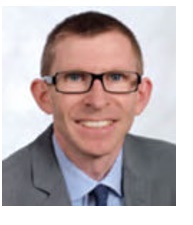
Abstract
Hofmann Leiterplatten GmbH has developed a wide range of products in the last 25 years. New manufacturing know-how has been developed in fabricating organic PCB with embedded devices. A special name, AML (active multilayer), was created to differentiate the surface mount devices (SMD) and the device embedded technology (DET) PCBs. Manufacturing processes that are not typical for standard PCB fabrication shops have been developed.
The paper explains typical applications where PCBs with embedded devices are used today. In addition, products with improved reliability will be shown and what are the benefits for the industry and the end user.
The last section in the paper will focus on future trends and the option for systems in PCBs (SiPCB). This enabling technology will open advanced production possibilities for improved reliability of high power electronics and harsh environment technology solutions. The paper will share specific knowledge applied in the production of products with embedded devices in PCBs more than 20 years. Important patents in Europe have expired. This will open a great opportunity for device embedded technology in PCBs as an excellent future potential for designers, PCB fabricators, EMS companies and OEMs.
Introduction
Thomas Hofmann founded Hofmann Leiterplatten GmbH in 1989. The objective was to provide special technology solutions based on printed circuit board technology to the electronics industry in Regensburg in Germany. During this time, many OEMs in Europe closed their in-house PCB fabrication sites to streamline the electronic equipment fabrication process. PCBs became commodities like standard passive and active components. The goal of the newly formed PCB factory started by Thomas Hofmann was to create innovative fabrication support for electronic designers and development engineers for large OEMs and EMS companies like Siemens, Osram, Infineon and many others in the Regensburg area. PCB fabrication technology was selected because this includes the widest range of fabrication technologies. Here are some examples of typical processes: mechanical drilling, mechanical and chemical milling, routing, photoimaging, screen printing, electroless and electroplating of different metals, and etching. These are considered as the enabling steps to produce a wide range of products. As a result, many innovative solutions are offered for various industries such as automotive and industrial electronics, lighting technology, measurement and medical technology, as well as the home automation sector. The following typical products are manufactured:
- Conventional printed circuit boards (PCBs)
- Active multilayer (AML)
- Active and passive front plates
- Printed board assemblies
- Metal core substrates (MCPCB or IMS)
- Printed circuit boards with embedded components
- Mechanical components and mechatronics
- Conventional front panel applications, front panels with integrated components (intelligent front panel)
The Trend in Device Embedding Technology
Embedding of passive components has been used in ceramic hybrid circuits since this technology was introduced in the beginning of the 1970s. Polymer thick film paste was used. OhmegaPly a resistor foil was available for PCBs as well. However, in mass production, only hybrid circuits are used. From the material point of view, this is an expensive technology selection. In cases where it is needed for reliability reasons, the higher cost has been justified. In mass production, the industry is looking for a more cost-effective solution based on organic PCB technology. Here the PCB fabrication technology has a clear advantage. Large panel production and standard multilayer processes offer an outstanding technology basis for embedding active and or passive components in the organic FR-4 material. As technology has evolved, smaller components made it easier to embed active and or passive components inside of PCBs by using the standards soldering or other component attachment technologies like gluing, sintering or plating. In 2011, the integration of embedded connector was evaluated by Hofmann Leiterplatten in Germany and introduced in the standard production of the latest design for device embedded technology. Examples are shown in Figures 16, 18 and 19.
The Process for Fabricating Device Embedding Technology PCBs
The surface mount device technology was an enabling way to place SMD parts on the surface of FR-4 CCL material on solder land layer of the PCB. This was then the important step to take the surface mount components to the inside of printed circuit boards (Figure 3, Step 1). For this process, a thin core CCL (0.36 mm) is used for mechanical stiffness during component placement. Thinner FR-4.0 and FR-4.1 laminate can be used. In our company, we have experience with both brominated flame-retardant that is used in FR-4.0 and the different flame retardant that are used in FR-4.1. We have gained experience with the resin flow, press condition and curing behavior of the important resin systems used in FR-4.0 and FR-4.1 CCL.
To read the full version of this article which appeared in the June 2017 issue of The PCB Magazine, click here.
Suggested Items
Driving Innovation: Direct Imaging vs. Conventional Exposure
07/01/2025 | Simon Khesin -- Column: Driving InnovationMy first camera used Kodak film. I even experimented with developing photos in the bathroom, though I usually dropped the film off at a Kodak center and received the prints two weeks later, only to discover that some images were out of focus or poorly framed. Today, every smartphone contains a high-quality camera capable of producing stunning images instantly.
Hands-On Demos Now Available for Apollo Seiko’s EF and AF Selective Soldering Lines
06/30/2025 | Apollo SeikoApollo Seiko, a leading innovator in soldering technology, is excited to spotlight its expanded lineup of EF and AF Series Selective Soldering Systems, now available for live demonstrations in its newly dedicated demo room.
Indium Corporation Expert to Present on Automotive and Industrial Solder Bonding Solutions at Global Electronics Association Workshop
06/26/2025 | IndiumIndium Corporation Principal Engineer, Advanced Materials, Andy Mackie, Ph.D., MSc, will deliver a technical presentation on innovative solder bonding solutions for automotive and industrial applications at the Global Electronics A
Fresh PCB Concepts: Assembly Challenges with Micro Components and Standard Solder Mask Practices
06/26/2025 | Team NCAB -- Column: Fresh PCB ConceptsMicro components have redefined what is possible in PCB design. With package sizes like 01005 and 0201 becoming more common in high-density layouts, designers are now expected to pack more performance into smaller spaces than ever before. While these advancements support miniaturization and functionality, they introduce new assembly challenges, particularly with traditional solder mask and legend application processes.
Knocking Down the Bone Pile: Tin Whisker Mitigation in Aerospace Applications, Part 3
06/25/2025 | Nash Bell -- Column: Knocking Down the Bone PileTin whiskers are slender, hair-like metallic growths that can develop on the surface of tin-plated electronic components. Typically measuring a few micrometers in diameter and growing several millimeters in length, they form through an electrochemical process influenced by environmental factors such as temperature variations, mechanical or compressive stress, and the aging of solder alloys.