-
- News
- Books
Featured Books
- pcb007 Magazine
Latest Issues
Current IssueInventing the Future with SEL
Two years after launching its state-of-the-art PCB facility, SEL shares lessons in vision, execution, and innovation, plus insights from industry icons and technology leaders shaping the future of PCB fabrication.
Sales: From Pitch to PO
From the first cold call to finally receiving that first purchase order, the July PCB007 Magazine breaks down some critical parts of the sales stack. To up your sales game, read on!
The Hole Truth: Via Integrity in an HDI World
From the drilled hole to registration across multiple sequential lamination cycles, to the quality of your copper plating, via reliability in an HDI world is becoming an ever-greater challenge. This month we look at “The Hole Truth,” from creating the “perfect” via to how you can assure via quality and reliability, the first time, every time.
- Articles
- Columns
- Links
- Media kit
||| MENU - pcb007 Magazine
Catching up with…Brigitflex
November 2, 2017 | Dan BeaulieuEstimated reading time: 7 minutes
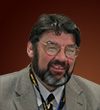
Where do you find an 8-foot R Card? Or an 18-oz. copper board? Why, you go to Brigitflex of course!
Just a few years ago, Brigitflex owner Brigitte Lawrence was in a jam. After 40 years in business things had gone from bad to worse. There was too much competition for her small company to withstand, especially offshore competition. She was losing market share at a rapid pace and what business she did have, she was losing to much lower-priced offshore sources.
She soon realized that if she did not change the way she was doing business she would no longer have a business. It was then that she had an epiphany as she considered her assets and thought about the possibilities. She decided to re-invent her company.
Instead of regretting what she didn’t have, she decided to focus on what she did have. In taking inventory, she realized what she should have known all along: Her husband, Chuck Lawrence, was capable of building anything, including any kind of PCBs that could be made. Chuck had always been a true outlier when it came to PCB technology since his start in the industry. Well known in the upper Midwest, Chuck was considered one of the truly great “mad scientists” of his generation. For years, people had been coming to him, asking him to build boards no one else could build. Ironically, this tended to irritate Brigitte who was trying to run a normal PCB shop while engineers were always coming in with distracting PCB technology challenges that Chuck just could not pass up. To him it was fun trying to build boards that no one had ever even tried before. To Brigitte trying it was just a distraction…sometimes a costly distraction.
Then it hit her to build her business around Chuck and his unique capabilities. She went back to the proverbial drawing board and re-invented her company as Brigitflex, a company that builds boards that no one else would even attempt. That was just a couple of years ago and the rest is history. Today, Brigitflex is building unique custom-made boards for companies all over the world, from large defense and aerospace companies to small incubator companies inventing new products. They have become well-known as the shop to go to when nobody else can solve your problems.
From the famous 8-foot rigid boards to long antenna boards to large R-cards, they build the most bleeding-edge products on the market today. They are also able to handle very thin (1/2-mil or thinner) materials on very large panels.
Not only is their shop unique, it is literally one of a kind since in many instances they have had to build their own equipment to handle their special projects.
Brigitte gives the impression that you are talking with a woman on a mission. This is not just a business to her, this is her life. The companies she deals with are not just customers, they are her friends, friends who have come to her with a unique problem and like a true friend she takes on their problems as if they were her own.
When I visited Brigitflex recently, I asked her what makes her company special and unique and this is what she said:
“What makes us different from every other PCB shop is our understanding, our belief that we are not just selling you a product. When you place an order with us, we become participants in the outcome of your design, packaging, and manufacturing efforts. We deeply value the good customer relationships we have built over many years of working in this industry. As in any good partnership, we believe in being honest and objective with our customers about any difficulties or problems that may arise. In fact, many times, on particularly challenging jobs the customer will come in a work side by side with us developing a process and successful building the boards. We love it when that happens.”
In talking with Brigitte, I tried to nail down exactly what technology they were good at. I wanted to get an idea as to what their actual niche was, but she would not be pinned down to a specific niche. Instead she told me:
“We don’t have a special technology niche unless you want to count the fact that we do what others cannot as a niche. Over the years, and especially the past couple of years, we have worked with many technologies including: very large boards, very thin boards, air dielectric boards, cavity antenna boards, filter boards, extremely long antenna boards, as well as PCBs that require embedded resisters, mixed dielectrics, conductive via fill, along with a couple of technologies or rather techniques that I cannot really talk about because of the numerous NDAs we have in place.”
Besides constantly developing and inventing new processes, Brigitflex also works in close partnership with their customers and laminate suppliers using laminates that have been developed by this three-way partnership, but that are not even on the market yet. Very often their customers have very special, very expensive and unique materials sent to Brigitflex by the laminate supplier so they can start working on the boards made from this laminate.
Again, Brigitte:
“When you work with Brigitflex you get 40 years of hands-on experience. Beyond our total in-house manufacturing and engineering capabilities, we have cultivated uniquely strong relationships with our suppliers and partners such as Rogers, Arlon, DuPont, Taconic, Sheldahl, Ticer and Ohmega, to name a few. Through these unique partnerships we can build what I like to call “products of the future” today Some of our development projects include pattern-plating on 3-D surfaces; thickness down to 10 microns. Huge multi-dielectrics, very heavy copper, .062 inner one-inch boards. We have also built special light weight air dielectric boards. Once again, the thing to remember is if an engineer can think it up and it’s a PCB, we will find a way to build it.”
What I found most interesting when talking with Brigitte was the informality of the way they do business. She and her team have a close relationship with their customers, so close that there is almost a shorthand between them. When walking through her receiving department Brigitte noticed that she had received a shipment of laminate from one of her partners and commented saying, “Well I guess we are going to be building the new boards for [she would not let me print the name of the customer] that we talked about the other day. That’s often how I know I am getting the order. The material just shows up and I call them and ask how many boards they want and when. That’s the way a lot of our business comes in, that’s how much we trust one another.”
After spending several hours in this little shop, and it is little by the way, my head was spinning. Even though I had seen the end-product and the custom-made equipment with my own eyes, I still found it hard to believe that this company could be doing the things they did and the way they were doing them. They were doing things that most of the larger well-equipped, well-manned and well-funded shops could not do so I asked Brigitte to try to explain to me how this could be possible. How could they do these things that the bigger guys could not?
She did not hesitate to give me her answer:
“To us business is not just business, it’s people. It’s people working together to try to do things that no one has ever done before. It’s people having each other’s backs and trusting each other. At our company we are always trying to figure out ways to do things better. We are always focusing on knowledge we have already, creativity, and science procedures and communications. We meet every morning at 7:00 a.m. over coffee to discuss the work on the floor. Together we go over problems and issues and how we are going to solve them. We also have 40 years of manufacturing experience; that’s 40 years of studying new materials and processes, cultivating relationships with our suppliers and keeping up with world progress. We try to learn as much from our customers as they learn from us. Because they trust is they talk to us about their new board requirements even while they are designing those boards. We also have our alpha shop testing materials and experimenting with new processes. We even have a machine shop on the premise which affords us the flexibility and control of keeping things in house. And speaking of controls we are always striving to keep our processes in complete control. And finally, we are completely dedicated to our customer’s success. Our day never ends at 5:00 p.m.; it ends when we are done for the day, whenever that is. Our ultimate goal is to make our customers’ concepts reality and we base everything we do on that premise.”
Testimonial
"Advertising in PCB007 Magazine has been a great way to showcase our bare board testers to the right audience. The I-Connect007 team makes the process smooth and professional. We’re proud to be featured in such a trusted publication."
Klaus Koziol - atgSuggested Items
How Good Design Enables Sustainable PCBs
08/21/2025 | Gerry Partida, Summit InterconnectSustainability has become a key focus for PCB companies seeking to reduce waste, conserve energy, and optimize resources. While many discussions on sustainability center around materials or energy-efficient processes, PCB design is an often overlooked factor that lies at the heart of manufacturing. Good design practices, especially those based on established IPC standards, play a central role in enabling sustainable PCB production. By ensuring designs are manufacturable and reliable, engineers can significantly reduce the environmental impact of their products.
50% Copper Tariffs, 100% Chip Uncertainty, and a Truce
08/19/2025 | Andy Shaughnessy, I-Connect007If you’re like me, tariffs were not on your radar screen until a few months ago, but now political rhetoric has turned to presidential action. Tariffs are front-page news with major developments coming directly from the Oval Office. These are not typical times. President Donald Trump campaigned on tariff reform, and he’s now busy revamping America’s tariff policy.
Global PCB Connections: Understanding the General Fabrication Process—A Designer’s Hidden Advantage
08/14/2025 | Markus Voeltz -- Column: Global PCB ConnectionsDesigners don’t need to become fabricators, but understanding the basics of PCB fabrication can save you time, money, and frustration. The more you understand what’s happening on the shop floor, the better you’ll be able to prevent downstream issues. As you move into more advanced designs like HDI, flex circuits, stacked vias, and embedded components, this foundational knowledge becomes even more critical. Remember: the fabricator is your partner.
MKS’ Atotech to Participate in IPCA Electronics Expo 2025
08/11/2025 | AtotechMKS Inc., a global provider of enabling technologies that transform our world, announced that its strategic brands ESI® (laser systems) and Atotech® (process chemicals, equipment, software, and services) will showcase their latest range of leading manufacturing solutions for printed circuit board (PCB) and package substrate manufacturing at the upcoming 17th IPCA Show to be held at Pragati Maidan, New Delhi from August 21-23, 2025.
MKS Showcases Next-generation PCB Manufacturing Solutions at the Thailand Electronics Circuit Asia 2025
08/06/2025 | MKS Instruments, Inc.MKS Inc, a global provider of enabling technologies that transform our world, today announced its participation in Thailand Electronics Circuit Asia 2025 (THECA 2025), taking place August 20–22 at BITEC in Bangkok.