-
- News
- Books
Featured Books
- pcb007 Magazine
Latest Issues
Current IssueInventing the Future with SEL
Two years after launching its state-of-the-art PCB facility, SEL shares lessons in vision, execution, and innovation, plus insights from industry icons and technology leaders shaping the future of PCB fabrication.
Sales: From Pitch to PO
From the first cold call to finally receiving that first purchase order, the July PCB007 Magazine breaks down some critical parts of the sales stack. To up your sales game, read on!
The Hole Truth: Via Integrity in an HDI World
From the drilled hole to registration across multiple sequential lamination cycles, to the quality of your copper plating, via reliability in an HDI world is becoming an ever-greater challenge. This month we look at “The Hole Truth,” from creating the “perfect” via to how you can assure via quality and reliability, the first time, every time.
- Articles
- Columns
- Links
- Media kit
||| MENU - pcb007 Magazine
HDI: Born in the USA and Making a Comeback
November 22, 2017 | Patty Goldman, I-Connect007Estimated reading time: 4 minutes
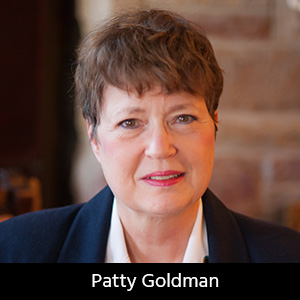
There is no denying that high-density interconnect (HDI) has been around a long time—over 25 years, believe it or not. From almost the moment of its conception in the U.S., the technology was adopted by and used almost exclusively in Asia. It was a puzzlement—and a frustration—as to why the quick move to Asia, and why the U.S. did not pick up on this technology and start making these boards. However, Taiwan, et al., were making most of the consumer products such as cellphones and camcorders, and HDI helped pack the necessary computing power into these devices.
But HDI is back! In this month’s reader survey, we learned that while half of the respondents have less than 25% of their production in HDI boards, for some 28% it accounts for more than half their business, and a for a third of those, HDI is their main technology (Question 1). In addition, 30% of all respondents expected their percentage of HDI work to grow to at least 25% and 45% expected it to represent more than half their business (Question 2).
According to our respondents, the three main industry segments using HDI were telecommunications, automotive and consumer electronics. We then asked about market trends: What market trends are driving your HDI work? Obviously, a multi-answer question, but note that many of the answers have to do with density on the board (Question 3).
Now, think back 25 years and you realize that fine features on a PCB were certainly not the same as they are now, and neither were the chip packages being used. Drilling, imaging and other PCB processes have made significant advances as you can imagine. And today’s densely-packed semiconductor packages are making HDI a necessity for many types of boards for many more applications—think electronics in cars, medical electronics and your incredible smartphone—all making use of components with many, many more I/Os and finer pitches (imagine what Moore’s Law has done in 25 years!). How to fit all those connections into a finite area on a PCB? So, it’s with all this in mind that we delve into this month’s issue on HDI, which is not for the faint of heart or the light reader!
Of course, we can’t talk about HDI without first hearing from the acknowledged “Father of HDI,” Happy Holden. And Happy has put together our intro article on the subject. He provides the proverbial wakeup we need to move all the faster into it. He points out concerns and obstacles and what needs to be done to overcome them.
Continuing in this theme, Mike Carano, RBP Chemical Technology, discusses in his col umn the practical competencies needed by a PCB fabricator to be a successful manufacturer of HDI boards. Consultant Vern Solberg continues with a more design-focused view—or perhaps explanation—of the rather recent surge in HDI. He not only thoroughly explains the need for HDI based on the increased package density, but also discusses both imaging and via formation.
This is a heavy-duty column for the PCB manufacturer, but definitely something you should read. As usual, we pulled together some experts who could intelligently explain some of this to us, as well as our readers. Our group consisted of Finisar’s Steve Bird, APCT’s Tony Torres, and several technologists from MC Assembly: Steve Jervey, Mike Smyth and Paul Petty. We learned a great deal about the latest technology, manufacturing challenges and strategies for design, fabrication and assembly—and you will too.
OK, let’s take a break and talk about something else. Elmatica’s Andreas Lydersen makes the case for a common PCB language called CircuitData. This open source standard was conceived to help prevent insufficient and erroneous article specifications that occur far too often between designer and manufacturer, often due to the many ways to describe even simple items like solder mask. This project sounds like a very good idea and one you should consider participating in.
Next, Tara Dunn, Omni PCB, writes about FlexFactor, a NextFlex program to help grow the next generation of advanced manufacturing workforce. She starts by listing several interesting electronics-based products that have been conceived by high school students and goes on to describe the four-week program and some of its encouraging results.
IPC’s John Mitchell also writes along these lines, covering the nationally recognized Manufacturing Day, which occurs on the first Friday in October. This day gives manufacturing companies the opportunity to present their company to their communities by inviting businesspeople, students, teachers and other community members, into their companies. It serves as a perfect venue to inform on career options in manufacturing, including the electronics industry.
OK, everyone. This issue is definitely required reading, so get on it. You need this technology and you need to read about it here. Next month we’ve got a hot one for you: an issue devoted to thermal management. We want you to learn and thrive in our industry and we’re doing our best to help you do that. If you haven’t already put yourself on our waiting list, what are you waiting for? Subscribe now and get a leg up on your competition. Move!
Patricia Goldman is managing editor of The PCB Magazine. To contact Goldman, click here.
This article originally appeared in the November 2017 issue of The PCB Magazine, click here.
Testimonial
"The I-Connect007 team is outstanding—kind, responsive, and a true marketing partner. Their design team created fresh, eye-catching ads, and their editorial support polished our content to let our brand shine. Thank you all! "
Sweeney Ng - CEE PCBSuggested Items
Indium Corporation Promotes Two Leaders in EMEA (Europe, Middle East, and Africa) Markets
08/05/2025 | Indium CorporationWith its commitment to innovation and growth through employee development, Indium Corporation today announced the promotions of Andy Seager to Associate Director, Continental Sales (EMEA), and Karthik Vijay to Senior Technical Manager (EMEA). These advancements reflect their contributions to the company’s continued innovative efforts with customers across Europe, the Middle East, and Africa (EMEA).
MacDermid Alpha Electronics Solutions Unveils Unified Global Website to Deepen Customer, Talent, and Stakeholder Engagement
07/31/2025 | MacDermid Alpha Electronics SolutionsMacDermid Alpha Electronics Solutions, the electronics business of Elements Solutions Inc, today launched macdermidalpha.com - a unified global website built to deepen digital engagement. The launch marks a significant milestone in the business’ ongoing commitment to delivering more meaningful, interactive, and impactful experiences for its customers, talent, and stakeholders worldwide.
KOKI to Showcase Analytical Services and New HF1200 Solder Paste at SMTA Guadalajara 2025
07/31/2025 | KOKIKOKI, a global leader in advanced soldering materials and process optimization services, will exhibit at the SMTA Guadalajara Expo & Tech Forum, taking place September 17 & 18, 2025 at Expo Guadalajara, Salón Jalisco Halls D & E in Guadalajara, Mexico.
Weller Tools Supports Future Talent with Exclusive Donation to SMTA Michigan Student Soldering Competition
07/23/2025 | Weller ToolsWeller Tools, the industry leader in hand soldering solutions, is proud to announce its support of the upcoming SMTA Michigan Expo & Tech Forum by donating a limited-edition 80th Anniversary Black Soldering Set to the event’s student soldering competition.
Koh Young Appoints Tom Hattori as President of Koh Young Japan
07/21/2025 | Koh YoungKoh Young Technology, the global leader in True 3D measurement-based inspection solutions, announced the appointment of Tom Hattori as President of Koh Young Japan (JKY).