-
- News
- Books
Featured Books
- pcb007 Magazine
Latest Issues
Current IssueInventing the Future with SEL
Two years after launching its state-of-the-art PCB facility, SEL shares lessons in vision, execution, and innovation, plus insights from industry icons and technology leaders shaping the future of PCB fabrication.
Sales: From Pitch to PO
From the first cold call to finally receiving that first purchase order, the July PCB007 Magazine breaks down some critical parts of the sales stack. To up your sales game, read on!
The Hole Truth: Via Integrity in an HDI World
From the drilled hole to registration across multiple sequential lamination cycles, to the quality of your copper plating, via reliability in an HDI world is becoming an ever-greater challenge. This month we look at “The Hole Truth,” from creating the “perfect” via to how you can assure via quality and reliability, the first time, every time.
- Articles
- Columns
- Links
- Media kit
||| MENU - pcb007 Magazine
HDI: Today, Tomorrow and the Future
December 5, 2017 | I-Connect007Estimated reading time: 5 minutes
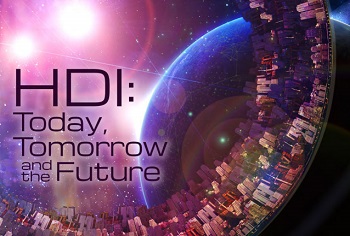
For this month’s issue, our editorial team interviewed some of the top HDI experts in the PCB supply chain. Joining us on the conference call were Steve Bird, PCB/flex technology manager at Finisar, and Tony Torres of APCT. Also on the call were several technologists from MC Assembly: Vince Burns, quality engineer; Steve Jervey, director of Test Engineering; Mike Smyth, SMT engineer; and Paul Petty, product engineer. This wide-ranging conversation covered the latest technology developments, manufacturing challenges, and HDI strategies, from the design, fabrication, and assembly perspectives.
Andy Shaughnessy: Why don’t we start with design? Steve, you’re an HDI technology manager, so you’re driving this whole thing. Why don’t you tell us where you guys are with HDI?
Steve Bird: Sure. I’m wearing two hats. One is technical lead for the EEs and the CAD designers here at Finisar, and the second one is organic substrate roadmapping and development. Maybe 18 months or two years ago, we were working with a fabricator. We started cheating on the FR-4 design rules, and to their credit they built over 1,500 of these over a period of a year or so and finally gave it up and said, “No bid.” So of course, the upper management team came to my group saying, “You’re violating the design rules.” And I said, “Yes, but not without an engineer sitting next to the CAD designer. And yeah, we did, but what we have here really is not a design rule violation, but a technology limitation.”
That spun off an effort to find a substrate that could support the design rules that we’re cheating to. Our PCB technology team was tasked with the effort. We got one new substrate developed and released, but now those new design rules are being violated; we have to continue development. For that previous generation, once we got off FR-4 and onto alternate materials, we were still in the subtractive process. Now we’re looking very heavily at the semi-additive process. Our trace with normal FR-4 is going from 4 mil trace and space down to say, 3.5 mil, roughly, and that’s what earned us the no-bid. Now we’re at two mil trace and three mil space, and that’s still not good enough.
So, we’re continuing to increase the density, and for us, our whole game is no vias, no stubs, and no parasitics. Everything’s predictable: no glass weave, etc. So what we’re looking at is thinner and thinner laminate, and hybrid stack-ups. We can certainly do all our power delivery and control signal distribution on FR-4 layers, but what lies on that surface is important to us. We can do small modules, system-type modules for our ICs and such, our chip-on-board and so on, but really what we need is a full system-level surface layer that can support those types of densities and mount chips.
That’s really what we are working towards right now. We’re now looking at 20−25-micron traces and 25−40-micron gaps, and seeing if we can’t do that. If we can, then we can support all our chip mounting technologies. We can support our system-level traces that get from the origin to the destination and so on. When we do that, then of course these traces get very lossy, and that becomes a huge concern. So our antidote to that is keep them short. Get them shorter. And so that’s kind of our roadmap in a nutshell. We’re starting with surface density, because the propagation is the fastest, keeping it stubless, and then making the net as short as possible. We run everything that’s important differentially for noise immunity. So, you can imagine the types of stackups we’re looking at in terms of hybrid stack-ups and so on.
Shaughnessy: What sort of materials are working out best for you?
Bird: When we first started this effort, my boss asked me, “What would you use? What’s the first step that you would do?” My response was, “Thin, glass-free laminates. Something that’s just as thin as you can make it.” Let me put it this way: There is a slide that shows FR-4 with traces and spaces in the 4 mil range. With the help of HDI, we then took the through-hole off HDI: TODAY, TOMORROW AND THE FUTURE the surface and stacked the blind and buried vias. We call this technology level modified FR- 4. This got us to 3.5 mil trace/space. There is another slide called the constant impedance funnel for differential pairs. You can imagine this funnel that starts out in the FR-4 at 4 mil trace/space and goes all the way down to be something like chip-on-glass or ceramic at 0.6 mil trace/space. One can place a large bracket in the gap with a label saying “This gap is too large. This gap is responsible for chewing up real estate because things are not scalable.” The things that you do on an IC or on glass, you have a lot of overhead in terms of the splay angle, trying to get the signals out (escaped) and getting them routable.
We are trying to solve that. Because once you solve the trace to be similar to the pin or pad pitch, then your channels become much more scalable on the surface. By the way, as we’re going up in frequency, we’re also going up in channel count. We’re getting whacked from both sides. We need to step back and look at what design rules we need. If we’re at 25-micron trace and 40-micron gap, things such as channel count and speed become much more manageable. Now the trace has become much shorter. From a signal integrity standpoint, the first thing to do is get rid of all your parasitics, get rid of all your stubs, trace, tie-bars, etc., as well as your parallelism and propagation delay; get rid of everything that will kill a signal, and then go for improved material. That’s where we’re at right now. We’re searching the world for the best material with the best copper with the best adhesion, which means the best processes in terms of subtractive, additive or semiadditive. Then of course the vias stick out like a sore thumb, and even 25-micron vias stick out like a sore thumb to us. So it’s very important that we go vialess for all our high-speed traces. If we do that, then we can get to where we want in organic material. My whole point is, let’s be organic if we can, and I don’t think we’re done being creative here.
This article originally appeared in the November 2017 issue of The PCB Magazine, click here.
Testimonial
"We’re proud to call I-Connect007 a trusted partner. Their innovative approach and industry insight made our podcast collaboration a success by connecting us with the right audience and delivering real results."
Julia McCaffrey - NCAB GroupSuggested Items
How Good Design Enables Sustainable PCBs
08/21/2025 | Gerry Partida, Summit InterconnectSustainability has become a key focus for PCB companies seeking to reduce waste, conserve energy, and optimize resources. While many discussions on sustainability center around materials or energy-efficient processes, PCB design is an often overlooked factor that lies at the heart of manufacturing. Good design practices, especially those based on established IPC standards, play a central role in enabling sustainable PCB production. By ensuring designs are manufacturable and reliable, engineers can significantly reduce the environmental impact of their products.
50% Copper Tariffs, 100% Chip Uncertainty, and a Truce
08/19/2025 | Andy Shaughnessy, I-Connect007If you’re like me, tariffs were not on your radar screen until a few months ago, but now political rhetoric has turned to presidential action. Tariffs are front-page news with major developments coming directly from the Oval Office. These are not typical times. President Donald Trump campaigned on tariff reform, and he’s now busy revamping America’s tariff policy.
Global PCB Connections: Understanding the General Fabrication Process—A Designer’s Hidden Advantage
08/14/2025 | Markus Voeltz -- Column: Global PCB ConnectionsDesigners don’t need to become fabricators, but understanding the basics of PCB fabrication can save you time, money, and frustration. The more you understand what’s happening on the shop floor, the better you’ll be able to prevent downstream issues. As you move into more advanced designs like HDI, flex circuits, stacked vias, and embedded components, this foundational knowledge becomes even more critical. Remember: the fabricator is your partner.
MKS’ Atotech to Participate in IPCA Electronics Expo 2025
08/11/2025 | AtotechMKS Inc., a global provider of enabling technologies that transform our world, announced that its strategic brands ESI® (laser systems) and Atotech® (process chemicals, equipment, software, and services) will showcase their latest range of leading manufacturing solutions for printed circuit board (PCB) and package substrate manufacturing at the upcoming 17th IPCA Show to be held at Pragati Maidan, New Delhi from August 21-23, 2025.
MKS Showcases Next-generation PCB Manufacturing Solutions at the Thailand Electronics Circuit Asia 2025
08/06/2025 | MKS Instruments, Inc.MKS Inc, a global provider of enabling technologies that transform our world, today announced its participation in Thailand Electronics Circuit Asia 2025 (THECA 2025), taking place August 20–22 at BITEC in Bangkok.