-
- News
- Books
Featured Books
- pcb007 Magazine
Latest Issues
Current IssueInventing the Future with SEL
Two years after launching its state-of-the-art PCB facility, SEL shares lessons in vision, execution, and innovation, plus insights from industry icons and technology leaders shaping the future of PCB fabrication.
Sales: From Pitch to PO
From the first cold call to finally receiving that first purchase order, the July PCB007 Magazine breaks down some critical parts of the sales stack. To up your sales game, read on!
The Hole Truth: Via Integrity in an HDI World
From the drilled hole to registration across multiple sequential lamination cycles, to the quality of your copper plating, via reliability in an HDI world is becoming an ever-greater challenge. This month we look at “The Hole Truth,” from creating the “perfect” via to how you can assure via quality and reliability, the first time, every time.
- Articles
- Columns
- Links
- Media kit
||| MENU - pcb007 Magazine
What Happens to Our Industry Without a Skilled Workforce?
April 3, 2018 | Dr. John Mitchell, IPCEstimated reading time: 4 minutes
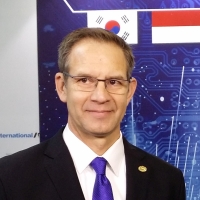
I’d like to discuss a critical issue facing our industry—the skills gap—and IPC’s commitment to supporting its members as we collectively seek to find solutions. Over the coming weeks and months, we plan to actively engage you, our members, to understand how IPC can be part of the solution. There are many exciting workforce, training and education initiatives out there—spanning Earn and Learn models to students building robots of the future. The question is: How do you know what is right for your company and how can IPC help?
We know what challenges we are facing—unfilled jobs, an unemployed or underemployed workforce, a decrease in job loyalty, and a rapid, unprecedented increase in technology and information, making it hard for us to keep up with the constant change, but what are we going to do about it? We at IPC have some ideas.
When I talk to manufacturing representatives throughout the country and internationally, the same worry concerns all of them—how are we going to recruit skilled workers? Where do we find individuals that have the skills and knowledge we need to be competitive and successful? What happens to our industry without a skilled workforce?
In an IPC study done in the US, we learned that 66% of companies have a difficult time finding production workers, and 64% have a difficult time finding engineers. According to Deloitte and the Manufacturing Institute, it is estimated that in 2025, two million manufacturing jobs will go unfilled due to the skills gap. This is not only a problem in the United States, but internationally. Statistics show that the percentage of jobs available in the European Union has nearly doubled over the past decade, and China will have 65,000 additional jobs available by 2020.
This is alarming to all of us, and indicates the issue’s criticality. It illustrates clearly how we need to change the message and culture around factory work and what it really entails. Because today’s workplace has become increasingly technical, greater knowledge and expertise is required of employees. And we in the industry need to provide that education and expertise to help the industry grow and succeed.
Not only do we need to change our focus when it comes to education, but we need to change our idea of who can fill the available jobs. Five generations are now in the workforce—from millennials to boomers—and each generation has different motivations and expectations from the work place. It’s important to pay attention to that and react accordingly. For example, in 2020, 50 percent of management jobs will be held by millennials, a generation that wants to make positive change in the world by doing a job that is meaningful to them. If they don’t find meaning in their job, they tend to leave for another one. The same is true of women in the workforce, who are looking for companies that support gender equality, management potential, work/life balance and family-friendly workplaces.
There are several options for training a workforce, including traditional schooling, ad hoc training, online training and apprenticeships—all important options to pursue. IPC is doubling down its commitment to its members to help address the pervasive and ever-widening skills gap issues. As I’ve mentioned, we will be reaching out to members to share preliminary ideas and potential solutions as we believe the success of any workforce program or initiative must be industry-led. One such solution is IPC EDGE, a cloud based learning management system that IPC launched in July 2016.
Other avenues we are pursuing include applying for grants and subsidies to help businesses obtain training for their staff. We are reaching out to local community colleges to provide technical training and scholarships for students interested in pursuing a career in manufacturing. We are also actively involved in several STEM programs across the country. Our Job Task Analysis committee is examining critical job roles in the electronics industry with the express purpose of mapping the knowledge, skills and abilities required to perform these job functions.
In addition, IPC plans to hold a webinar in the coming months that will provide more detailed information and answers to any workforce questions you may have. We firmly believe that IPC can make a significant and positive difference in addressing workforce development in the U.S. and worldwide. While it is critical to address the skills gap, it is also important to budget for the investment needed to do so. Recent tax breaks in the U.S. tax code provide us with an opportunity to invest in our people, modernize our facilities, and update our technology. By investing in staff training and building a stronger workforce, will remain competitive in the industry. Extra money can be used for acquisitions such as updating our facilities and for research and development to help with strategic planning.
IPC is ready to help you find ways to address the issue of workforce skills gaps. We believe in maximizing the use of your membership in a trade organization. We are thrilled to have you as members of IPC, and we’re here to help you address this critical issue. IPC is fully committed to helping your business maintain its high standard by assisting in getting you the educated workforce you need.
Testimonial
"Our marketing partnership with I-Connect007 is already delivering. Just a day after our press release went live, we received a direct inquiry about our updated products!"
Rachael Temple - AlltematedSuggested Items
Lessons From a Thousand Columns: Dan Beaulieu on Writing, Selling, and Staying the Course
08/21/2025 | Michelle Te, I-Connect007For 20 years, Dan Beaulieu has been a steady voice in sales and marketing, offering weekly columns that challenge, inspire, and guide professionals in the electronics industry and beyond. Soon, he will reach a remarkable milestone—his 1,000th It’s Only Common Sense weekly column. In this Q&A, we look behind the scenes of Dan’s writing journey, exploring what has kept him motivated, the lessons he’s learned along the way, and how two decades of weekly columns have shaped his career and the industry conversation.
University Of Minnesota Team Claims Victory In Bright Manufacturing Challenge 2025 Round 1
08/19/2025 | EMACThe Electronics Manufacturing & Assembly Collaborative (EMAC) recently announced that Team "Rise and Grind Crew" from the University of Minnesota has emerged victorious in Round 1 of the Bright Manufacturing Challenge 2025.
The Knowledge Base: Cultivating Your Brand in the Age of Connection
08/19/2025 | Mike Konrad -- Column: The Knowledge BaseAudiences have evolved in how they consume information, form opinions, and make purchasing decisions. While marketing still relies on tried-and-true methods—get your name and message in front of your audience—you must also cultivate connection, credibility, and community. Your customers, particularly the younger generation of engineers, buyers, and program managers, want to discover value on their terms.
American Made Advocacy: Where’s the Budget for a Modern Military Run on Microelectronics?
08/19/2025 | Shane Whiteside -- Column: American Made AdvocacyIn a world of peer threats and urgent transformation, having secure, trusted, and reliable microelectronics is non-negotiable. While largely hidden, microelectronics are the ubiquitous enablers of modern defense platforms. Nothing in the current American arsenal flies, floats, or fights without a technology stack that includes a semiconductor, an integrated circuit substrate, and a printed circuit board.
Meet with The Test Connection Inc. (TTCI) at SMTA Guadalajara 2025
08/18/2025 | The Test Connection Inc.The Test Connection Inc. (TTCI), a trusted provider of electronic test and manufacturing solutions for more than 45 years, is pleased to announce its participation at the upcoming SMTA Guadalajara Expo & Tech Forum, taking place September 17–18, 2025, at Expo Guadalajara, Salón Jalisco Hall D & E.