-
- News
- Books
Featured Books
- pcb007 Magazine
Latest Issues
Current IssueInventing the Future with SEL
Two years after launching its state-of-the-art PCB facility, SEL shares lessons in vision, execution, and innovation, plus insights from industry icons and technology leaders shaping the future of PCB fabrication.
Sales: From Pitch to PO
From the first cold call to finally receiving that first purchase order, the July PCB007 Magazine breaks down some critical parts of the sales stack. To up your sales game, read on!
The Hole Truth: Via Integrity in an HDI World
From the drilled hole to registration across multiple sequential lamination cycles, to the quality of your copper plating, via reliability in an HDI world is becoming an ever-greater challenge. This month we look at “The Hole Truth,” from creating the “perfect” via to how you can assure via quality and reliability, the first time, every time.
- Articles
- Columns
- Links
- Media kit
||| MENU - pcb007 Magazine
A Discussion About Everything Under the Sun
April 6, 2018 | Stephen Las Marias, I-Connect007Estimated reading time: 16 minutes
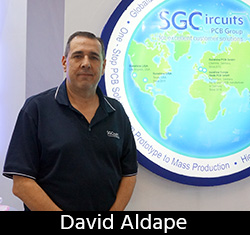
From flex circuits to HDI, Industry 4.0, leading market drivers, and materials—this wide-ranging discussion with Sunshine Global Circuits CTO David Aldape highlights the latest and future developments, challenges, and opportunities in the PCB manufacturing industry.
Stephen Las Marias: David, tell us more about your company and your role.
David Aldape: I’m the chief technology officer for Sunshine Global Circuits. Our headquarters are in Shenzhen. We also have facilities in Jiujiang, in the Jiangxi province, and we have a facility in Germany as well. In the United States, our main office is in Plano, Texas, and we have another office in Southern California. To create our organization’s model, we went after what we considered a neglected marketplace from the China-based manufacturing groups. We have been willing to fit the role of taking on a lot of the smaller orders, as well as pilot runs—not just looking for high volume production.
We are more of an engineering technology-driven organization. We build everything from two layers to 36 layers, HDI products, blind and buried vias, and we work with a lot of high-speed materials. We work closely with our customer base through the designers and engineers, and provide what we consider a value-added service.
Las Marias: So, you manufacture single-sided, multilayer, and HDI boards. Do you also deal with flex?
Aldape: Actually, yes. We have continued to expand our flex operation. We have seen an increasing call for flex circuits, as well as rigid-flex and more advanced flex circuit products utilizing new materials such as the liquid crystal polymers, as well as HDI technology, with filled micro vias and buried vias inside those types of products. Now, we’ve dedicated an entire floor in our Jiujiang operation, which will be 15,000 square meters of manufacturing space, strictly dedicated to flex and rigid-flex products.
Las Marias: There definitely has been an increase in those products.
Aldape: Oh, yes. We have noticed as we grow year-over-year, that increase in demand continues to grow, achieving an even higher rate than rigid products.
Las Marias: What do you consider the main drivers for this?
Aldape: A lot of it is coming through the automotive industry and smart technology, and the Internet of Things. We’re seeing that the communication is necessary, or the ability to fit tight form-factors, are the main drivers that we see taking place here. Then, lighter weight. Therefore, from an overall cost of these higher complexity products, it has been more beneficial from a cost standpoint to integrate flex or rigid-flex into it, compared to having cables, also because of the speed of the connections necessary.
Las Marias: You made a presentation at the technical conference about PCB technology trends. Can you give us a summary of that presentation?
Aldape: What we looked at were the trends in our marketplace now and in the coming years. What we find is that the major drivers tend to be performance, cost, packaging of devices, more form fit, as well as higher layer counts. Those tend to be the things that are driving this technology.
Now, the things that we deal with from that standpoint, if I'm looking at it from a perspective of the company and the things that we must understand, is the competition we have there in today’s world is more global. It’s not regional. So, we’re dealing with global competition. We’re also looking at things such as environmental costs that are driving our business. Materials, the cost competition between competitors, and a wealth of materials that we’re dealing with now.
Also, it’s not by looking at marketplaces themselves, or what’s driving the marketplaces. I look at things such as the Internet of Things, 5G technology, and autonomous vehicles. We must look at the smart technology, where I need to have communication maybe going around a building now instead of a straight line of sight. With medical, for example, there’s the ability for patient monitoring to be done where you’re not having to go into the actual clinic, or to the doctor. You can put on a device to monitor you, and even do a prescription, and do a real-time assessment of your health and how you’re reacting to medication, or how your body is functioning, and then actually do prescriptions that way to help people get a much quicker diagnosis.
Then also we see a lot of power consumption going on. For example, how we’re controlling our city grids. How can we be more efficient at that? Or solar technology, power and energy. Now, if I start breaking that down into what industries are using that, I will see the major drivers being industrial controls, medical, telecommunications, power and energy, aviation and security. These will be the major drivers that I've seen driving the industry.
Las Marias: From your experience, what are the challenges being faced by the industry right now?
Aldape: The challenges from the industry standpoint, as I see it right now, is that we need to get closer to our customer. As you go through the higher technology, there's more investment that’s going to be needed to take place to keep up with the technology requirements from that standpoint. So, we're going to have to do more investment. But we're also going to have to invest into services for our customers. In other words, I’m going to have to provide a value-added service to my customer to differentiate me from someone else.
I'm going to be working closer with the designers and engineers by understanding the products they want, what they need to build, and how they’re going to function. That way, I can better recommend material types for their systems that are more cost-effective, and not over-recommend material. Or, I can look at a product from a design for manufacturability standpoint, and can then, in turn, give them ideas on how to better make this more manufacturable.
So, as I get to the manufacturing operation, it is a much smoother transition, when I bring it from a conception stage to a reality and am building those products. I can build it more cost effectively, because I have fewer issues in manufacturing. And then I can give my customer what they need so that when their product performs, they’re performing as desired, and not going through as many iterations.
Capital investment in equipment is going to be one of keys to the future to keep up with technology, from the fabricator’s standpoint. So, what we're seeing from that standpoint is more automation taking place because the cost of labor continues to rise. The cost of environmental standards continues to rise. Material costs have been one of the costs that have remained there.
But I need to look at better ways to utilize my power and energy, as well as my manpower. Therefore, the individuals I want in those facilities, I need to maximize their services. So, the more I can automate my factory, the more I can cut down on, let's say, manual labor. And the individuals, I can maximize their time that they're going to use inside my facility to benefit the organization.
Las Marias: Are we getting near to a period when we will have a lights-out factory?
Aldape: We are getting close to that. There are many functions now that you can run lights-out operations. Take drilling, for example. Since we have loaders and autoloaders, if I have those set up properly, I can load up all those autoloaders and I can have my operation, as long as I’m running particular part numbers, switch it off when they’re ready to leave, and all that can continue to process without an operator. I can do the same thing with testing of boards, where I have stacks set up that will be able to do that for me. I can have automation, from the standpoint that I can have robots that are moving materials for me back and forth to the next operation and allow a lights-out operation.
So, that is coming more and more. With some of the most advanced equipment out there now, you can set up an individual, let's say when you are running, not lights out, but a single individual can be running a process where I used to have multiple individuals, because I had to have multiple processes that were separated. I can join those processes together, so I could have one individual running four or five processes together in an operation. You have eliminated the need for operator intervention from a handling standpoint. You have been able to maximize your efficiency and minimize your cost in doing so.
Las Marias: Because you minimize the operator handling, that will also result in improved yield.
Aldape: Handling is probably one of the biggest contributors of defects within a facility, and it always has been, whether it's here in China, Europe, or in the US. Handling is typically always your biggest contributor for defects. By minimizing that as much as possible, you’ve taken out a lot of the issues that used to take place, and from the standpoint of the cosmetics of the product, moving forward, that’s much better as well.
Las Marias: In the last year, the industry has been beset from a material standpoint—specifically, with the shortage of copper. Are you seeing that this year?
Aldape: The shortage of copper, as I understand it from my discussions with the material manufacturers, has about one more year left. The battery industry was absorbing all the copper—the majority of the copper suppliers shifted their manufacturing capacity to meet that demand, because it was a less costly process, and a higher profit yield. Since they’ve done that, now they’ve had to retool their facilities back up to meet the demand of the copper foils, as well as a lot of the new copper foils that are coming out. So, we are about a year away, and then hopefully, that shortage will be resolved.
Glass is still a shortage as well. We have seen lead times push out, because most of the glass manufacturers for the last few years were not making money. Now, they have looked at ways to retool those factories to make themselves more efficient—just like the copper guys did—to make themselves more efficient and to be able to achieve a profit at supplying that glass. So whenever you go to retool, you have a temporary time with a little bit of diminished capacity.
The other thing is, some of the glass styles that we use now are newer glass styles. You have the traditional glass styles, but now we need to build new glass styles such as the square weaves, or these much thinner glasses, such as the 1027s, 1017s, that weren’t previously available.
One of the things I brought forth in the presentation, especially with HDI products, is that we will see an increased need for thinner glass. We’re going to continue to see that trend with things getting smaller and thinner, and more compact. The 1027, 1017 glasses are going to become more and more in demand, and the use of those is expected to double within the coming year.
Las Marias: The industry has seen an increase in HDI use. What markets have been driving this?
Aldape: From the HDI standpoint, I think among the biggest drivers are the communication and automotive industries. From what I can see from my studies, take cars, for example, there’s already a lot of communication devices in it. The devices that we now have are controlling braking, controlling motors, and they need to be more compact. Therefore, HDI starts playing a bigger role in that.
Previously, cars had few circuit boards in them. Now, if you look at all the electronics inside a car, it’s like we’re driving a computer down the road, and it’s all interconnected. Now, we have somewhere upwards of 30 to 50 boards in every vehicle, and many of those include HDI. The HDI and BGAs have been getting smaller because they are necessary for routing purposes. Therefore, that is being done a lot as package sizes decrease and HDI becomes more common.
Las Marias: Is it true that by using HDI, you also reduce your cost?
Aldape: Yes, if you design it properly. You want to be able to trade off two layers for every one layer that you’re going to put in HDI. If you're just adding HDI, you’re not saving cost. You need to reduce layer count in order to get a cost advantage out of it. Otherwise, you're just putting HDI in there and you're going to increase cost, unless you're in a situation where you're able to design smaller and save on the packaging. But if you're not trading off layers, then you're really not taking the full advantage you can have with HDI technology and micro-via technology.
Las Marias: Going back to the communications market that you mentioned, definitely one of the things right now that people will need to focus on more is high-speed materials. What are the challenges here?
Aldape: The challenges for high-speed material, for most organizations, are going to be understanding it. One of the things that we have done at Sunshine is taken our R&D engineering group and partnered with four different material suppliers, so that we could work closely with their advanced material groups to have a good understanding of those materials. One, from how they process in our facility manufacturing with them, and the interaction of materials from a chemical and electrical standpoint. When I go to my customers, I can give them real data on how that material will function in their systems. Doing that gives us an understanding of those materials. We chose four, because you can’t work with them all. But by doing those high-speed materials, and as we get to higher and higher frequency, more and more understanding is needed on how those materials interact inside their systems. It's more than just building time domain reflectance. It's more than just controlled impedance. We need to look at insertion loss and how it reacted at those higher-gig levels.
Las Marias: Communication between the designers and the manufacturers is important, right?
Aldape: Yes. I believe that will become even more important as we go forward. One of the things that we've embraced from our side is being active on that front with the customers and being much more engineering-driven and more data-driven, whether we're doing it internally for manufacturing, or working with our customer base.
Las Marias: What do you think the environment will be like in 2018?
Aldape: 5G is coming at us. Therefore, higher speeds are necessary. From the flex standpoint, I would expect the flex market to grow somewhere around 6% on an overall basis with all the different organizations or all the different fields. On the other side, the layer counts will go up. We need to start concentrating more in the, let's say, eight- to 18-layer range. The two- to four-layer boards, you have 3,000 facilities out there that can manufacture that type of product. The price pressure is enormous, and it's very cutthroat. It's more like a cheap commodity versus building a technology. The shops that are only building that, in my opinion, are slowly outdating themselves. They're not keeping up.
I believe the telecommunications market is going to continue to grow, as well as the medical industry. I would be looking closely at that, and of course, automotive. Materials are going to become more important—and the understanding of those materials, I believe, will be more important as we go forward, if you want to be on the leading edge. There will always be the standard products out there, but if you want to be leading edge, that's where you need to start to focus some of your efforts.
The other thing I would expect now through 2020 is we should enjoy as an industry a 3-4% growth annually, worldwide. In 2018, the PCB industry should be somewhere around $71 billion, overall, and then looking at 3-4% year-over-year growth after that.
Las Marias: What can you say about the Industry 4.0 trend?
Aldape: I really like it, and I embrace it. I am continuing to try to integrate that into the factory as much as possible because we are going to need it as we move forward. The ability to have the collection of information that we can get out of that will only make us better. When we are able to have those machines feeding back real-time information to us, we can have tighter and tighter process controls. We create less variation, more consistency. Our yields increase, as well as it can start to tell us where to focus our efforts. It’s not just collecting data, it’s letting the data drive us. So, with the Industry 4.0, we get a much better overall picture of what is happening in the entire facility, our interactions within the facility, how the products are being produced in our facility, and knowing where to put our efforts going forward to be most efficient at that.
Las Marias: From your perspective, what is the decision process when it comes to deciding when or what new equipment to install or acquire?
Aldape: When we look at equipment, we're looking at something that is going to give us a path for growth. So, I'm looking out somewhere in the three- to five-year range on most of the equipment, even though the equipment should last, let's say, for the next 10 to 15 years; but it must give me a growth path for the next few years. I also look at it from a reliability standpoint. How reliable is this equipment going to be in my day-to-day use?
Another thing I look at is what kind of information that equipment can feed back to me. How can I utilize that equipment’s collected data that I can integrate into my system? A lot of the equipment are efficient enough to talk with other systems. Therefore, I'm using the software within these systems to help drive me to get better. There is a lot of equipment out there, and there are a lot of claims out there on what equipment can do—so you need to do your homework. We need to remember when we’re selecting equipment, it’s a major purchase. Therefore, it isn't something we're going to quickly replace. We need to run the proper testing and make sure it’s a proper fit for us.
From my perspective, and the way I do it, upgrading sometimes is to solve certain technology levels that, let's say, our facility is struggling with. That's because it's the newest technology, so we need to invest in it. So yes, sometimes we find we're struggling to solve some of the challenges that are out there that we may be facing, and certainly any of the others are facing in their day-to-day challenges of building PCBs.
Beyond that, we need to look at the challenges that are coming; we must keep an eye to the future and understand the trends that are coming, whether that be finer lines and spaces, higher layer count, thicker panels, higher aspect ratios from a plating perspective, or subtractive or additive processes.
Las Marias: David, I enjoyed our conversation. Is there anything that we haven't discussed that you think we should be talking about?
Aldape: I would leave us with one thought that I left at the end of my presentation. A quote by Michio Kaku: “Science and technology are the engines of prosperity. One is free to ignore science and technology, but that will be at your own peril. If you don't master the latest in science and technology, your competitors will.” So that's a thought-provoking quote that we all need to think about, in my opinion, and take seriously. And if we embrace it from that perspective, then I think we all can be better off.
Las Marias: Thank you very much, David.
Aldape: Thank you!
Testimonial
"In a year when every marketing dollar mattered, I chose to keep I-Connect007 in our 2025 plan. Their commitment to high-quality, insightful content aligns with Koh Young’s values and helps readers navigate a changing industry. "
Brent Fischthal - Koh YoungSuggested Items
How Good Design Enables Sustainable PCBs
08/21/2025 | Gerry Partida, Summit InterconnectSustainability has become a key focus for PCB companies seeking to reduce waste, conserve energy, and optimize resources. While many discussions on sustainability center around materials or energy-efficient processes, PCB design is an often overlooked factor that lies at the heart of manufacturing. Good design practices, especially those based on established IPC standards, play a central role in enabling sustainable PCB production. By ensuring designs are manufacturable and reliable, engineers can significantly reduce the environmental impact of their products.
50% Copper Tariffs, 100% Chip Uncertainty, and a Truce
08/19/2025 | Andy Shaughnessy, I-Connect007If you’re like me, tariffs were not on your radar screen until a few months ago, but now political rhetoric has turned to presidential action. Tariffs are front-page news with major developments coming directly from the Oval Office. These are not typical times. President Donald Trump campaigned on tariff reform, and he’s now busy revamping America’s tariff policy.
Global PCB Connections: Understanding the General Fabrication Process—A Designer’s Hidden Advantage
08/14/2025 | Markus Voeltz -- Column: Global PCB ConnectionsDesigners don’t need to become fabricators, but understanding the basics of PCB fabrication can save you time, money, and frustration. The more you understand what’s happening on the shop floor, the better you’ll be able to prevent downstream issues. As you move into more advanced designs like HDI, flex circuits, stacked vias, and embedded components, this foundational knowledge becomes even more critical. Remember: the fabricator is your partner.
MKS’ Atotech to Participate in IPCA Electronics Expo 2025
08/11/2025 | AtotechMKS Inc., a global provider of enabling technologies that transform our world, announced that its strategic brands ESI® (laser systems) and Atotech® (process chemicals, equipment, software, and services) will showcase their latest range of leading manufacturing solutions for printed circuit board (PCB) and package substrate manufacturing at the upcoming 17th IPCA Show to be held at Pragati Maidan, New Delhi from August 21-23, 2025.
MKS Showcases Next-generation PCB Manufacturing Solutions at the Thailand Electronics Circuit Asia 2025
08/06/2025 | MKS Instruments, Inc.MKS Inc, a global provider of enabling technologies that transform our world, today announced its participation in Thailand Electronics Circuit Asia 2025 (THECA 2025), taking place August 20–22 at BITEC in Bangkok.