-
- News
- Books
Featured Books
- pcb007 Magazine
Latest Issues
Current IssueInventing the Future with SEL
Two years after launching its state-of-the-art PCB facility, SEL shares lessons in vision, execution, and innovation, plus insights from industry icons and technology leaders shaping the future of PCB fabrication.
Sales: From Pitch to PO
From the first cold call to finally receiving that first purchase order, the July PCB007 Magazine breaks down some critical parts of the sales stack. To up your sales game, read on!
The Hole Truth: Via Integrity in an HDI World
From the drilled hole to registration across multiple sequential lamination cycles, to the quality of your copper plating, via reliability in an HDI world is becoming an ever-greater challenge. This month we look at “The Hole Truth,” from creating the “perfect” via to how you can assure via quality and reliability, the first time, every time.
- Articles
- Columns
- Links
- Media kit
||| MENU - pcb007 Magazine
Unimicron Germany Rises from the Ashes with New Smart Factory
April 30, 2018 | Pete Starkey, I-Connect007 and Michael Weinhold, EIPCEstimated reading time: 9 minutes
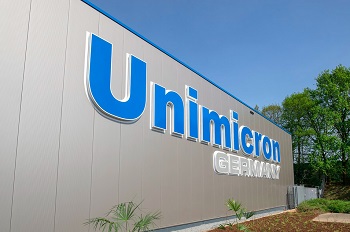
This is a review of the grand opening of Unimicron’s new smart factory in Geldern, Germany.
A fire in a PCB shop is an experience we all dread, but still it happens, and the consequences can be devastating. In the early hours of December 28, 2016, the innerlayer production plant at RUWEL International in Geldern, Germany, caught fire and the whole factory and its contents were destroyed.
Figure 1: Aerial photo of the burned-out factory. (Source: EIPC)
Thankfully, there were no casualties and because the chemical stores survived, there were no serious environmental consequences. However, early estimates of the cost of the damage ran into higher-double-digit millions of Euros. And to quote the words of CTO Rico Schlüter “...we have unfortunately not the time to mourn—we must tackle today's challenges and come back as an even stronger company."
Recognised as the oldest operating PCB producer in Europe, RUWEL International GmbH was founded in Geldern in 1945. Unimicron Group made a strategic investment in RUWEL in 2009, and in 2011 fully integrated the company into the group, developing it as the leader of their High Reliability Business Unit (HRBU). More recently, the operation has been re-named Unimicron Germany. The parent organisation, headquartered in Taiwan, is the global leader in the PCB industry, with an annual turnover of $2 billion, 14 Asian production facilities, and a workforce of over 20,000.
Meanwhile, in Geldern, the pressure was on to move fast to maintain continuity of supply to RUWEL’s customer base. Only a few hours after the fire, and in consultation with Unimicron, it was decided that a new innerlayer production facility should be built in Geldern, with the production needs supported with mass-lam from the Unimicron plant in Kunshan, China—already qualified and certified with the approvals required by RUWEL’s automotive market.
I have always been encouraged by the community spirit which exists in our industry, especially when misfortune strikes. On several occasions over many years of personal experience I have seen how suppliers, friends and even competitors rally round to offer practical help, and this was very much the case for RUWEL who were able to benefit from local resources to support small batch and quick-turn requirements in the interim period, all with the approval and cooperation of their customers.
In the meantime, the company was re-named Unimicron Germany.
So, with continuity of production secured, planning of the replacement factory went ahead and in August 2017 the City of Geldern gave Unimicron formal permission for the rebuilding work to commence. Orders were placed for equipment that would represent the state of the art both in technology and in smart factory automation.
It all became a reality on Saturday 21st April 2018, when together with suppliers, customers, the Unimicron workforce and the officers of the EIPC, I was one of 800 guests privileged to attend the opening ceremony and to have a guided tour of the new facility—a spectacular experience!
Although most visitors were being escorted in large groups around the factory with German-speaking guides, my EIPC colleagues and I had the benefit of a more exclusive, small-group walk-around in the company of CTO Rico Schlüter who had been instrumental in designing, installing and commissioning the whole set-up.
After congregating outside in hot sunshine, it was refreshing to feel the air conditioning as we entered the plant. First impression was white—white floor, white walls, white ceiling, fully-enclosed white equipment, lots of space, all the services out of sight, no clutter of racks or trolleys to be seen.
And we were greeted by a robot—an autonomous guided vehicle (AGV) carrying a sign welcoming us to Unimicron’s smart factory. It was yellow, as were its eight colleagues around the factory area, each robot AGV capable of performing any panel-transportation task in any area. No fear of getting run-over—these laser- and GPS-guided robots could identify humans and stop, even if someone suddenly stepped into their path, although they did tend to bleep rather impatiently if they had work to do and you happened to be standing in their way!
Figure 2: Welcoming robot AGV.
Automation was everywhere, with traceability to match; every panel in the factory had its own unique data-matrix ID. Whether the job was a quick-turn prototype or a series production batch, the required material was drawn from store by an automated picking system and transferred to an AGV, which transported it to the load station of one of three surface-preparation lines, from which it was fed by a six-axis robot onto the machine conveyor. The predominant panel size was 24” x 21” although 24” x 18” and 24” x 24” were alternative options.
Figure 3: Surface preparation line.
Figure 4: Rear of surface preparation line.
Figure 5: Six-axis robot loader.
Page 1 of 6
Testimonial
"The I-Connect007 team is outstanding—kind, responsive, and a true marketing partner. Their design team created fresh, eye-catching ads, and their editorial support polished our content to let our brand shine. Thank you all! "
Sweeney Ng - CEE PCBSuggested Items
How Good Design Enables Sustainable PCBs
08/21/2025 | Gerry Partida, Summit InterconnectSustainability has become a key focus for PCB companies seeking to reduce waste, conserve energy, and optimize resources. While many discussions on sustainability center around materials or energy-efficient processes, PCB design is an often overlooked factor that lies at the heart of manufacturing. Good design practices, especially those based on established IPC standards, play a central role in enabling sustainable PCB production. By ensuring designs are manufacturable and reliable, engineers can significantly reduce the environmental impact of their products.
50% Copper Tariffs, 100% Chip Uncertainty, and a Truce
08/19/2025 | Andy Shaughnessy, I-Connect007If you’re like me, tariffs were not on your radar screen until a few months ago, but now political rhetoric has turned to presidential action. Tariffs are front-page news with major developments coming directly from the Oval Office. These are not typical times. President Donald Trump campaigned on tariff reform, and he’s now busy revamping America’s tariff policy.
Global PCB Connections: Understanding the General Fabrication Process—A Designer’s Hidden Advantage
08/14/2025 | Markus Voeltz -- Column: Global PCB ConnectionsDesigners don’t need to become fabricators, but understanding the basics of PCB fabrication can save you time, money, and frustration. The more you understand what’s happening on the shop floor, the better you’ll be able to prevent downstream issues. As you move into more advanced designs like HDI, flex circuits, stacked vias, and embedded components, this foundational knowledge becomes even more critical. Remember: the fabricator is your partner.
MKS’ Atotech to Participate in IPCA Electronics Expo 2025
08/11/2025 | AtotechMKS Inc., a global provider of enabling technologies that transform our world, announced that its strategic brands ESI® (laser systems) and Atotech® (process chemicals, equipment, software, and services) will showcase their latest range of leading manufacturing solutions for printed circuit board (PCB) and package substrate manufacturing at the upcoming 17th IPCA Show to be held at Pragati Maidan, New Delhi from August 21-23, 2025.
MKS Showcases Next-generation PCB Manufacturing Solutions at the Thailand Electronics Circuit Asia 2025
08/06/2025 | MKS Instruments, Inc.MKS Inc, a global provider of enabling technologies that transform our world, today announced its participation in Thailand Electronics Circuit Asia 2025 (THECA 2025), taking place August 20–22 at BITEC in Bangkok.