-
-
News
News Highlights
- Books
Featured Books
- pcb007 Magazine
Latest Issues
Current IssueThe Hole Truth: Via Integrity in an HDI World
From the drilled hole to registration across multiple sequential lamination cycles, to the quality of your copper plating, via reliability in an HDI world is becoming an ever-greater challenge. This month we look at “The Hole Truth,” from creating the “perfect” via to how you can assure via quality and reliability, the first time, every time.
In Pursuit of Perfection: Defect Reduction
For bare PCB board fabrication, defect reduction is a critical aspect of a company's bottom line profitability. In this issue, we examine how imaging, etching, and plating processes can provide information and insight into reducing defects and increasing yields.
Voices of the Industry
We take the pulse of the PCB industry by sharing insights from leading fabricators and suppliers in this month's issue. We've gathered their thoughts on the new U.S. administration, spending, the war in Ukraine, and their most pressing needs. It’s an eye-opening and enlightening look behind the curtain.
- Articles
- Columns
- Links
- Media kit
||| MENU - pcb007 Magazine
ACE’s AccuWrap Simplifies Multiple Sequential Laminations with Blind Vias
May 29, 2018 | Andy ShaughnessyEstimated reading time: 5 minutes
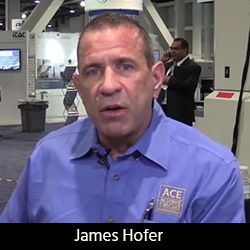
At DesignCon 2018, I spoke with James Hofer, general manager for Accurate Circuit Engineering, a quick-turn fabricator based in Santa Ana, California. James gave me a preview of AccuWrap, a new type of processing technology that lets designers reduce the amount of copper during sequential laminations while still meeting IPC specs, which should be of great interest to RF designers.
Andy Shaughnessy: Good to see you, James. Why don’t you just give us a quick rundown of the company?
James Hofer: Accurate Circuit Engineering has been a privately-owned company for the last 35 years. We’re family-owned, small, quick-turn, high-mix, high-tech, and low to mid-volume. We specialize in RF and microwave boards. We've got all the certifications. We're actually one of the few remaining small, privately held circuit board shops in Southern California, considering all the acquisitions that have been going on.
Shaughnessy: I understand you've got some really new cool technology to talk about.
Hofer: That's right. Over the last couple years, we've developed a trademarked process that allows us meet wrap requirements per IPC, while still maintaining low surface copper, which is important to our microwave and RF customers. We've labeled the technology AccuWrap, and its purpose is to be able to do multiple sequential laminations with blind vias while keeping the surface copper manageable.
The issue that we encounter is that nowadays, you do a lot of blind vias that might span one to two, then one to three, then one to five, maybe one to six on a 10-layer board. Then you've got through-holes that are filled. Each one of those blind vias and the through filled holes all require wrap. This is all before you actually get to your drilled holes, which also require wrap and plating.
With standard processing methodology, each one of those gets plated up for IPC-6012, for example, Class 3, and each one of those has to have a half mil of wrap. Typically, you'll start with a quarter or half ounce foil, but I just defined five different sets requiring wrap, that's an addition two and a half mils of copper that's going on top of your either ¼ ounce or .5 oz of base copper before you've even gotten to your through-hole plating. In an RF world, having that much copper on the surface, and we are talking about three mils, can be detrimental for your signals. So, ACE has been tasked with finding a way of meeting 6012 and 6018 specifications, yet still being able to build an RF board that engineers can model and work with.
So AccuWrap, in short, reduces the amount of surface copper that goes on the board, while still meeting the wrap requirements of the IPC specifications. It's taken a couple years for us to refine it, define it and of course trademark it. Actually, this is kind of a preview of coming attractions, because we won't be posting this news on our website for probably another 60 to 90 days. We're very excited about it, and it's going to allow us now to do RF and antenna boards that want to keep the copper down around 1.5 mils or 1 mil yet still meet all the wrap requirements.
I think this is really groundbreaking for the industry in standard methodology. We're very excited about it. I just thought I'd bring it out at this show and talk to you a little bit about it.
Shaughnessy: What sort of customers or final products would this appeal to?
Hofer: This is especially good for folks who are doing antennas. Antennas typically utilize a lot of blind vias, always utilize some sort of filled vias, they may also have some back drilling as well. So I'm thinking It's going to be fantastic for the antenna industry, and I think even some of our digital boards where we have stacked, sequential laminations that exceed nine laminations may benefit.
Now if I've got nine laminations, that's means I've got nine wrap requirements, not including the filled vias or the through-hole vias. Being able to reduce that copper and keep it closer to 1.5 or 2 mils is going to really make a difference for even your guys who are doing digital stuff with impedance because it's hard to have a five mil high trace and meet your impedance requirement, especially when most of your designers model that out at 1.5 mils or 2 mils.
So I think in that regard, in that market sector, our customers are going to see a real advantage.
Shaughnessy: That will really help the designers. So, you've obviously been working with IPC on this?
Hofer: Absolutely, as well as trademark attorneys all our process engineers and, of course, now it’s your turn. You're the marketing guys! You've got to let designers know that there is an answer. I think the issue is that we have a lot of PCB designers out there, and basically, when they model, they take the base copper that they get with a laminate and they assume that this is going to be the finished copper. A lot of RF designers model with what's known as base copper or foil weights and they don't realize how much copper can be added to the surface in standard manufacturing. I really am looking forward to getting the word out there that they can still meet the requirements of the specs and have copper that's manageable.
Shaughnessy: For designers, what are the biggest advantages of using AccuWrap?
Hofer: You can go with as many sequential laminations as you need to, without jeopardizing the amount of copper on your outer layers. A lot of designers get fearful that are aware of wrap that I can't do that because I can't have that much copper on the surface. The second thing I would let them know is that you can still do multiple sets of blind and filled vias while still being able to certify the board IPC.
Shaughnessy: That sounds like a pretty easy sell. Congratulations. It sounds like you're really taking care of a problem here.
Hofer: We've seen the problem and we found a solution. We provide solutions. We don't just provide circuit boards.
Shaughnessy: That's what people want.
Hofer: Yep. Thank you, Andy.
Shaughnessy: Thank you for speaking with us, James.
Suggested Items
The Evolution of Picosecond Laser Drilling
06/19/2025 | Marcy LaRont, PCB007 MagazineIs it hard to imagine a single laser pulse reduced not only from nanoseconds to picoseconds in its pulse duration, but even to femtoseconds? Well, buckle up because it seems we are there. In this interview, Dr. Stefan Rung, technical director of laser machines at Schmoll Maschinen GmbH, traces the technology trajectory of the laser drill from the CO2 laser to cutting-edge picosecond and hybrid laser drilling systems, highlighting the benefits and limitations of each method, and demonstrating how laser innovations are shaping the future of PCB fabrication.
Day 2: More Cutting-edge Insights at the EIPC Summer Conference
06/18/2025 | Pete Starkey, I-Connect007The European Institute for the PCB Community (EIPC) summer conference took place this year in Edinburgh, Scotland, June 3-4. This is the third of three articles on the conference. The other two cover Day 1’s sessions and the opening keynote speech. Below is a recap of the second day’s sessions.
Day 1: Cutting Edge Insights at the EIPC Summer Conference
06/17/2025 | Pete Starkey, I-Connect007The European Institute for the PCB Community (EIPC) Summer Conference took place this year in Edinburgh, Scotland, June 3-4. This is the second of three articles on the conference. The other two cover the keynote speeches and Day 2 of the technical conference. Below is a recap of the first day’s sessions.
Preventing Surface Prep Defects and Ensuring Reliability
06/10/2025 | Marcy LaRont, PCB007 MagazineIn printed circuit board (PCB) fabrication, surface preparation is a critical process that ensures strong adhesion, reliable plating, and long-term product performance. Without proper surface treatment, manufacturers may encounter defects such as delamination, poor solder mask adhesion, and plating failures. This article examines key surface preparation techniques, common defects resulting from improper processes, and real-world case studies that illustrate best practices.
RF PCB Design Tips and Tricks
05/08/2025 | Cherie Litson, EPTAC MIT CID/CID+There are many great books, videos, and information online about designing PCBs for RF circuits. A few of my favorite RF sources are Hans Rosenberg, Stephen Chavez, and Rick Hartley, but there are many more. These PCB design engineers have a very good perspective on what it takes to take an RF design from schematic concept to PCB layout.