-
- News
- Books
Featured Books
- pcb007 Magazine
Latest Issues
Current IssueInventing the Future with SEL
Two years after launching its state-of-the-art PCB facility, SEL shares lessons in vision, execution, and innovation, plus insights from industry icons and technology leaders shaping the future of PCB fabrication.
Sales: From Pitch to PO
From the first cold call to finally receiving that first purchase order, the July PCB007 Magazine breaks down some critical parts of the sales stack. To up your sales game, read on!
The Hole Truth: Via Integrity in an HDI World
From the drilled hole to registration across multiple sequential lamination cycles, to the quality of your copper plating, via reliability in an HDI world is becoming an ever-greater challenge. This month we look at “The Hole Truth,” from creating the “perfect” via to how you can assure via quality and reliability, the first time, every time.
- Articles
- Columns
- Links
- Media kit
||| MENU - pcb007 Magazine
Robert Art on the Importance of Thermal Management
January 7, 2019 | Pete Starkey, I-Connect007Estimated reading time: 12 minutes
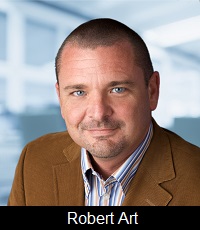
Robert Art, global account manager for IMS materials at Ventec International Group, discusses future market requirements for thermal management materials, the need for a better understanding of the concept of thermal impedance, and an initiative to propose a consistent industry-standard method for measuring thermal conductivity while at electronica 2018.
Pete Starkey: Robert, it's great to meet you. Thank you for taking the time to talk with me.
Robert Art: Thank you.
Starkey: You're an expert in materials for thermal management. We know that over the last several years, Ventec has established a leading position in IMS materials, and you have a good forward vision of the market. Can you tell us what the market is expecting of you now, and in which direction you are going to meet future market needs and expectations?
Art: The market is looking for what it has always looked for—better thermal performance. In every sales meeting and discussion with customers and at trade show events, the engineering community is always looking for better thermal performance. Our VT-4B7 material is a star performer amongst our market-leading VT-4B family of high-performance IMS materials. We continue to push the envelope when it comes to developing stronger, more reliable robust dielectrics that can be thinner to reduce thermal impedance and resistance values.
Starkey: Can you give me a couple of points of reference? What sort of thermal conductivities are achievable with these materials, and when you talk about "thin," what's a point of reference for thinness?
Art: With respect to thermal conductivities, the current Ventec product line-up ranges anywhere from two watts per meter-Kelvin all the way up to roughly 10 watts per meter-Kelvin. From a thickness standpoint, we have one new product out on the market called VT-4B5SP that is available in a thickness of 40 microns. That's an incredibly thin dielectric that still has a very good voltage withstand and excellent thermal conductivity.
Starkey: Is that a reinforced dielectric or a filled-resin dielectric?
Art: It's a filled-resin dielectric with no fiberglass or other carrier reinforcement.
Starkey: And you can get that down as thin as 40 microns?
Art: Correct.
Starkey: We continue to try very hard to explain to people that the most significant consideration is the concept of thermal impedance rather than just thermal conductivity. Even if you have high thermal conductivity, if the heat has a long path to get through, there’s going to be resistance to the flow. The shorter you can get that path, the better, and it's really important to explain this.
Art: Exactly. We need to continue to educate and help our customer base. Take LEDs, for example; even though IMS substrates have become very commonly used in LED applications, we still come across engineers who focus solely on thermal conductivity. Thermal conductivity is a great characteristic to use for benchmarking materials, but it is not the only attribute that designers should pay attention to. They need to consider dielectric thickness and the overall thermal resistance. That is truly what matters—the resistance to heat flow. As you mentioned, you can have a product at 10 watts per meter-Kelvin, but if it's in a 150- or 200-micron dielectric, then the thermal resistance will be high, and the overall path of heat may not be as good as it could be through a thinner dielectric with a lower thermal conductivity.
Starkey: To try to achieve a dielectric thickness reliably at 40 microns must present a lot of challenges in the manufacturing process. How do you overcome those challenges?
Art: That's a really good question. Ventec has without a doubt the best R&D staff community in the IMS world in my opinion. A lot of time and care is taken to perfect a manufacturing process and speeds of conveyors and lamination cycles to be able to consistently reproduce a dielectric at 40 microns with very high yield and efficiency.
Starkey: The other consideration is that on the one hand, you want to conduct heat, but on the other, you want to maintain electrical insulation.
Art: Yes. Although there are products on the market that are slightly thinner than 40 microns, the challenge is holding to a tighter tolerance. So, when you commit to a thin dielectric, the customer base wants that to be the same dielectric thickness with each and every shipment. A 40-micron dielectric with a ±40-micron thickness tolerance is really of no value. You're absolutely right; it's a hard line between thermal performance, electrical isolation, and peel strength. Trying to juggle all three of those attributes and hold to something that's less than 50 microns is quite a challenge.
Starkey: Where is the main area of application for these high-performance materials?
Art: The primary application today for these extremely thin dielectrics is in LED lighting, which is a high performer.
Starkey: Is this LED lighting for automotive, municipal, industrial, or domestic?
Art: The answer really is all of the above. The hottest market today is automotive lighting for these types of dielectrics, but we also see them in parking lot lights, parking ramp lights, and street lights. Most of those designs today use a number of boards—it's not just one dedicated board; it might be four, six, or eight different boards in a lighting unit. The desire by the engineering community is to get all of those LEDs and connectors onto one board, so it's much more robust and reliable. Each time you add an additional board into a module, you create more risk as far as efficiency and failure. These thin dielectrics allow customers to go to a one-board system, and that represents a great savings in total system cost.
Starkey: You've progressively developed to a very high level of specification, and have a vision of what the market is going to call for in the future. Is there a realistic limit to what you can achieve? Is there any benefit in pushing it any further than that, or do you look for alternative technologies if you have more heat than this sort of material can handle?
Art: Good question! Do we push the envelope? We have to! To stay in the mindset of the customer as a world leader or a supplier to look for the next best-generation product, we have to push the envelope. We consider the characteristics of IMS that are not only focused on the dielectric. There are attributes with the total material stackup that can be altered, changed, or adjusted that produce even better results. There's a whole concern in the industry with IMS because generally speaking, the base plate in an IMS stackup is aluminum. That has wildly different CTE values than the copper foil that becomes the circuit trace. Solder joint reliability is a big concern today for many customers, and not exclusive to automotive; we see it in other markets too.
If you look at our roadmaps, some of the product offerings we're pursuing not only improve the thermal performance or peel strength but also improve the modulus of the dielectric to make it more conducive to providing a really solid solder joint. Solder joint fatigue is a big issue in our marketplace today, and that's an area of focus for our future development.
Page 1 of 2
Testimonial
"Our marketing partnership with I-Connect007 is already delivering. Just a day after our press release went live, we received a direct inquiry about our updated products!"
Rachael Temple - AlltematedSuggested Items
Indium Corporation Promotes Two Leaders in EMEA (Europe, Middle East, and Africa) Markets
08/05/2025 | Indium CorporationWith its commitment to innovation and growth through employee development, Indium Corporation today announced the promotions of Andy Seager to Associate Director, Continental Sales (EMEA), and Karthik Vijay to Senior Technical Manager (EMEA). These advancements reflect their contributions to the company’s continued innovative efforts with customers across Europe, the Middle East, and Africa (EMEA).
MacDermid Alpha Electronics Solutions Unveils Unified Global Website to Deepen Customer, Talent, and Stakeholder Engagement
07/31/2025 | MacDermid Alpha Electronics SolutionsMacDermid Alpha Electronics Solutions, the electronics business of Elements Solutions Inc, today launched macdermidalpha.com - a unified global website built to deepen digital engagement. The launch marks a significant milestone in the business’ ongoing commitment to delivering more meaningful, interactive, and impactful experiences for its customers, talent, and stakeholders worldwide.
KOKI to Showcase Analytical Services and New HF1200 Solder Paste at SMTA Guadalajara 2025
07/31/2025 | KOKIKOKI, a global leader in advanced soldering materials and process optimization services, will exhibit at the SMTA Guadalajara Expo & Tech Forum, taking place September 17 & 18, 2025 at Expo Guadalajara, Salón Jalisco Halls D & E in Guadalajara, Mexico.
Weller Tools Supports Future Talent with Exclusive Donation to SMTA Michigan Student Soldering Competition
07/23/2025 | Weller ToolsWeller Tools, the industry leader in hand soldering solutions, is proud to announce its support of the upcoming SMTA Michigan Expo & Tech Forum by donating a limited-edition 80th Anniversary Black Soldering Set to the event’s student soldering competition.
Koh Young Appoints Tom Hattori as President of Koh Young Japan
07/21/2025 | Koh YoungKoh Young Technology, the global leader in True 3D measurement-based inspection solutions, announced the appointment of Tom Hattori as President of Koh Young Japan (JKY).