-
- News
- Books
Featured Books
- pcb007 Magazine
Latest Issues
Current IssueInventing the Future with SEL
Two years after launching its state-of-the-art PCB facility, SEL shares lessons in vision, execution, and innovation, plus insights from industry icons and technology leaders shaping the future of PCB fabrication.
Sales: From Pitch to PO
From the first cold call to finally receiving that first purchase order, the July PCB007 Magazine breaks down some critical parts of the sales stack. To up your sales game, read on!
The Hole Truth: Via Integrity in an HDI World
From the drilled hole to registration across multiple sequential lamination cycles, to the quality of your copper plating, via reliability in an HDI world is becoming an ever-greater challenge. This month we look at “The Hole Truth,” from creating the “perfect” via to how you can assure via quality and reliability, the first time, every time.
- Articles
- Columns
- Links
- Media kit
||| MENU - pcb007 Magazine
Estimated reading time: 4 minutes
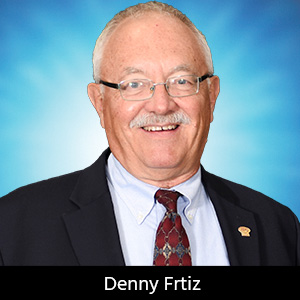
Defense Speak Interpreted: PERM—Pb-free Electronics Risk Management
In this column, we explore PERM—the Pb-free Electronics Risk Management Consortium. No, the group members do not all have curly hair! The name was chosen around 2008 by a group of engineers from aerospace, defense, and harsh environment (ADHE) organizations. Two points: first, the team used the chemical designation “Pb” for the element “lead” to differentiate the effort from the “leads” on electronic components mounted on boards. Second, the word “risk” was intentionally emphasized because of the different solder performance properties between Pb-free formulations in commercial electronics and the traditional tin-lead eutectic solder still used by many ADHE companies. Also, the switch to pure tin component finishes creates the possibility for tin whiskers.
The origins of PERM date well before the 2006 implementation of RoHS to a defense-directed study group—the Executive Lead-free Integrated Process Team (ELF-IPT). The Aerospace Industries Association (AIA) administered this loosely organized ELF-IPT body of 500 individuals into teams. There were two principal activities: first, research into and member education about the differences between the two solder families; and the second activity was the promulgation of standards concerning the continued use of Pb solder with the possible conversion to Pb-free. The standards were issued through the former Government Electronics Industry Association (GEIA) where AIA was responsible for many GEIA standards besides electronics.
In 2012, AIA passed the research, communications, and advocacy activities of PERM to IPC-Association Connecting Electronics Industries while SAE International adopted the PERM standards. PERM activities today are best summed up in Figure 1.
Figure 1: PERM Consortium focus.
A major continued focus of PERM has been detailed engineering knowledge to convert from Pb-containing eutectic solder to Pb-free. In 2009, PERM supported an effort funded by the U.S. Department of Defense (DoD) to enumerate the ADHE industry knowledge gaps and estimate the cost to solve these issues. The total estimate at that time was about $110 million over three intense years of project work. Conveniently, the total effort was broken up into over 100 “bite-size chunks” varying from $100,000 to $5 million. Unfortunately, with the DoD budget cuts from 2009– 2012, this “Manhattan Project” for solder conversion was never funded, even in part. However, individual companies and universities continued smaller scale work on these bite-size chunks.
After taking over the public face of PERM, IPC completed a “Manhattan re-baseline” in 2014 and estimated that about $40 million remained to complete the knowledge base for the conversion to Pb-free. Again, this did not receive funding, although aerospace companies were solicited, besides Defense.
Currently, the IPC Government Relations group has resurrected the Manhattan Project funding issue and proposed to request $15 million in fiscal year (FY) 2020 of congressionally-directed funding to jumpstart Manhattan Project work including an initial formal project review immediately. IPC is currently soliciting interested parties to participate in conference calls and to come to Capitol Hill early in 2019 to get Manhattan funding into the 2020 Federal budget.
In other Pb-free activities, PERM members worked together to issue IPC/PERM-2901—"Pb-free Design and Assembly Implementation Guide”—in February 2018. This guide for the present eutectic solder users covers:
- Pb-free solders and solder joints
- Tin whiskers
- Printed board defects
- Product qualification
- Manufacturing processes
- Supply chain control
- Obsolescence management
- COTS assembly, selection, and use
- Configuration management
The IPC/PERM-2901 “Pb-free Design and Assembly Implementation Guide” is available for purchase from IPC.
To get a better understanding of current ADHE attitudes toward Pb-free, PERM worked with IPC staff to issue and tabulate “IPC/PERM Pb-free Industry Needs Survey—April 2018” with 76 ADHE respondents. Some striking conclusions:
- 60% of respondents say their company has a Pb-free control plan
- 30% of companies train employees on Pb-free solder risks
- 30% have delivered some Pb-free assemblies already, but almost 50% do not anticipate lead-free delivery for at least 10 years
- 50% think they have Pb-free COTS (commercially off the shelf) subassemblies in their products
- 55% think they will have to deliver legacy Pb-based solder parts for at least 20 more years to keep existing defense electronics working
- Almost 40% have seen tin whiskers on some part in their assemblies
PERM also shares knowledge of industry tin whisker efforts—first, the nearly completed “IPC-TR-587 Conformal Coating Material and Application ‘State of the Industry’ Assessment Report,” and second, the “Tin Whisker Mitigation by SMT Reflow/Results of an Industry Round Robin” spearheaded by Dave Pinsky of Raytheon. In this study, IPC-PERM-WP-022, the coverage of pure-tin component leads by solder—Pb-free or especially eutectic—mitigates the tin-whisker formation risk on the component lead.
To better educate members, PERM is always looking for parallel industry activity. Meetings have been held in conjunction with such subscription consortia as AREA at SUNY Binghamton and CAVE3 at Auburn University. Progress reports to PERM have been given by the NASA/DoD Pb-free Solders Round 3 Testing Group, which has recently also been transferred to IPC supervision under John Perry.
One interesting sister industry is automotive. Thermal cycle testing of engine and brake controllers is now proposed for -40°C to +150°C—an even wider thermal cycle testing than the military specification for defense electronics, which is -55°C to +125°C.
While the general public thinks that all electronics are now produced with Pb-free solders, the members of the PERM Council are busy working to ensure that the harsh environment advantages of Pb-containing solders are not lost with the eventual conversion to Pb-free.
More Columns from Defense Speak Interpreted
Defense Speak Interpreted: If CHIPS Cuts Back, What Happens to Electronics Packaging Funds?Defense Speak Interpreted: JADC2—Why It’s More Relevant Than Ever in Drone Warfare
Defense Speak Interpreted: Is DARPA Still Around After CHIPS?
Defense Speak Interpreted: Is There Still a CHIPS Act?
Defense Speak Interpreted: Update on the Continuing Resolution and Budget Process for Defense
Defense Speak Interpreted: It’s Time for a ‘Defense-Speak’ Update
Defense Speak Interpreted: SWaPing Nanosatellites for Defense Systems
Defense Speak Interpreted: Who Won the Project Convergence War Game—Evil Chaos or JADC2?