-
- News
- Books
Featured Books
- pcb007 Magazine
Latest Issues
Current IssueInventing the Future with SEL
Two years after launching its state-of-the-art PCB facility, SEL shares lessons in vision, execution, and innovation, plus insights from industry icons and technology leaders shaping the future of PCB fabrication.
Sales: From Pitch to PO
From the first cold call to finally receiving that first purchase order, the July PCB007 Magazine breaks down some critical parts of the sales stack. To up your sales game, read on!
The Hole Truth: Via Integrity in an HDI World
From the drilled hole to registration across multiple sequential lamination cycles, to the quality of your copper plating, via reliability in an HDI world is becoming an ever-greater challenge. This month we look at “The Hole Truth,” from creating the “perfect” via to how you can assure via quality and reliability, the first time, every time.
- Articles
- Columns
- Links
- Media kit
||| MENU - pcb007 Magazine
FlexFactor Program Informs, Inspires, Attracts, and Recruits Talent
May 24, 2019 | Nolan Johnson and Barry Matties, I-Connect007Estimated reading time: 5 minutes
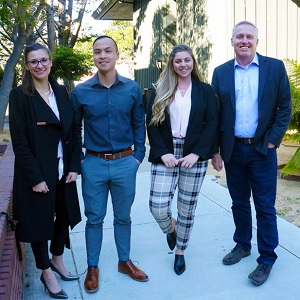
Barry Matties and Nolan Johnson speak with Brynt Parmeter, Emily McGrath, Clarence Chi, and Mikayla Ridi about the NextFlex program FlexFactor. This initiative aims to help high school and college students see potential futures in the advanced manufacturing sector and combat common misperceptions young people might have about modern-day manufacturing.
Nolan Johnson: Brynt, tell us about your role at NextFlex and what the company does.
Brynt Parmeter: I am the director of workforce development, education, and training for Next-Flex. We are a 501(c)(6) public-private partnership with nearly 100 members across the U.S., and we’ve been in existence for three and a half years. Our goal is to advance the technology associated with the manufacturing of flexible hybrid electronics in conjunction with our members. We operate under a cooperative agreement with the Department of Defense, and we are working toward becoming a self-sustaining organization. In addition to the 501(c)(6), we run our workforce development and learning programs under a 501(c)(3) nonprofit and our design and manufacturing services under a C corporation to include fabrication operations within a 20,000-square-foot cleanroom facility at our headquarters in San Jose, California.
Johnson: We could do an entire interview just on NextFlex, but today, could you talk about the vision of the FlexFactor program?
Parmeter: Since our start, we have focused on enabling the creation of the talent needed by our industry partners over time. We are very much looking at the problem from the demand side to identify and quantify the knowledge and attributes needed to tackle what is commonly known as the “skills gap” across the advanced manufacturing and technology sector. We don’t have enough young people aware of the sector or the pathways that will lead them to become competitive hires. We have a gender imbalance and need to figure out how to reach more women to join this sector as well as non-traditional populations.
We’ve have put a lot of energy into tackling this problem and are seeing some impressive results. Our flagship program is called Flex-Factor, and it’s intended to do three things. First, the program aims to provide first-hand experiences that allow the next generation to see what a career in advanced manufacturing looks like. They learn what it is like to work in the field.
Second, it helps engage and familiarize students with the education pathways that lead into the sector and provide the skills and competencies necessary to become the competitive hires that our members, and those they represent, need in their future workforce when Industry 4.0 becomes a reality. Finally, as a project-based learning activity, FlexFactor gives participants the motivation and sense of purpose to want to take that journey and pursue the relevant education pathways to become competitive hires because they’ve become informed, inspired, attracted, and recruited into the sector through this immersive experience.
Barry Matties: What is the primary age group in the FlexFactor program?
Parmeter: We started with high school students in grades 9–12 and then we expanded the program to include middle school and elementary school students. We’re also launching a program segment for transitioning service members, veterans, and their spouses and dependent children in the school systems around military installations. We’ll start to see the first pilots of these cohorts happen across the country in late 2019 and early 2020.
Matties: How responsive are the schools to this program?
Parmeter: They are very responsive because what is unique about the program is its ability to meet the needs of a range of stakeholders. Companies engage with the program as a strategic talent acquisition activity. Institutions of higher education use it to attract students into the pathways needed by various industries so they can fill seats in classes aligned to the coursework and relevant material.
Finally, high schools and middle schools have a vested interest because they need to engage their students with real-world experiences in both higher education and multiple industries. In the words of one high school principal, “Schools and teachers need help understanding the world they’re preparing their kids for rather than remaining insulated in purely theoretical settings.” That’s a large part of what this program does.
Matties: That might be the toughest challenge right there.
Parmeter: It’s very difficult. We went through a significant learning curve and a lot of trial and error in the early stages of the program. This is a good bridge for Emily to discuss the strategy, including what we’ve learned and how the program has evolved into what it is today.
Emily McGrath: The program is intended to unite all stakeholders across a geographically aligned ecosystem who need to be engaged for effective workforce development. But those aren’t players who traditionally communicate with each other. We find that high schools are talking to higher education to some extent, but they aren’t talking to the industry. And the industry doesn’t often engage with higher education outside of specific programs.
What we had to do was figure out coordination steps that allowed these groups to interact smoothly on a regular basis. The program acts as a “Rosetta Stone” of sorts and speaks three different “languages.” The key to the success of the program are the project managers, such as Clarence and Mikayla. They need to be able to speak all three languages and ensure that all three stakeholders can communicate with one another about the challenges they have in common. FlexFactor’s coordination process is what allows the program to unfold smoothly and achieve the desired outcomes.
Matties: What is the greatest challenge?
Clarence Chi: Industry participation is one of the most critical aspects of the program. Our ability to directly engage students with advanced technologies and professional mentors is transformative, and you see their faces light up after they see how advanced technologies are changing the world around us.
Johnson: For example, a U-2 spy plane just took off and is flying right above us.
Parmeter: That plane is a perfect example because we work with a range of industry partners, including Boeing, Lockheed Martin, and others. FlexFactor is designed to get students interested not just in the technology of flexible electronics but also in the advanced manufacturing sector in general. Many students don’t realize that amazing products—such as the U-2 that just flew over, medical devices that are helping to save our loved ones, or automotive technologies—are all products from the advanced manufacturing industry.
Chi: To expand on that idea, the program casts a wide net because it works with existing classes—it’s not something students self-select into. The program’s touchpoints were designed in a way that allows it to work with any subject—English language development, AP biology, environmental science, mathematics, history, robotics, etc. What all the students have in common is their reaction to seeing modern manufacturing in action. Touring advanced facilities gets them really excited about what’s ahead for them in the future and what they can actually do, and they picture themselves working in these environments.
To read the full article, which appeared in the April 2019 issue of Flex007 Magazine, click here.
Testimonial
"The I-Connect007 team is outstanding—kind, responsive, and a true marketing partner. Their design team created fresh, eye-catching ads, and their editorial support polished our content to let our brand shine. Thank you all! "
Sweeney Ng - CEE PCBSuggested Items
VVDN Expands Manufacturing Footprint into the UAE to Meet Global Demand
08/20/2025 | PRNewswireVVDN Technologies, a global provider of software, product engineering and electronics manufacturing services & solutions, today announced it is setting up a new manufacturing facility in the UAE as part of its global expansion strategy.
Haylo Labs Acquires Plessey Semiconductors
08/20/2025 | Haylo LabsHaylo Labs has acquired Plessey Semiconductors, the UK’s leading innovator in microLED display technology.
Kimball Electronics Veterans ERG Members Proudly Participate in the 5th Annual Honor and Remember Run
08/20/2025 | Kimball ElectronicsVeterans and Military Service Advocacy (VMSA) Employee Resource Group (ERG) members Michael Mosher (Database Administration Engineer), Michael Stone (Test Technician Team Lead), and Joshua Belcher (Application Development Manager) took part in the 5th Annual Honor & Remember Run, a meaningful event dedicated to honoring fallen service members. The race featured a powerful memorial wall constructed from dog tags.
Meet Incap UK at the Electronic Component Show 2025
08/20/2025 | IncapIncap UK is pleased to be exhibiting at the Electronic Component Show 2025. This one-day event will take place on 18 September at the Kassam Stadium in Oxford, bringing together design engineers, purchasing professionals, manufacturers, distributors, and service providers to discover new products, solutions, and contacts. You will find us at stand 52.
Hon Hai Rotating CEO Yang Qiujin Wins 2025 Golden Yang Award for Women’s Power in Technology
08/20/2025 | Hon Hai Precision Industry Co., Ltd.Amid the global rise of "female-powered technology," Yang Qiujin, Rotating CEO of Hon Hai Precision Industry Co., Ltd. (TWSE: 2317), the world's largest platform solutions provider, has been awarded the "2025 Golden Yang Award - Female-Powered Technology" by the China Software Association/China Software Industry Association.