Lasers Enable Engineers to Weld Ceramics, No Furnace Required
August 26, 2019 | UC San DiegoEstimated reading time: 2 minutes
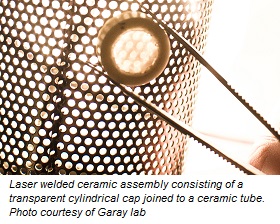
Smartphones that don’t scratch or shatter. Metal-free pacemakers. Electronics for space and other harsh environments. These could all be made possible thanks to a new ceramic welding technology developed by a team of engineers led by the University of California San Diego.
The process uses an ultrafast pulsed laser to melt ceramic materials along the interface and fuse them together. It works in ambient conditions and uses less than 50 watts of laser power, making it more practical than current ceramic welding methods that require heating the parts in a furnace.
Ceramics have been fundamentally challenging to weld together because they need extremely high temperatures to melt, exposing them to extreme temperature gradients that cause cracking, explained senior author Javier E. Garay, a professor of mechanical engineering and materials science and engineering at UC San Diego, who led the work in collaboration with UC Riverside professor and chair of mechanical engineering Guillermo Aguilar. Ceramic materials are of great interest because they are biocompatible, extremely hard and shatter resistant, making them ideal for biomedical implants and protective casings for electronics. However, current ceramic welding procedures are not conducive to making such devices.
“Right now there is no way to encase or seal electronic components inside ceramics because you would have to put the entire assembly in a furnace, which would end up burning the electronics,” Garay said.
Garay, Aguilar and colleagues’ solution was to aim a series of short laser pulses along the interface between two ceramic parts so that heat builds up only at the interface and causes localized melting. They call their method ultrafast pulsed laser welding.
To make it work, the researchers had to optimize two aspects: the laser parameters (exposure time, number of laser pulses, and duration of pulses) and the transparency of the ceramic material. With the right combination, the laser energy couples strongly to the ceramic, allowing welds to be made using low laser power (less than 50 watts) at room temperature. “The sweet spot of ultrafast pulses was two picoseconds at the high repetition rate of one megahertz, along with a moderate total number of pulses. This maximized the melt diameter, minimized material ablation, and timed cooling just right for the best weld possible,” Aguilar said.
“By focusing the energy right where we want it, we avoid setting up temperature gradients throughout the ceramic, so we can encase temperature-sensitive materials without damaging them,” Garay said.
As a proof of concept, the researchers welded a transparent cylindrical cap to the inside of a ceramic tube. Tests showed that the welds are strong enough to hold vacuum.
“The vacuum tests we used on our welds are the same tests that are used in industry to validate seals on electronic and optoelectronic devices,” said first author Elias Penilla, who worked on the project as a postdoctoral researcher in Garay’s research group at UC San Diego.
The process has so far only been used to weld small ceramic parts that are less than two centimeters in size. Future plans will involve optimizing the method for larger scales, as well as for different types of materials and geometries.
Suggested Items
The Pulse Design: Constraints for the Next Generation
07/16/2025 | Martyn Gaudion -- Column: The PulseIn Europe, where engineering careers were once seen as unpopular and lacking street credibility, we have been witnessing a turnaround in the past few years. The industry is now welcoming a new cohort of designers and engineers as people are showing a newfound interest in the profession.
Copper Price Surge Raises Alarms for Electronics
07/15/2025 | Global Electronics Association Advocacy and Government Relations TeamThe copper market is experiencing major turbulence in the wake of U.S. President Donald Trump’s announcement of a 50% tariff on imported copper effective Aug. 1. Recent news reports, including from the New York Times, sent U.S. copper futures soaring to record highs, climbing nearly 13% in a single day as manufacturers braced for supply shocks and surging costs.
Symposium Review: Qnity, DuPont, and Insulectro Forge Ahead with Advanced Materials
07/02/2025 | Barb Hockaday, I-Connect007In a dynamic and informative Innovation Symposium hosted live and on Zoom on June 25, 2025, representatives from Qnity (formerly DuPont Electronics), DuPont, and Insulectro discussed the evolving landscape of flexible circuit materials. From strategic corporate changes to cutting-edge polymer films, the session offered deep insight into design challenges, reliability, and next-gen solutions shaping the electronics industry.
Indium Corporation Expert to Present on Automotive and Industrial Solder Bonding Solutions at Global Electronics Association Workshop
06/26/2025 | IndiumIndium Corporation Principal Engineer, Advanced Materials, Andy Mackie, Ph.D., MSc, will deliver a technical presentation on innovative solder bonding solutions for automotive and industrial applications at the Global Electronics A
Gorilla Circuits Elevates PCB Precision with Schmoll’s Optiflex II Alignment System
06/23/2025 | Schmoll MaschinenGorilla Circuits, a leading PCB manufacturer based in Silicon Valley, has enhanced its production capabilities with the addition of Schmoll Maschinen’s Optiflex II Post-Etch Punch system—bringing a new level of precision to multilayer board fabrication.