-
- News
- Books
Featured Books
- pcb007 Magazine
Latest Issues
Current IssueInventing the Future with SEL
Two years after launching its state-of-the-art PCB facility, SEL shares lessons in vision, execution, and innovation, plus insights from industry icons and technology leaders shaping the future of PCB fabrication.
Sales: From Pitch to PO
From the first cold call to finally receiving that first purchase order, the July PCB007 Magazine breaks down some critical parts of the sales stack. To up your sales game, read on!
The Hole Truth: Via Integrity in an HDI World
From the drilled hole to registration across multiple sequential lamination cycles, to the quality of your copper plating, via reliability in an HDI world is becoming an ever-greater challenge. This month we look at “The Hole Truth,” from creating the “perfect” via to how you can assure via quality and reliability, the first time, every time.
- Articles
- Columns
- Links
- Media kit
||| MENU - pcb007 Magazine
Standards: Why We Have Them and Live by Them
October 7, 2019 | Alifiya Arastu, Jeff Beauchamp, Harry Kennedy, and Ruben Contreras, NCAB GROUPEstimated reading time: 4 minutes
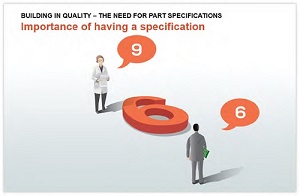
Have you ever designed a board but received feedback that it couldn’t be manufactured unless changes were made? Or maybe you’ve designed a complex board and sent it to the factory only to find out that the manufacturer didn’t build the board to your expectations? PCBs are becoming more complex, factory options are growing, and expectations for product life cycles are becoming longer.
Why Do We Need Standards?
As a designer, you now have to think about more than just the software used for design. To ensure that you have a robust design, you must understand how to design for manufacturability (DFM), design for the environment (DFE), design for reliability (DFR), design for test (DFT), etc. Considering all of this means that designers also have to be aware of the expectations and, in some cases, the correct terminology necessary to make this happen.
Figure 1: Without proper specification of a standard, there may be various interpretations.
The Institute of Printed Circuits (IPC) was founded in 1957 to develop standards for the fledgling PCB industry. Many years later (somewhere in the ‘90s) the name was changed to IPC–Association Connecting Electronics Industries to better reflect the expanded membership of the assembly folks and the need for standards for that end. Through the use of IPC standards, board designers can design robust PCBs that achieve the necessary requirements and minimize their time to market and have confidence in a reliable board when the end product is used in the field.
But is the use of standards really that important? Absolutely. Consider the impact of producing PCBs without defined standards (Figure 1). For example:
• We would not always receive a product that meets our expectations
• We would experience the risk of various interpretations of the same aspect
• We would not be able to secure the correct quality level
• We would not be able to compare “like-for-like” products or factories
• A guaranteed time to market would be based on chance rather than good factory selection and good design
Now that we can all agree that we need standards, are IPC standards effective? Yes! Through the implementation of IPC standards, the designer, manufacturer, and end customer see some of the benefits in Figure 2.
Figure 2: Benefits of users who implement IPC standards. (Source: TechValidate survey of IPC users, January 2018).
One of the most important things to notice is that using IPC standards as the minimum benchmark helps save the designer and manufacturer time before the product is built, during the manufacturing process, and after the final product is assembled, which results in saving money. There are multiple documents within IPC standards, and when used together, these documents should lead both manufacturer and customer to consistent terms of quality and acceptability. These documents also allow the customer and manufacturer to work together to set the criteria for acceptance of products that use newer technologies.
If you’re reading this and wondering how to start understanding standards and acceptability, there are many resources to help you. IPC’s website can help you learn more about the organization and how to become a member. Also, engineers at NCAB Group can help you to learn which IPC standards you should consider depending on your end application. We have certified IPC Trainers to teach your engineers about the acceptability of printed boards, and you can work with NCAB to produce your next PCB. Based on the 120+ million PCBs we ship annually, we’ve identified multiple steps in our PCB production process where we go beyond IPC specifications.
Risk/Awareness
When we look at what can happen from failing to require, reference, or follow specifications, there are a few considerations. The material produced can suffer from poor reliability. The cost to produce the PCB can be higher than needed, or subsequent builds of the same design can be inconsistent. It is critical to reference relevant industry specifications such as those released by IPC. Designs must contain a complete and concise specification that does not allow for interpretation as well as an adequate baseline to make sure that both the customer and supplier are on the same page.
A common example we see is a requirement for copper weights not referencing IPC minimums as detailed in the IPC-6012 and IPC-600 specifications. For instance, a fabrication drawing for a six-layer design has copper requirements of 2 oz. for all layers. No additional information for copper thicknesses is detailed or external specification referenced. This fabrication data goes to the manufacturer to be built, and some of the delivered PCBs show failures post-assembly. During root-cause analysis of the failures, it is noticed there is variance in the copper thicknesses delivered. This could potentially be caused by failure to reference the IPC copper thickness chart for internal and external conductor thickness in the fabrication data, allowing your manufacturer to interpret the requirement. Theoretically, this could result in external copper thickness ranging from 47.9 μm to 78.7 μm, depending on what the fabrication house considers as 2 oz. finished copper.
To read the full article, which appeared in the September 2019 issue of PCB007 Magazine, click here.
Testimonial
"The I-Connect007 team is outstanding—kind, responsive, and a true marketing partner. Their design team created fresh, eye-catching ads, and their editorial support polished our content to let our brand shine. Thank you all! "
Sweeney Ng - CEE PCBSuggested Items
How Good Design Enables Sustainable PCBs
08/21/2025 | Gerry Partida, Summit InterconnectSustainability has become a key focus for PCB companies seeking to reduce waste, conserve energy, and optimize resources. While many discussions on sustainability center around materials or energy-efficient processes, PCB design is an often overlooked factor that lies at the heart of manufacturing. Good design practices, especially those based on established IPC standards, play a central role in enabling sustainable PCB production. By ensuring designs are manufacturable and reliable, engineers can significantly reduce the environmental impact of their products.
50% Copper Tariffs, 100% Chip Uncertainty, and a Truce
08/19/2025 | Andy Shaughnessy, I-Connect007If you’re like me, tariffs were not on your radar screen until a few months ago, but now political rhetoric has turned to presidential action. Tariffs are front-page news with major developments coming directly from the Oval Office. These are not typical times. President Donald Trump campaigned on tariff reform, and he’s now busy revamping America’s tariff policy.
Global PCB Connections: Understanding the General Fabrication Process—A Designer’s Hidden Advantage
08/14/2025 | Markus Voeltz -- Column: Global PCB ConnectionsDesigners don’t need to become fabricators, but understanding the basics of PCB fabrication can save you time, money, and frustration. The more you understand what’s happening on the shop floor, the better you’ll be able to prevent downstream issues. As you move into more advanced designs like HDI, flex circuits, stacked vias, and embedded components, this foundational knowledge becomes even more critical. Remember: the fabricator is your partner.
MKS’ Atotech to Participate in IPCA Electronics Expo 2025
08/11/2025 | AtotechMKS Inc., a global provider of enabling technologies that transform our world, announced that its strategic brands ESI® (laser systems) and Atotech® (process chemicals, equipment, software, and services) will showcase their latest range of leading manufacturing solutions for printed circuit board (PCB) and package substrate manufacturing at the upcoming 17th IPCA Show to be held at Pragati Maidan, New Delhi from August 21-23, 2025.
MKS Showcases Next-generation PCB Manufacturing Solutions at the Thailand Electronics Circuit Asia 2025
08/06/2025 | MKS Instruments, Inc.MKS Inc, a global provider of enabling technologies that transform our world, today announced its participation in Thailand Electronics Circuit Asia 2025 (THECA 2025), taking place August 20–22 at BITEC in Bangkok.