-
- News
- Books
Featured Books
- pcb007 Magazine
Latest Issues
Current IssueInventing the Future with SEL
Two years after launching its state-of-the-art PCB facility, SEL shares lessons in vision, execution, and innovation, plus insights from industry icons and technology leaders shaping the future of PCB fabrication.
Sales: From Pitch to PO
From the first cold call to finally receiving that first purchase order, the July PCB007 Magazine breaks down some critical parts of the sales stack. To up your sales game, read on!
The Hole Truth: Via Integrity in an HDI World
From the drilled hole to registration across multiple sequential lamination cycles, to the quality of your copper plating, via reliability in an HDI world is becoming an ever-greater challenge. This month we look at “The Hole Truth,” from creating the “perfect” via to how you can assure via quality and reliability, the first time, every time.
- Articles
- Columns
- Links
- Media kit
||| MENU - pcb007 Magazine
Estimated reading time: 2 minutes
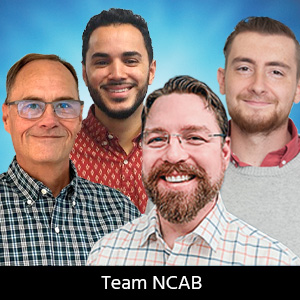
Fresh PCB Concepts: Pros and Cons of the 6 Most Common Surface Finishes
A surface finish can be defined as a coating, either metallic or organic in nature, that is applied to a PCB to ensure the solderability of the metal underneath. Most of the surface treatment dissolves into the solder paste or wave solder during the soldering process, and the solder joint is forming between the solder and the copper. One exception is ENIG/immersion gold, where the solder dissolves the thin layer of gold and forms a joint with the underlying nickel phosphorous alloy.
There are only two different types of surface finishes for PCBs: organic and metal. Here are the six most common finishes on the market:
- ENIG
- HASL leaded
- HASL lead-free
- Organic solderability preservatives (OSP)
- Immersion Sn
- Immersion Ag
OSP is more like a lacquer, which prohibits oxygen from attacking the copper underneath. All others are coating metals, and they may be applied using one of two different methods: electroless or immersion.
Electroless systems work in the same fashion; they use a reducing agent inside the bath itself. This means that the metal thickness increases during the whole period that the PCB is in contact with the solution.
An immersion systems process uses a chemical displacement reaction to deposit a metal layer onto the exposed metal surface of the PCB. The base metal donates the electrons that reduce the positively charged metal ions present in the solution. The immersion layer will continue to grow; however, as the thickness of the deposit increases, the rate of deposition falls. Therefore, the process is self-limiting.
Comparing both types and all available options can quickly demonstrate the relative benefits or drawbacks. Typically, the decisive factors when it comes to selecting the most suitable finish is the end application, the assembly process, and the design of the PCB itself.
For each of the six most common surface finish, these tables illustrate the pros and cons (Tables 1–6).
Table 1: ENIG pros and cons.
Table 2: HASL leaded pros and cons.
Table 3: HASL lead-free pros and cons.
Table 4: OSP pros and cons.
Table 5: Immersion Sn pros and cons.
Table 6: Immersion Ag pros and cons.
Conclusion
There is much more to understand about surface finishes. Each of the six surface finishes I mentioned has a different process for application, handling recommendations, storage conditions and time, baking requirements, thickness requirements, masking limitations and design considerations and concerns. Tables 1–6 are simply an overview. We always recommend discussing surface finishes with your PCB supplier as early as possible in the design stage.
Harry Kennedy is a field application engineer at NCAB Group.
More Columns from Fresh PCB Concepts
Fresh PCB Concepts: More Than Compliance—A Human-centered Sustainability ApproachFresh PCB Concepts: Assembly Challenges with Micro Components and Standard Solder Mask Practices
Fresh PCB Concepts: The Power of a Lunch & Learn for PCB Professionals
Fresh PCB Concepts: Key Considerations for Reliability, Performance, and Compliance in PCBs
Fresh PCB Concepts: Traceability in PCB Design
Fresh PCB Concepts: Tariffs and the Importance of a Diverse Supply Chain
Fresh PCB Concepts: PCB Stackup Strategies—Minimizing Crosstalk and EMI for Signal Integrity
Fresh PCB Concepts: PCB Plating Process Overview